Effective Strategies for Scaling Manufacturing Operations
- Supply Chain
- Manufacturing
- Automation
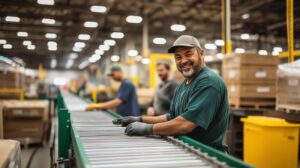
Scaling manufacturing operations is crucial for business growth but presents unique challenges. Balancing increased demand with consistent quality and controlled costs is difficult but essential for manufacturers looking to expand.
Successfully scaling manufacturing requires more than just adding resources. It’s about building adaptable systems, establishing clear performance indicators, and implementing processes that can handle growth spurts and market fluctuations. This requires a strategic approach focused on efficiency, quality control, and sustainable growth.
This guide covers the key elements of successful manufacturing scaling:
- Understanding manufacturing scalability and its core components
- Assessing your current capabilities
- Developing a strategic growth plan
- Implementing technology and automation solutions
- Optimizing operations for sustainable growth
- Measuring and evaluating your scaling success
This post will provide a practical roadmap to scale manufacturing operations and achieve sustainable business growth.
4 Ways RFgen Mobile Apps Help You Get More Out of Oracle SCM Cloud
READ MORE »Understanding Scaling Manufacturing
The manufacturing business relies on scalability to increase production output efficiently without a proportional increase in costs. A truly scalable operation can handle increased volume while remaining cost-effective and delivering consistent product quality.
Key Components of Scalable Production
Several key elements contribute to a scalable manufacturing operation:
- Flexible Manufacturing Equipment: Your equipment should leverage technology to be adaptable, allowing quick adjustments to output levels as demand changes. This agility minimizes downtime and maximizes resource utilization.
- Advanced Automation Systems: Seamless integration of automation is essential for agile manufacturing. These systems should complement existing processes, allowing incremental capacity expansion without disrupting current operations.
- Supply Chain Resilience: Strategic partnerships with reliable suppliers guarantee consistent material availability, regardless of production scale. This reliability prevents bottlenecks and keeps production flowing smoothly.
- Modular Production Lines: Implementing modular production lines allows for independent scaling of specific processes. This targeted approach optimizes resource allocation and minimizes bottlenecks by allowing you to scale only where necessary.
Expanding production capabilities is essential for increasing efficiency and ensuring a strong market presence.
Common Challenges in Scaling Manufacturing Operations
While the benefits of scalability are clear, several challenges must be addressed:
- Space Constraints: Physical limitations can hinder expansion plans. Optimizing existing layouts and exploring alternative locations may be necessary.
- Resource Allocation: As production grows, effectively scheduling your workforce and utilizing equipment in response to market demand becomes increasingly critical.
- Quality Control: Higher volumes create more opportunities for defects. Maintaining quality assurance requires robust quality control systems and rigorous monitoring.
- Supply Chain Vulnerabilities: Your suppliers need to scale with you. Dependencies on suppliers who can’t meet increased demand can lead to material shortages and production delays.
- Transportation and Logistics: Increased production volume complicates logistics. New solutions for material handling and finished product distribution are often required.
- Energy Consumption: Scaling production typically increases energy use, which can significantly impact operating costs.
- Training Requirements: Introducing new equipment and processes necessitates workforce training to ensure smooth transitions and maintain productivity.
- Documentation and Compliance: Larger-scale operations require more complex documentation and compliance procedures.
- Infrastructure Limitations: Existing infrastructure, including utilities, data networks, and support systems, may struggle to handle increased demand. Upgrades and expansions may be necessary.
- Coordination of Multiple Shifts: Managing multiple production shifts introduces new challenges in maintenance scheduling and equipment downtime.
- Material Flow: Optimize material flow patterns to accommodate increased volume without creating bottlenecks or excessive inventory.
- Environmental Impact: Larger-scale production has a greater environmental footprint.
Addressing these challenges is crucial for the long-term success of any manufacturing business looking to scale.
Assessing Current Manufacturing Capabilities
Before scaling, thoroughly assess your current production capabilities and manufacturing capabilities. This involves analyzing production capacity, equipment effectiveness, and resource utilization to identify opportunities and potential bottlenecks. A comprehensive assessment provides a solid foundation for informed scaling decisions.
Production Capacity Analysis
While traditional testing methods can be time-consuming and offer incomplete data, focusing on key production metrics within the manufacturing process provides more actionable insights. Consider these essential metrics:
- Asset Utilization: How efficiently are your machines being used? Track machine runtime to understand and optimize utilization rates.
- Throughput: Measure the number of units produced per hour to gauge your current output capacity.
- Maintenance Time: Track equipment downtime to identify maintenance needs and improve production reliability.
