4 Strategies for Maximizing Warehouse Safety
- Compliance
- Inventory/Warehouse
- Workforce
In today’s world of speedy supply chain fulfillment and chronic labor shortages, it’s more important than ever to ensure worker safety in the warehouse. The Bureau of Labor Statistics reports that 5.5% of warehouse employees suffer a workplace injury each year, and 4.6% have had to take time off work or be transferred to a different facility as a result.
Understandably, companies want to reduce this number by having effective safety measures in place. Policies that enforce government and OSHA regulations, facility design, and warehouse ergonomics are all strategies that work toward a safer facility without impacting operational efficiency.
So if you’re wondering how to improve warehouse safety, here are some valuable warehouse safety tips from the experts:
Develop a Culture of Safety
According to Gary Gagliardi, vice president of Safety Resources, managers and workers need to come together to understand challenges related to safety in the warehouse and come up with solutions.
“Companies need a culture of safety,” Gagliardi told Inbound Logistics. “Creating a safe work environment requires a good deal of effort, but it brings benefits to both workers and management.”
This culture of safety will help managers and workers alike understand their unique challenges and develop a plan of action to tackle workplace concerns. But safety culture doesn’t arise naturally. It requires dedicated fostering of worker and management engagement.
A safer warehouse work environment benefits everyone. Employees feel more secure and cared for, leading to greater vigilance, job satisfaction, and tenure. Meanwhile, managers can reduce team shortages due to injuries. The company benefits by reducing overhead costs and the indirect expenses associated with safety penalties or medical claims.
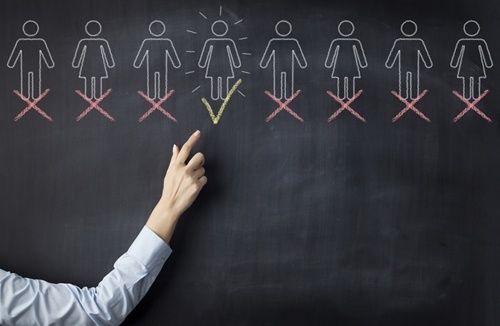
Addressing Talent Acquisition in the Supply Chain
READ NOW »Physical Infrastructure & Equipment Safety
Warehouse Safety Signs & Visibility Solutions
Even small design improvements to increase visibility can contribute to a safer work environment. Health Safety Training Limited lists numerous possible solutions to visibility concerns, from floor marking tape to bright clothing to luminescent safety signs.
A well-placed sign can prevent injuries when hazards are present, even in a digital warehouse. However, when placing signs, don’t overdo it. Too many signs and employees may be liable to ignore them.
Building & Structural Safety
The structural integrity of the warehouse is a factor in safety. Regular inspections can identify issues such as cracks, leaks, or potential collapse risks. Floors should be free from tripping hazards while roofs should have adequate drainage to prevent pooling when it rains.
Shelving & Storage Systems
Shelving systems are the backbone of the warehouse. Investing in high-quality systems ensures that they can bear the weight of the stored items. Additionally, regular maintenance checks can preempt potential failures. Every shelf should have clear weight capacity labels to prevent overloading as well as a safe means of access for storing and removal.
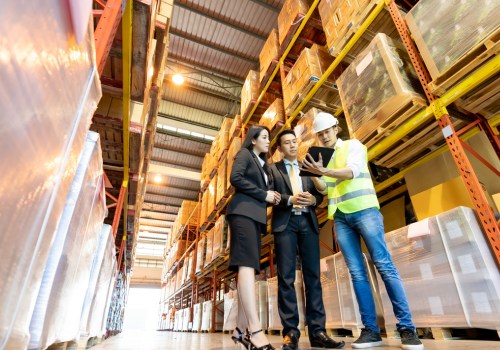
4 Tips for Spring Cleaning Your Warehouse
READ MORE »Equipment & Machinery
Today’s warehouses employ more equipment and machinery than ever, such as forklifts, conveyor belts, and pick-to-light technologies. However, poorly maintained equipment presents a significant hazard. Implementing regular maintenance schedules and ensuring that all workers are trained to operate them can significantly reduce accidents.
Environmental & Ergonomic Considerations
Lighting & Ventilation
Adequate lighting ensures that workers can see potential hazards. Moreover, proper ventilation can reduce hazards, especially in warehouses storing chemicals or perishables. Investing in energy-efficient lighting can also bring down operational costs.
