5 Supply Chain Factors for Effective Supply Chain Optimization
- Inventory/Warehouse
- Supply Chain
Key Takeaways
- Supply chain optimization is critical in the face of disruptive market conditions.
- Inventory management in the supply chain, coupled with automated technologies, can help boost efficiencies.
- A mobile supply chain will help deliver better data and increase visibility across all inventory.
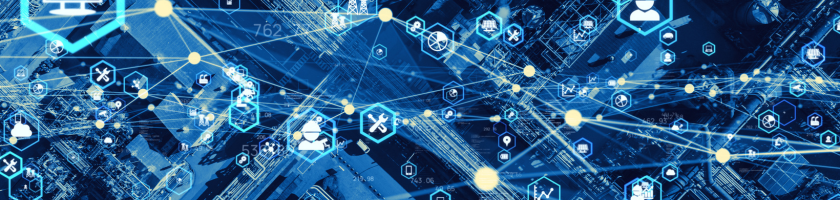
The modern supply chain faces unprecedented complexity. Businesses continuously adapt to shifting consumer demands, material shortages, and increasing digitization pressures. Simultaneously, they must strike the delicate balance between efficiency and resilience to ensure that disruptions—whether from supplier delays, fluctuating costs, or regulatory changes—don’t derail operations.
For inventory-heavy organizations, the challenge extends beyond basic logistics management. Every decision must be backed by accurate, real-time data. A supply chain optimized for efficiency, automation, and comprehensive visibility is essential for maintaining competitive advantage. The ability to track materials, control costs, and standardize processes allows companies to mitigate disruptions with agility, ultimately improving profitability and customer satisfaction.
While no single strategy can eliminate all supply chain challenges, certain factors consistently contribute to better outcomes. Organizations that prioritize data-driven decision-making, automation integration, high-value asset tracking, regulatory compliance, and workforce efficiency position themselves to manage disruptions and enhance overall performance effectively.
The following five key supply chain factors drive optimization and create the foundation for an agile, reliable, and cost-effective supply chain ecosystem.
1. Important Supply Chain Metrics
Data-driven decision-making forms the cornerstone of supply chain excellence. Measuring efficiency through key performance indicators provides the insights necessary to optimize operations from warehouses to distribution centers.
Effective supply chain analytics depend on tracking several critical measurements:
- Inventory turnover rates measure how quickly stock moves through your system. High turnover indicates efficient inventory management, while low rates signal excess stock, forecasting errors, or supply chain inefficiencies.
- Automated identification and data capture (AIDC) implementation reflects your organization’s commitment to error reduction. Higher AIDC adoption through barcode scanning and RFID tracking enhances order accuracy and inventory visibility while reducing manual processing errors.
- Granular cost tracking for high-value supplies enables precise budget allocation and material usage assessment. This detailed approach to cost management facilitates better forecasting and minimizes waste.
- Standardized product identifiers, including SKUs, lot numbers, and serial numbers, establish the foundation for comprehensive traceability. Consistent product labeling streamlines procurement, inventory management, and compliance reporting while reducing stock mismanagement risks.
While tracking these metrics is essential, the real value lies in automation. Manual data entry introduces errors and delays compromising reporting accuracy and decision quality. Companies implementing automated inventory management systems collect real-time data across their entire supply chain network. This automation improves accuracy and integrates directly with Enterprise Resource Planning (ERP) systems, enabling confident, data-backed decision-making at all levels of the organization.
How Mobile Barcoding Helps with Supply Chain Issues
RELATED »2. Inventory Management Automation Solutions
As supply chains expand and customer expectations intensify, efficient inventory management becomes increasingly challenging. Organizations handling substantial stock volumes must ensure accurate tracking, timely replenishment, and seamless accessibility across warehouses, distribution centers, and retail locations. Traditional manual tracking methods inevitably lead to costly errors, from misplaced products to inaccurate counts, making automation technologies indispensable for supply chain optimization.