- Quality Control: Monitor defect rates to understand product consistency and identify areas for improvement.
Analyzing these metrics gives a clearer picture of your current production health and efficiency, highlighting areas for improvement before scaling begins. It’s better to address potential bottlenecks before they impact expanded operations.
Resource Utilization Assessment
Adopt a utilization-focused approach to production management, even in low-volume, highly engineered environments. This involves careful planning and optimization across all resources. Consider the following:
- Existing Stock Keeping Units (SKUs): Manufacturing companies should analyze their current inventory levels and how they align with anticipated demand.
- Pipeline Products: Factor in upcoming product launches and how they will impact resource needs.
- Seasonal Customer Requirements: Account for any seasonal fluctuations in demand to ensure you can meet peak periods.
- Equipment Configuration Capabilities: Understand the flexibility and limitations of your current equipment.
- Current Facility Space Utilization: Evaluate how effectively you are using your existing space.
When considering physical expansion, explore whether you should acquire additional manufacturing space, upgrade existing facilities or invest in new equipment. Don’t forget to factor in lead times for equipment installation and potential disruptions during transitions.
The Impact of Cloud Migration on Data Collection Software
LEARN MORE »Strategic Planning for Scale
Strategic planning, incorporating digital transformation, is the cornerstone of successful manufacturing expansion. A data-driven approach ensures systematic, sustainable growth. Strategic planning should also focus on expanding production capabilities to meet increasing market demands.
Setting Clear Objectives
Scaling objectives should be specific and measurable. Industry leaders emphasize the importance of defining clear production targets using quantifiable metrics and identifying critical expansion points, including production volume increases, space utilization rates, and equipment efficiency targetsAnalyze data from historical performance, demand forecasts, and capacity constraints to determine optimal scaling patterns. Establishing clear performance indicators helps track progress towards expansion goals while maintaining quality standards.
Developing a Growth Roadmap
A well-defined roadmap provides a structured approach to expansion, minimizing disruption and maximizing efficiency.
- Technical Roadmap: Leading manufacturers guide the implementation of scaling initiatives across all manufacturing operations. The architecture should anticipate future expansion requirements, ensuring seamless integration of new production sites, users, and systems. This allows for the creation of reusable components, applications, and data pipelines that support continued growth.
- Organizational Scalability: Template-based role structures enhance organizational scalability by providing clear frameworks for staffing new facilities. This simplifies the process of identifying qualified personnel and ensures consistency across locations. Each expansion phase should follow established patterns, while allowing for site-specific adjustments.
- Infrastructure Planning: Proactively plan your technical infrastructure to support future solution development, user growth, and facility additions. Use case analyses help define essential features and functionality requirements, ensuring the infrastructure can accommodate future demand.
- Cross-Functional Coordination: Ensure all departments are aligned. Production, technology, and organizational structure should all support the overall scaling strategy. Regularly review the roadmap, adjusting as needed based on changing market conditions, operational insights, and technological advancements. This iterative planning process maintains focus while allowing for flexibility.
Digital Transformation and Automation Solutions
Technology and automation streamline manufacturing processes, enhancing operational efficiency and quality management, reducing manual labor, and significantly improving overall productivity.
Smart Manufacturing Technologies
Smart manufacturing combines the power of real-time data analysis with automated systems to enhance the production process and capabilities. Connected devices monitor equipment performance, enabling predictive maintenance that minimizes downtime. This data feeds into machine learning algorithms, which optimize resource allocation for maximum efficiency.
AI systems can even adjust manufacturing parameters in real time, ensuring consistent product quality and optimal output. These technologies significantly enhance production capabilities, allowing for more efficient and scalable operations.
Process Automation Opportunities
Process automation transforms manual manufacturing operations into streamlined, efficient workflows. Robotic systems handle repetitive tasks with precision and consistency, minimizing human error and maintaining uniform quality across production runs. Automated quality control measures, often integrated directly into advanced manufacturing equipment, detect defects early in the production cycle, reducing waste and improving overall product quality.
For efficient inventory management, IoT sensors automate tracking and trigger material orders when supplies reach predetermined thresholds, preventing shortages and delays. Automated scheduling systems further optimize production sequences, taking into account equipment availability, material requirements, and delivery deadlines.
To simulate and test process modifications without disrupting active production, digital twin technology provides a virtual environment for experimentation and optimization. Finally, integrating your ERP system automates data collection across all manufacturing operations, offering real-time visibility into critical performance metrics. This data flows into automated reporting systems, tracking KPIs and generating insights for continuous process improvement.