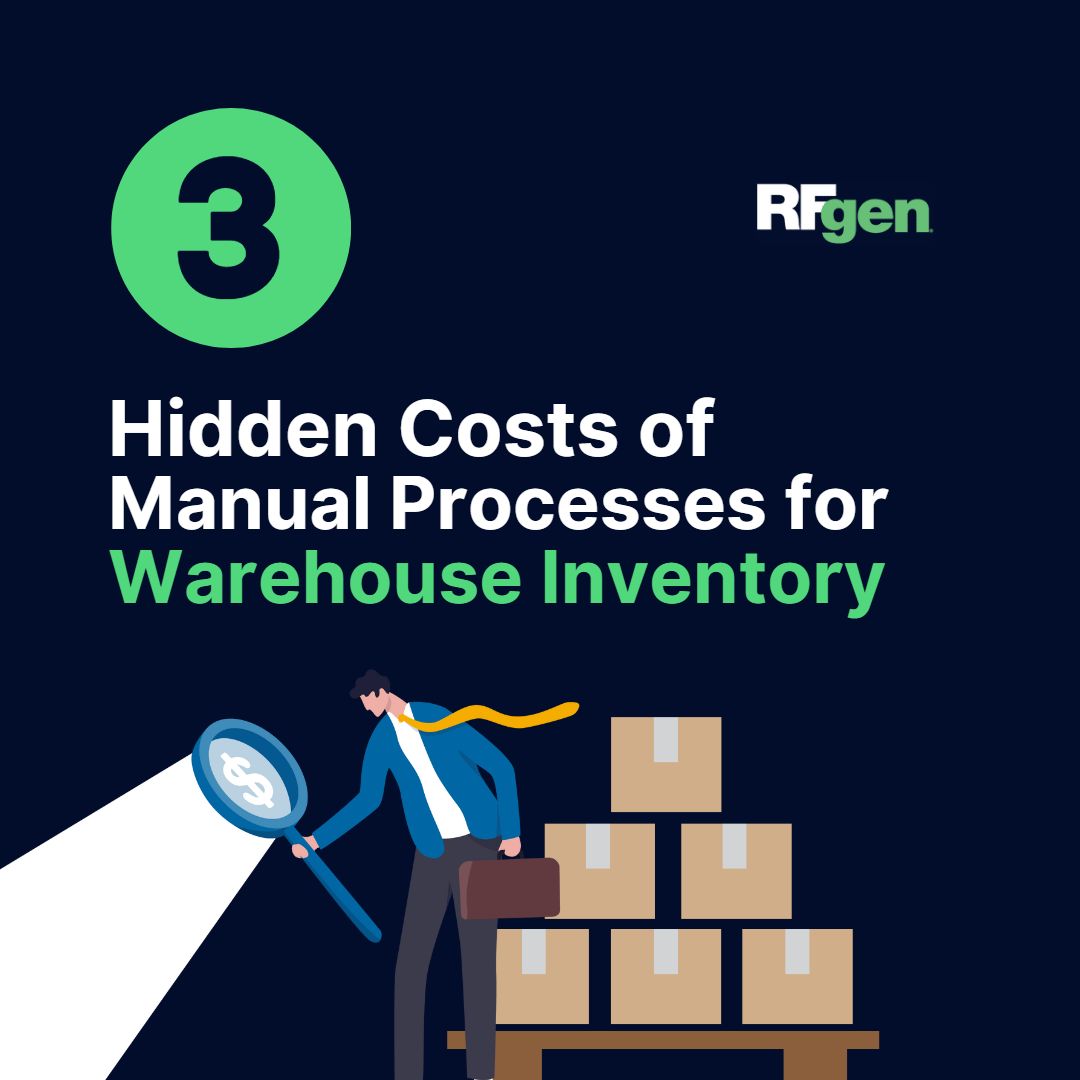
3 Hidden Costs of Manual Warehouse Processes
DOWNLOAD NOW »Ergonomics in the Warehouse
Repeated strain can lead to long-term injuries. Ergonomically warehouse equipment and tools can prevent this. Warehouse safety training on proper lifting techniques and providing equipment like weight belts can also go a long way in reducing strain-related injuries.
Using mobile devices for warehouse processes can reduce strain from repetitive motions and data entry, while lowering the chances of injury from overreaching, climbing, and falls.
Operational Protocols & Procedures
Implementing and enforcing appropriate policies is the most basic step to ensuring the safety of warehouse workers. The Occupational Safety and Health Administration enforces strict regulations. Companies are required to follow these regulations, and your policies should reflect their guidelines.
The most common types of workplace accidents include slips, trips, and falls; lifting and reaching pains; and material handling accidents like dropped boxes and forklift incidents. Make sure your safety policies touch on all of these kinds of accidents.
Loading & Unloading Protocols
Loading docks are a hive of activity but also potential danger zones. Implementing guidelines, such as designating specific areas for loading/unloading and using equipment like dock levelers, can enhance safety. Workers should also be trained to handle goods without causing damage or injury, particularly with forklifts.
Inventory Management
While it might seem unrelated to safety, effective inventory management can prevent many hazards. Overstocking can lead to items falling off shelves, while poor stock rotation can lead to decay or degradation of some goods. Regular inventory checks can prevent such issues. Manual cycle counts increase the risk of inventory-related accidents.
Automating manual processes with mobile inventory solutions can increase safety in all these areas.