Automated inventory solutions deliver multiple strategic advantages:
- Enhanced perishable inventory management ensures compliance with expiration dates and safety regulations—particularly crucial in healthcare and food production, where improper storage or delays can result in significant financial losses.
- Accelerated traceability and recall management capabilities minimize financial exposure when dealing with expired or recalled products. Automated systems enable immediate identification and removal of affected inventory, preventing costly operational disruptions and potential regulatory penalties.
- Strategic workforce allocation shifts employees from manual data entry to higher-value activities such as quality control, supplier management, and process improvement initiatives.
- Comprehensive supplier and procurement visibility provides accurate insights into purchase patterns, inventory levels, and demand trends. This intelligence helps organizations avoid overordering, reduce carrying costs, and strengthen supplier negotiations.
According to the RFgen Digital Inventory Report, a mere 16% of participants believe their company’s mobile automation systems adequately meet their current needs. Without proper capture and standardization via mobile supply chain management, organizations cannot collect the high-quality data essential for effective decision-making.
Implementing automation technologies and supply chain optimization software drives efficiency, agility, and productivity gains, translating into significant time and cost savings throughout the operational ecosystem.
3. High-Dollar Products and Procedural Costs
While monitoring supply chain metrics is important to effectively control overhead, granular data can be useful for oversight of high-cost materials. An example of this would be tracking supply cost per case of goods that are used for a specific manufacturing order for a certain customer. Or semiconductors that require tracking by expiration dates and lot numbers.
Automated data collection is especially useful in this respect. The visibility gained by instant material data can inform continuous improvement strategies, as well as financial and supply chain integration. Mobile barcoding and data collection can ensure big ticket items, like equipment and expensive parts, can be found anywhere, anytime.
But this only works if technology is integrated you’re your everyday business processes. Forty-seven percent of Digital Inventory Report respondents cite the need to integrate multiple systems as a key issue. By implementing real-time asset tracking software that easily integrates with business-critical systems like an ERP, supply chain leaders can boost production and manufacturing efficiency.
What Mobile Technologies Best Support Your Operation?
SIMILAR »4. Industry Standards
Maintaining industry standards throughout supply chain operations transcends basic regulatory compliance—it protects against inefficiencies, financial vulnerabilities, and reputational damage. Organizations in highly regulated sectors such as pharmaceuticals, food production, and aerospace must track unique product identifiers to ensure product safety, traceability, and compliance with industry mandates.
This tracking extends beyond basic SKUs to encompass lot numbers, serial numbers, batch codes, and expiration dates. The ability to trace components, ingredients, or finished goods throughout every supply chain stage is essential for meeting regulatory requirements and preventing costly operational disruptions.
Without automated systems, maintaining compliance becomes labor-intensive and error-prone. Manual tracking methods prove impractical, especially in large-scale operations requiring real-time visibility. Purpose-built traceability software automates the entire process, ensuring proper logging, tracking, and accessibility for audit or recall scenarios.
The benefits of automated compliance tracking include:
- Stronger recall preparedness – In the event of a product issue, businesses can swiftly identify affected batches, reducing downtime and minimizing financial loss.
- More accurate usage tracking – With precise data, companies can optimize material usage, reduce waste, and make better purchasing decisions.
- Improved spend analysis – Tracking production and inventory movement at a granular level allows for a clearer understanding of costs and opportunities for savings.
- Streamlined compliance processes – Automated data collection reduces the administrative burden of regulatory reporting, ensuring that documentation is always current.
The value of compliance tracking depends entirely on data accuracy and integrity. Inconsistent or incomplete information leads to errors, compliance violations, and supply chain bottlenecks. Organizations must implement standardized data capture methods, integrate them across all platforms, and continuously monitor for accuracy.
As supply chain regulations evolve and become more stringent, automated traceability solutions are no longer optional. These systems are essential for maintaining operational efficiency, ensuring compliance, and protecting business continuity.
What Does Supply Chain Innovation Look Like in Action?