What to Know About Mobile Security with Cloud ERP
LEARN MORE »Optimizing Operations for Growth
Optimizing operations in the manufacturing sector requires a strategic approach to improving supply chain logistics, strengthening quality control systems, and developing a skilled and adaptable workforce.
Optimizing operations is essential for any manufacturing business aiming to scale successfully.
Supply Chain Management
Start with comprehensive supplier assessments, focusing on reliability, scalability, and potential risks. Implement just-in-time inventory practices to reduce carrying costs while maintaining a consistent flow of materials. Mitigate disruptions by diversifying procurement channels through a multi-sourcing strategy. Real-time supply chain monitoring, facilitated by integrated software systems, enables proactive issue resolution, accurate inventory tracking, and streamlined delivery coordination. For critical parts, conduct detailed risk assessments that consider supplier capacity, performance history, and financial stability, ensuring the availability of essential components when you need them most.
Quality Control Systems
Automated inspection systems, leveraging machine vision and sensor technology, dramatically improve defect detection rates. Statistical process control (SPC) methods identify variation patterns, allowing for timely corrective actions before issues impact output. Comprehensive documentation systems track quality metrics across all production runs, providing valuable data-driven insights for continuous improvement initiatives. Regular calibration protocols and standardized testing procedures further ensure accurate measurements and consistent quality across all expanded operations.
Workforce Development
Cross-training programs develop a versatile team capable of handling multiple responsibilities, providing flexibility and resilience. Standardized work instructions improve consistency and help preserve institutional knowledge, ensuring that best practices are maintained as the team grows. Implement skills matrices to track employee capabilities and proactively identify training needs, ensuring adequate coverage for all critical operations.
Technical certification programs help develop specialized expertise in areas like equipment operation, maintenance, and troubleshooting. Mentorship programs provide valuable on-the-job training and accelerate skill development by pairing experienced operators with newer team members.
Performance monitoring systems offer data-driven feedback for continuous improvement, empowering employees to enhance their skills and contribute to overall operational efficiency. Digital training platforms provide consistent instruction across multiple shifts and locations, ensuring standardized training for everyone. Document standard operating procedures (SOPs) for knowledge transfer as operations scale, preserving best practices and ensuring consistency. Equipping team leads with management training focused on production scheduling, resource allocation, and performance optimization prepares them to effectively manage growing teams and resources.
Finally, establishing clear career development paths helps maintain employee engagement and motivation during periods of expansion, fostering a positive and productive work environment. Regular skill assessments further identify any gaps in capabilities, guiding targeted training investments and maximizing the effectiveness of workforce development initiatives.
Measuring and Analyzing
Measuring the success of your scaling initiatives involves tracking key performance indicators (KPIs) and conducting thorough return on investment (ROI) analyses. Data-driven evaluation provides valuable insights into the effectiveness of your scaling strategies and informs future decisions.
Performance Metrics
Tracking relevant performance metrics that offer insights into various aspects of your operations, from equipment effectiveness to overall productivity. Focus on these key indicators:
- Overall Equipment Effectiveness (OEE): OEE measures the availability, performance, and quality of your equipment.
- Production Cycle Time: This metric tracks the time it takes to produce one unit, from start to finish. Analyzing cycle time helps identify bottlenecks and inefficiencies in your scaled processes.
- Defect Rates: Monitoring defect rates is crucial for ensuring that quality standards are maintained as production increases..
- Capacity Utilization Rate: This metric indicates how effectively you are using your expanded resources.
- Manufacturing Lead Time: Track the time it takes from order receipt to delivery to assess the efficiency of your supply chain throughout the scaling process.
- Labor Productivity: Measure units produced per labor hour to evaluate workforce performance across expanded operations.
- Energy Consumption per Unit: This metric helps evaluate the sustainability of your scaled production and identify opportunities for energy efficiency improvements.
- Inventory Turnover Rate: Inventory turnover reveals how effectively your supply chain optimization strategies are working.
Creating Native Mobile Inventory Apps for SAP
DOWNLOAD NOW »ROI Evaluation
Calculating ROI provides a financial assessment of your scaling investments. Use a variety of financial indicators to gain a comprehensive understanding of your returns.
- Payback Period: This analysis determines the time required to recoup your initial scaling investments.
- Net Present Value (NPV): NPV calculations factor in the time value of money, using discount rates specific to manufacturing investments.
- Cost per Unit: Comparing pre-scaling and post-scaling cost per unit, including materials, labor, and overhead, reveals the cost-effectiveness of your scaling efforts.
- Margin Improvements: Analyze margin improvements resulting from economies of scale. Scaling often leads to cost reductions through volume efficiencies.
- Capital Expenditure: Measure the return on investment for capital expenditures like new equipment and facilities.
