Oil & Gas Supply Chain Trends: Insights & Innovations
- Digital Transformation
- Supply Chain
- Oil & Gas

Today’s oil and gas supply chain is defined by rising costs
and a highly competitive market.
As companies grapple with volatility and global uncertainty,
the need for resilience is greater than ever.
But the challenges are many.
That’s why industry leaders are turning to technology solutions to mitigate risk, enhance agility, and control costs.
In their 2024 report, oil and gas industry experts at
Captech Consulting also expect to see the influence of renewable energy, digital transformation, sustainability initiatives, and continued competition for limited resources impact the industry significantly.
To understand why, let’s explore the challenges in today’s oil and gas supply chain and how modernization is helping companies take the lead.
Key Players
It may come as no surprise that the United States is the leading producer of oil and natural gas.
According to the U.S. Energy Information Administration, In 2023, the United States reached a record-high crude oil production of 12.9 million barrels per day (b/d).
Behind the U.S. are Saudi Arabia, Russia, Canada, China, Iraq, the United Arab Emirates (UAE), Brazil, Iran, and Kuwait.
Top oil and gas companies include ExxonMobil, Shell, BP, Chevron, and Total, and national oil companies such as Saudi Aramco, and CNPC in China.
Major service providers include Schlumberger and Halliburton. Both provide specialized services and equipment for exploration and extraction. They also design and produce equipment for various processes, like exploration, extraction, and refining.
Understanding the Oil & Gas Supply Chain
The oil and gas supply chain involves three stages that work to turn natural elements into petroleum products from the source to the consumer. The stages include:
- Upstream
- Midstream
- Downstream
Stage 1: Upstream
Exploration and Extraction is the initial oil supply chain stage, which involves locating oil and gas reserves and drilling wells to extract these resources.
Furthermore, at this stage, operators are challenged with environmental regulations such as EPA, OSHA, and BSEE.
Consequently, many industry leaders are adopting modern techniques like 3D seismic imaging, horizontal drilling, and hydraulic fracturing to increase efficiency and reduce environmental impact.
Stage 2: Midstream
After extraction, midstream refers to the processing, storing, and transportation of oil and gas products.
- Processing: Distillation, cracking, and reforming to produce different petroleum products such as gasoline, diesel, jet fuel, and lubricants.
- Storing: Short-term storage facilities that balance supply and demand by temporarily holding crude oil and petroleum products.
- Transportation: Using tankers, pipelines, and trucks, to transport unrefined oil and final products
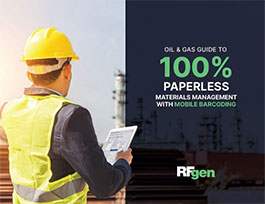
Oil & Gas Guide to Paperless Materials Management
GET THE GUIDE »Stage 3: Downstream
Downstream marks the final process of refining and distribution of petroleum products.
Refining is a subset of processing involving chemical engineering methods like blending, and purifying to make petroleum products market-ready.
Refineries use processes like distillation, cracking, reforming, and purification treatments to turn crude oil into usable products. Some are owned by oil companies, while others are independent operators.
Overseen by supply chain managers, Distribution involves getting finished products to primary consumers, businesses, and government agencies.
Key Business Challenges
Oil & Gas operators are faced with numerous challenges around production costs, MRO, and talent acquisition. Let’s take a look at how oil and gas manufacturers are navigating these challenges.
Controlling Production Costs
Geopolitical and global economic conditions make oil and gas prices volatile, with wide fluctuations in supply and demand.
To tackle this, companies are adopting several strategies to reduce risks and control costs. These strategies include adopting digital transformation technologies to increase resilience and predictability, engaging in strategic mergers and acquisitions, and adopting new sustainability measures, among others.
Optimizing Maintenance and Repair Costs of Critical Assets
Oil industry assets are typically complex, expensive, and require expertise to replace or repair. Parts must be strategically located and assets closely monitored to prevent excess machinery downtime.
Again, technology plays a major role in surmounting these challenges. Digitizing manual processes for more efficient work order completion in the field, leveraging technologies like IoT sensors and advanced analytics to collect real-time data, and equipping workers with mobile devices enable oil and gas companies to streamline costs and maintenance response times.
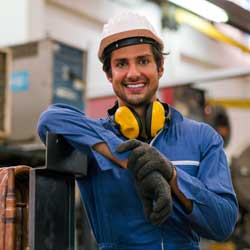
Explore the 3 Benefits of Mobile Work Order Management
DOWNLOAD NOW »Managing Fixed Assets
Another challenge is often locating fixed assets as most operators don’t log them consistently.
And with 70% of companies reporting lacking visibility into asset maintenance, they risk not having parts for critical repairs which can result in machinery downtime, delaying maintenance schedules, and financial loss. This can happen when using outdated manual processes to track parts.
Consequently, experts advise that unplanned downtime is directly driving digital transformation.
Companies are replacing manual data entry with real-time asset tracking software and mobile barcoding, which allows them to create new fixed assets in their ERP, and transfer and remove fixed assets from one location to another— all digitally.
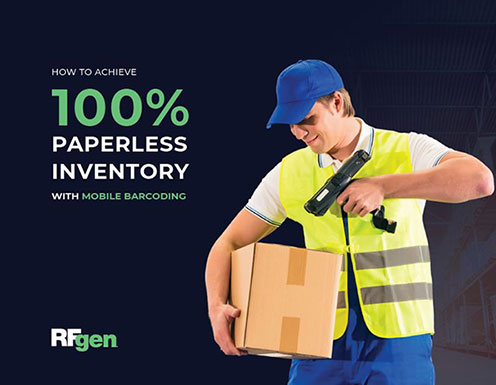
How to Achieve 100% Paperless inventory & Asset Tracking
GET THE GUIDE »Talent shortage
Oil and gas face a significant labor shortage—a problem that seems to be only getting worse. An aging workforce, talent competition, and skills gaps continue to be leading factors.