ALSO READ »5. Human Supply Chains
While digital transformation dominates supply chain discussions, the human element remains crucial to operational success. Effective supply chains balance technological advancement with workforce optimization to achieve peak performance. However, persistent staffing shortages and workforce challenges increasingly threaten operational stability. Over 70% of companies surveyed in the RFgen Digital Inventory Report cite staffing as a primary operational concern.
Escalating labor demands, high turnover rates, and growing operational complexity continue to strain supply chain teams. Forward-thinking organizations address these challenges through human-centric technologies, including mobile workforce management platforms, digital task automation, and real-time communication tools. These solutions reduce manual workloads, minimize errors, and enable employees to focus on strategic activities rather than repetitive processes.
Companies investing in mobile supply chain solutions experience measurable improvements across multiple dimensions:
- Enhanced workforce productivity reduces time spent on manual data entry, inventory counts, and shipment tracking, allowing employees to engage in more strategic initiatives.
- Reduced operational costs come from automating routine processes to optimize staffing levels without sacrificing operational efficiency.
- Improved accuracy and throughput result from digital task management tools that reduce errors while enhancing order fulfillment and inventory tracking precision.
- Decreased burnout and turnover occur when mobile automation lightens workloads, alleviating employee stress and reducing absenteeism and staff churn.
Beyond internal efficiency gains, workforce optimization directly enhances customer experience. Employees with real-time inventory data, automated workflows, and digital reporting fulfill orders faster, make fewer errors, and respond more effectively to demand fluctuations.
The result is a noticeable improvement in service quality: fewer shipment errors reduce costly returns and order disputes; shorter lead times ensure products arrive when and where needed; and greater operational flexibility allows businesses to scale without proportional workforce expansion.
One RFgen customer successfully leveraged mobile supply chain software to reconfigure work assignments, enabling their team to process higher order volumes without additional hiring. This approach improved efficiency while maintaining service levels despite significant demand variability.
As labor challenges persist, organizations investing in human-centric automation gain substantial competitive advantages. Those effectively balancing technology implementation, process automation, and workforce optimization achieve higher efficiency, enhanced customer satisfaction, and long-term operational resilience.
By extending ERP functionality through mobility solutions, companies build more agile, resilient, and productive workforces equipped to handle the evolving demands of modern supply chains.
Effective Supply Chain Solutions for Your Business
The current economic landscape and evolving market conditions continue to transform operational requirements across industries. While implementing automated mobile solutions may not completely shield organizations from disruption, the resulting supply chain visibility significantly enhances preparedness in an uncertain business environment.
Maintaining efficient supply chains is crucial for resource optimization and cost control, ultimately maximizing profitability. Well-executed supply chain optimization strategies enhance operational efficiencies and enable organizations to accomplish more with fewer resources. The outcome is a streamlined, more productive approach to establishing clear competitive differentiation.
Beyond immediate efficiency gains, optimized supply chains strengthen long-term adaptability. Organizations investing in real-time data capabilities, automation technologies, and workforce optimization identify emerging risks earlier, adjust inventory strategies proactively, and respond to market fluctuations more precisely. Making faster, more informed decisions provides a competitive advantage and fundamentally strengthens an organization’s capacity to adapt, scale, and thrive amid persistent market unpredictability.
Frequently Asked Questions (FAQs)
1. What makes a supply chain effective?
An effective supply chain seamlessly integrates technology, data-driven decision-making, and automation to optimize inventory management, streamline logistics, and improve overall efficiency. Businesses that achieve supply chain effectiveness leverage real-time visibility, automated workflows, and a well-managed workforce to reduce costs and enhance productivity.
2. What are the most important supply chain factors for optimization?
Several key supply chain factors contribute to optimization. One of the most important is tracking supply chain metrics, which helps businesses assess performance indicators such as order accuracy, stock turnover, and demand forecasting. Another critical factor is inventory automation, where technologies like barcoding, RFID, and mobile tracking improve real-time stock updates. Cost management is also essential, ensuring high-dollar products and procedural costs are closely monitored to maintain profitability. Compliance with tracking product identifiers, such as serial numbers and SKUs, in highly regulated industries is vital in avoiding costly errors. Finally, workforce efficiency remains a major factor, as businesses that integrate human-centric automation can alleviate labor shortages while increasing productivity.