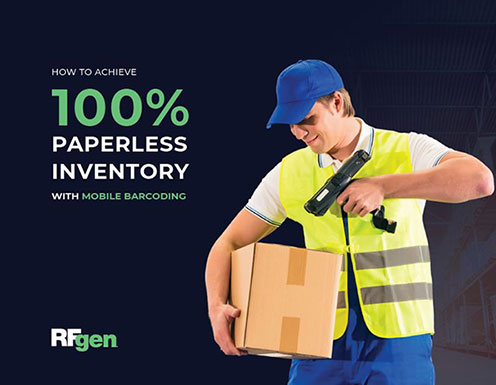
How to Achieve 100% Paperless Inventory with Mobile Barcoding
LEARN MORE »Emergency Response Procedures
Every warehouse should have clear, visible signage indicating emergency exits. Workers should be trained in fire safety protocols, including the use of extinguishers, eyewash stations, and the locations of assembly points. Conducting periodic evacuation drills ensures that everyone knows how to react in emergencies.
Personnel Safety & Training
Safety Training Programs
Training is the cornerstone of warehouse safety. Regular sessions can educate workers on potential hazards, how to avoid them, and what to do if they encounter one. Specialized training, like how to operate a particular machine or handle specific chemicals, should also be mandated.
The end goal should be to inculcate warehouse safety best practices so that safe behaviors come naturally.
Personal Protective Equipment (PPE)
PPE like helmets, gloves, and safety shoes are essential. Ensuring that workers have access to quality PPE and are trained in their correct usage can significantly reduce the risk of injury. Periodic checks can ensure that these are in good condition.
Mobile devices have been emerging as a new form of PPE to assist workers in doing their jobs safely and efficiently.
Continuous Monitoring & Feedback
Safety Audits
Just as businesses have financial audits, safety audits are crucial. These can identify potential hazards, evaluate the effectiveness of safety measures, and recommend improvements. In addition to internal audits, having third-party safety audits can provide an unbiased perspective to further enhance safety in the workplace.
Feedback Mechanisms
Creating a culture where workers can voice their concerns without fear of repercussions can lead to valuable insights. Digital platforms or suggestion boxes can be avenues for employees to report potential hazards or suggest improvements. Encourage staff members to voice their concerns at safety meetings as well as contribute to potential solutions.
Use Technology & Innovation in Warehouse Safety
Safety Management Systems
Modern technology has made safety easier to manage. Systems that track safety metrics, analyze data for patterns, and send alerts can be invaluable. Integrating these with other operational software can also enhance efficiency.
Mobile solutions like RFgen Mobile Edge™ can automatically track critical warehouse KPIs to assist with data collection.
Advanced Mobile Devices
Beyond handheld phones, industrial mobile solutions like vehicle-mounted rugged tablets and wearable devices can offer innovative solutions to safety hazards. Vehicle-mount devices enable forklift drivers to stay safely focused on the task at hand. Similarly, wearables like VR headsets and voice-picking solutions ensure employees aren’t looking down or getting too distracted to notice potential hazards.
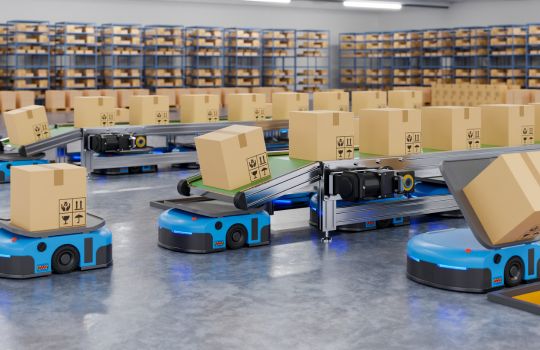
Enhance Safety with Advanced Directed Movement
LEARN MORE »Automation & Robotics
Robots and automated systems can handle tasks that are dangerous for humans. For several years, co-bots have been in use to assist with transporting boxes throughout the warehouse—a role that continues to be used by conveyor systems. However, it’s essential to ensure that there are safety protocols in place for human-robot coordination. As technology evolves, staying updated can also offer newer, safer ways of handling other warehouse operations.
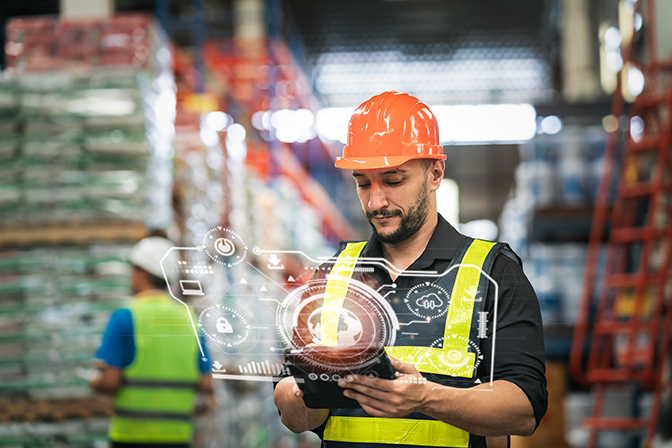
Getting Started with Warehouse Automation
READ MORE »Maximizing Warehouse Safety Pays Dividends
A safer warehouse means more productive workers and a lower chance of accidents. From the very infrastructure to the processes and the people, a holistic approach to safety ensures not just compliance but a more efficient, productive, and harmonious work environment with lower costs.
Beyond technology solutions like PPE and enterprise mobility, encourage continuous improvement and reinforce a culture of safety. And while every warehouse will have its unique challenges, investing in safety is an investment that always pays off, both in terms of cost and human well-being.