And as the industry is moving towards decarbonization and digitalization, businesses are struggling to find employees with the requisite technical skills.
To combat this, executives are strengthening their employee value proposition (EVP), with competitive compensation, and implementing more automation and new technology.
Technologies & Trends Impacting the Industry
Enhancing Employee Safety with Automation
Jobs in the oil and gas industry rank high in terms of dangerous professions, necessitating new ways to keep workers safe. Technology may provide the answer.
A recent study found that the adoption of automation technologies can decrease the number of workers exposed to hazardous conditions, thereby reducing injuries and fatalities by up to 25%.
The use of automation technologies in drilling operations such as:
- Robotic drilling and remote operations
- Sensors and control systems
- A.I. and machine learning
Therefore, integrating automated systems eliminates manual operations in high-risk environments, reducing risks of injury.
Additionally, it gives operators the oversight and visibility to make informed data-driven decisions.
Transition to Renewable Energy and Sustainability
The oil and gas industry is increasingly shifting toward renewable energy sources, mostly due to climate change concerns and government incentives.
Today’s forward-thinking industry players are investing in low-carbon technologies and IoT solutions to drive real-time monitoring, improve operational efficiency, and address environmental concerns.
Not to mention that adopting sustainable supply chain practices can position organizations for long-term success in the global energy market.
Digital Transformation
As with many other industries, oil and gas continues to focus on digital transformation efforts to combat rising costs and the unexpected.
For most, this involves replacing manual processes, paper printouts, and data entry with digital automation technologies. These range from mobile inventory solutions for real-time materials management to AI and machine learning for analyzing collected data.
By digitizing tedious tasks, companies can accurately collect and assess data, disrupt information siloes, and prioritize accurate decision-making and forecasting.
Mobilizing the Workforce
Today’s workforce is more mobile than ever. Top performers in oil and gas are equipping their workforce with mobile devices to increase operational efficiency and nimbleness.
For example, workers can use ruggedized mobile devices to locate parts and documentation for a maintenance work order in the field.
In a warehouse or production facility, implementing mobile barcoding can extend ERP functionality to point-of-work. Workers can scan inventory or materials in any location to process transactions instantly, enabling real-time visibility.
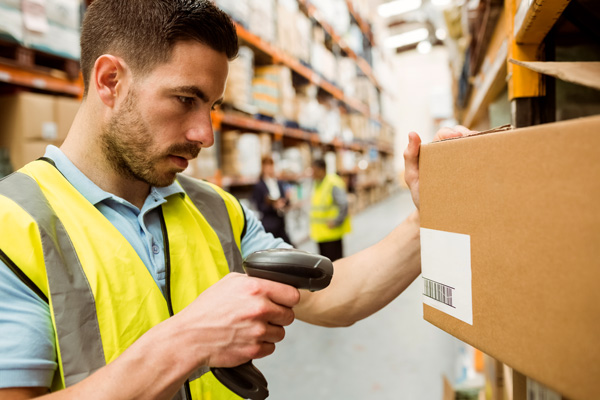
The Crucial Role of Mobile Data Collection in the Oil and Gas Industry
READ NOW »Investment in LNG (Liquefied Natural Gas)
A variety of economic and environmental factors are driving a toward Liquefied Natural Gas (LNG). Liquified natural gas is natural gas that’s been cooled, allowing it to be shipped safely and efficiently abroad.
Increasing the prevalence of LNG is also a win for consumers as it promises environmental advantages like improved air quality.
As a result, the development of LNG infrastructure and projects will continue or expand as global distributors seek greener ways to transport gas across long distances.
Case Study: Global LNG Exporter Digitizes Supply Chain
After a company merger, a Global LNG Exporter shifted ERPs and, in the process, lost their barcoding functionality, forcing them to revert to managing MRO spare parts inventory with paper processes.
Knowing that manual inventory wasn’t sustainable, they sought a new barcoding solution that would allow them to digitize their supply chain process and operate more competitively.
After partnering with RFgen, they were able to digitally transform paper processes with mobile barcoding.
As a result, they automated spare parts inventory management for MRO, reduced operating costs from real-time visibility, and achieved 75-93% shorter training time for new employees.

Global LNG Exporter Reduces Operating Costs
READ THE FULL STORY »Looking to the Future of Oil & Gas — Automation
Oil and gas remains a highly competitive market beset by numerous challenges. As the industry prioritizes decarbonization, enhancing employee safety, and talent acquisition and retention, digital transformation with technology remains the primary vehicle to get there.
To that end, oil and gas leaders must embrace the move toward automation to increase resilience and future-proof their supply chain. Those hesitant to adapt won’t have the business agility to match bolder competitors eager to get ahead by adopting innovative technology solutions.
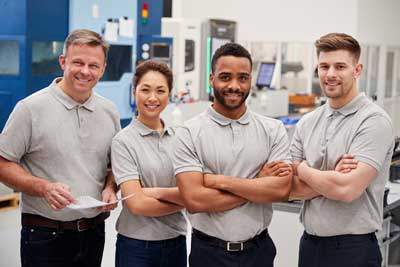