3. How does automation improve supply chain effectiveness?
Automation is a game-changer for supply chains, allowing companies to significantly reduce manual errors, improve data accuracy, and enhance efficiency. Businesses that implement automated inventory tracking systems see improvements in order fulfillment speed, warehouse accuracy, and overall workflow optimization. With automation, supply chain managers can free up labor for more strategic tasks while ensuring real-time data is always available for decision-making.
4. What role does data analytics play in supply chain optimization?
Data analytics is a crucial component of an effective supply chain because it provides real-time insights into inventory levels, demand fluctuations, and operational performance. By leveraging predictive analytics, companies can anticipate demand shifts, optimize shipping routes, and improve supplier relationships. The ability to track trends and spot inefficiencies before they become costly problems enables businesses to make more informed, strategic decisions.
5. How can companies reduce costs in supply chain management?
Cost reduction in supply chains comes from multiple strategies working together. Companies can lower operational expenses by optimizing warehouse operations through lean inventory practices and automated storage solutions. Demand forecasting is crucial in preventing stockouts or overstocking, ensuring businesses only carry the necessary inventory. Another cost-saving approach is improving supplier negotiations and exploring third-party logistics (3PL) partnerships, which can lead to more efficient shipping and lower transportation costs.
6. What technologies help create an effective supply chain?
Various technologies contribute to an effective supply chain, each improving different aspects of operations. Warehouse Management Systems (WMS) streamline order processing, picking, and packing, ensuring that warehouse operations run smoothly. Inventory Management Systems (IMS) provide real-time stock visibility, helping companies maintain optimal inventory levels and automate replenishment. The Internet of Things (IoT) introduces real-time monitoring, allowing businesses to track temperature-sensitive goods, asset movement, and stock levels. Meanwhile, Artificial Intelligence (AI) enhances decision-making by improving demand forecasting, identifying inefficiencies, and automating repetitive tasks.
7. How does supply chain optimization improve customer satisfaction?
A well-optimized supply chain directly impacts customer satisfaction by ensuring on-time deliveries, accurate order fulfillment, and faster response times. Companies that invest in automation and real-time inventory tracking experience fewer delays and fulfillment errors, leading to a more seamless customer experience. Providing transparency into order statuses and maintaining high availability strengthens customer trust and loyalty.
8. What are common challenges in supply chain optimization?
Businesses often encounter several roadblocks when optimizing their supply chains. One of the biggest challenges is system integration, where companies struggle to merge multiple software solutions across different departments. Data inaccuracies can also hinder optimization efforts, as poor data quality leads to incorrect forecasting and inefficient resource allocation. Supply chain disruptions, such as material shortages and logistics bottlenecks, remain an ongoing challenge, requiring companies to develop contingency plans. Additionally, many businesses face labor shortages, making it difficult to maintain operational efficiency without adopting automation.
9. How do companies ensure compliance in supply chain management?
Regulatory compliance is essential for avoiding costly disruptions, particularly in industries that require strict product tracking. Companies ensure compliance by maintaining visibility into their supply chain through automated traceability systems. This includes tracking unique product identifiers such as SKUs, lot numbers, and serial numbers, which allow businesses to trace products throughout their lifecycle. By implementing compliance-driven supply chain software, companies can streamline audits, improve recall preparedness, and safeguard against regulatory violations.
10. Why is workforce optimization important for an effective supply chain?
An effective supply chain isn’t just about technology—it also depends on the workforce’s efficiency. Well-managed teams can process orders faster, improve picking accuracy, and make better data-driven decisions. However, many industries are experiencing labor shortages, so companies are turning to mobile workforce solutions and automation to enhance efficiency. By integrating mobile scanning tools, automated picking systems, and digital workforce management platforms, businesses can ensure that employees remain productive while reducing the overall workload.