- Market Share Gains: Quantify revenue growth attributed to increased production capacity to understand the impact of scaling on market share.
- Customer Satisfaction: Ensure that scaling efforts don’t negatively impact customer satisfaction. Maintain high satisfaction rates to preserve customer loyalty.
- Revenue per Employee: This metric helps evaluate improvements in workforce efficiency resulting from scaling.
- Contribution Margin Ratio: This ratio indicates profitability improvements from scaling by considering variable costs against revenue increases.
- Working Capital Efficiency: Monitor working capital efficiency through cash conversion cycle measurements. This ensures that scaling investments don’t negatively impact operational liquidity.
- Break-Even Analysis: Conduct break-even analyses to determine the production volume required for profitability at different scaling stages, accounting for new fixed cost structures.
Conclusion
Scaling manufacturing operations is a complex undertaking, requiring a strategic blend of careful planning, innovative technology, and robust measurement systems. Success hinges on maintaining quality while increasing output, achieved through smart automation and data-driven decision-making. It’s a balancing act, requiring a methodical approach and a commitment to continuous improvement.
Simply adding resources isn’t enough. True scalability comes from building adaptable systems, establishing clear metrics, and implementing processes that can handle both growth and market fluctuations. This includes optimizing your supply chain, ensuring quality control at every stage, and investing in your workforce. Technology and automation play a critical role, from smart manufacturing systems that provide real-time insights to process automation that streamlines workflows and reduces manual labor.
By embracing these principles and maintaining a focus on measurable outcomes, manufacturers can position themselves for long-term success in a competitive market. The future of manufacturing belongs to those who can effectively balance innovation with operational excellence as they expand their capabilities.
Frequently Asked Questions
What is manufacturing scalability?
Manufacturing scalability is a company’s ability to increase its production output efficiently without a proportional increase in costs. It involves building adaptable and flexible systems that can handle larger production volumes while maintaining quality and controlling expenses. A scalable manufacturing operation can readily respond to fluctuations in demand and changing market conditions.
What are the key challenges in scaling manufacturing operations?
Scaling manufacturing operations presents several key challenges. These include space constraints, the growing complexity of resource allocation, maintaining quality control with increased output, potential supply chain disruptions, more complicated logistics, rising energy consumption, increased training requirements, more intricate compliance procedures, and the possibility of reaching infrastructure limitations. Successfully navigating these challenges is essential for achieving sustainable growth.
How can technology help in scaling manufacturing operations?
Technology is a key enabler of successful scaling in manufacturing. Smart manufacturing systems, automation technologies, and digital twins can significantly enhance scaling efforts. These solutions offer the potential to reduce downtime, increase production efficiency, improve quality control through real-time monitoring, and optimize processes for greater throughput and resource utilization.
What metrics should be tracked when scaling manufacturing?
When scaling manufacturing, track key metrics that offer insights into your operational performance. These include Overall Equipment Effectiveness (OEE), which measures equipment availability, performance, and quality; Production Cycle Time, which tracks the time required to produce one unit; Defect Rates, monitoring the frequency of product defects; Capacity Utilization, measuring how effectively resources are used; Manufacturing Lead Time, tracking the time from order to delivery; Labor Productivity, measuring units produced per labor hour; Energy Consumption per Unit, tracking energy efficiency; and Inventory Turnover Rate, which measures how well inventory is managed.
How important is strategic planning in manufacturing expansion?
Strategic planning is absolutely vital for successful manufacturing expansion. It provides a structured roadmap for growth, ensuring efficient resource allocation and alignment between scaling activities and overall business objectives. Effective strategic planning involves a data-driven approach, clearly defined objectives, and a detailed implementation roadmap.
What role does workforce development play in scaling operations?
Workforce development plays a crucial role in scaling manufacturing operations. A well-trained and adaptable workforce can handle the increased demands and complexities that come with larger-scale operations. Cross-training, standardized work instructions, and the use of digital training platforms are key components of building a workforce capable of supporting growth.
How can quality control be maintained during scaling?
Maintaining quality control during scaling requires implementing robust systems and procedures. Automated inspection systems, statistical process control methods, and comprehensive monitoring protocols are essential for preventing defects, reducing waste, and ensuring consistent adherence to quality standards, even as production volumes rise.
What factors determine successful production scalability?
Successful production scalability depends on a combination of factors. These include having flexible and adaptable equipment, implementing advanced automation technologies, establishing strong supply chain partnerships with reliable suppliers, optimizing resource utilization for maximum efficiency, implementing robust quality control systems, ensuring accurate demand forecasting, and utilizing systematic performance measurement for data-driven optimization.