Maximizing Supply Chain Strategy: A 10-Step Guide
- Supply Chain
Strategy is a critical aspect of supply chain management. Its execution directly impacts cost, quality, and the delivery of goods and services. By managing processes like planning, sourcing, production, and delivery, companies can reduce costs, safeguard against undue risk, and pivot quickly when faced with the unexpected.
But when your supply chain isn’t meeting the company’s goals, what do you do? It’s time to step back and re-evaluate.
Creating a new supply chain strategy can be complicated, if not daunting. Don’t worry. Below, this guide will outline 10 proven steps any business can take to make significant improvements to its supply chain strategy:
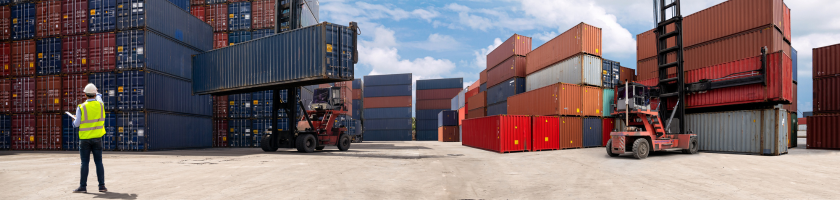
Step 1: Define your supply chain objectives
Before diving into making your strategy, take a deep breath and consider your objectives. A strategy is bound to fail if you can’t define success.
Defining your supply chain objectives sets the foundation for subsequent steps, helping you to understand requirements for alignment, resources, and outcomes. Concrete goals also allow you to prioritize initiatives by effort and impact. This also ensures your objectives align with emerging supply chain trends like sustainability, efficiency, and risk management.
Here are some common supply chain objectives to consider:
- Cost reduction: Minimizing spend associated with acquiring and delivering goods and services to customers.
- Improved efficiency: Streamlining processes and reducing waste to improve speed and accuracy of supply chain optimization.
- Increased customer satisfaction: Delivering products and services to customers in a timely, reliable, and compliant manner—or exceeding their expectations.
- Enhanced sustainability: Incorporating environmental, social, and economic considerations into supply chain optimization.
- Risk management: Identifying and mitigating risks in the continuous flow of goods and services.
- Improved supplier relations: Building and maintaining strong, collaborative relationships with suppliers, vendors, and technology partners.
Ideally, you will want to improve in all these areas. Realistically, you may have to prioritize due to logistical or budget limitations.
Consider the following tips to help you prioritize your objectives:
- Align supply chain objectives with business goals to support the company’s vision or mission.
- Consider the needs and expectations of customers and other supply chain partners to prevent any gaps.
- Take into account the trends and challenges facing your industry.
- Conduct a SWOT analysis of your supply chain to identify strengths, weaknesses, opportunities, and threats.
- Engage key stakeholders to gather their perspectives and insights, including suppliers, employees, and customers.
5 Factors to Consider for Effective Supply Chain Optimization
READ MORE »Step 2: Conduct a supply chain assessment
With your objectives in mind, the next step is to conduct a thorough analysis of your supply chain and supply chain strategy. You can’t make adjustments without first knowing what needs to be adjusted.
Your assessment will enable you to baseline current performance, identify areas for improvement and potential risk, and highlight weaknesses that need extra help.
To get the best outcome, don’t work in a silo. Instead, develop a planning team consisting of experienced supply chain experts.
When beginning your analysis, be sure to:
- Map out your present supply chain. Create a visual representation of the flow of goods and services from the point of origin to the point of consumption.
- Identify bottlenecks and roadblocks. Look for areas where processes are slow, prone to errors, or not keeping up with customer expectations.
- Understand how strategy and business plans connect. Take the time to assess the company’s current supply chain strategy and supply chain management plan, which may differ.
- Analyze data. Gather and analyze supply chain data to help you recognize trends and patterns that indicate both strengths and areas for improvement.
Learn the 3 hidden costs of manual warehouse processes
WATCH NOW »Consider bringing in outside help
But conducting this type of assessment is very difficult to do internally. It can be hard to step away and observe current strategies with an objective eye. This is where hiring an outside consultant can help.
A consulting firm can help you better understand your supply chain’s strengths and deficiencies and assist in setting goals, which will be an important part of your supply chain management strategy. They can also assist in formalizing a comprehensive report for the C-suite.
If you’re considering a third-party assessment, here are a few things to expect:
- You may be asked to assist in the in-depth discovery process.
- They may tell you your processes are out of date.
- They will likely uncover old technologies in need of upgrades.
- They will recommend solutions, but it’s up to you whether you implement them or not.
The consultant may review individual facilities and suggest ways to reduce operational overhead and smooth out supply chain potholes. As a part of this process, many companies discover their warehouses still rely on manual or obsolete data processing systems to record and exchange data. Not only does this generate incorrect information, this “dirty” data then leads to sluggish, inefficient operations. Budget for new data collection solutions may be needed to solve the problem.
In any case, to get the most value out of the evaluation process, work closely with the consulting firm to identify objectives and carry out possible avenues to achieve them.
WATCH BELOW: Life Extension revitalizes its supply chain with mobile barcoding –
Benefits of a supply chain assessment
Even if you think you understand your supply chain, it’s still worth conducting an assessment to gain insight into the reality of current operations. A structured assessment can reveal inefficiencies that could be resolved through a lean supply chain approach, ensuring optimized workflows and reduced costs.
The benefits of performing a supply chain assessment may include:
- Improved understanding of your supply chain, including how goods and services are acquired, moved, and delivered—and how data is collected along the way.
- Identification of problem areas, namely bottlenecks and inefficiencies resulting from outdated processes and technologies.
- Increased efficiency from solving problem areas and breaking down hidden roadblocks.
- Enhanced customer satisfaction through greater speed, accuracy, and reliability.
- Improved risk management to mitigate potential disruptions before they halt the flow the goods and services.
Solving Supply Chain Problems with Mobile Software
ALSO READ »Step 3: Identify key stakeholders
Before formalizing your supply chain strategy in written form, identify the key stakeholders that can help inform the plan, and who in the organization will be impacted by its implementation.
A “key stakeholder” is any individual, group, or vendor involved in the company’s supply chain. Not everyone in the supply chain will be crucial to this process, so narrow stakeholders down to only the most important personnel that need to be involved.
Key stakeholders may include:
- Suppliers
- Manufacturers
- Distributors
- Retailers
- Customers
- Logistics service providers
- Government agencies
- Financial institutions
Work Closely with Your Team and Third-Party Vendors
One of the reasons supply chains falter is because of disruptions in the flow of communication or information exchange between strategy planners and stakeholders.
To build a well-flushed-out supply chain management strategy, communication is essential. Internal and external teams must work together as a cohesive unit. Without continuous alignment, even the best plan will fall apart before it can be carried out.
When communicating with stakeholders, consistent communication and transparency are vital to success. Companies that succeed in these two areas have a much greater chance of creating a supply chain strategy that supports their business objectives.
How Blue Bell ice cream manufacturer overcame supply chain challenges
WATCH VIDEO »Step 4: Evaluate your current technology and infrastructure
Technology and infrastructure play an important role in supply chain optimization. Infrastructure is the highway that allows the supply chain to keep moving. Meanwhile, technology makes up the tools that enable your supply chain to harvest data, automate processes, increase efficiency, and track performance.
But having technology and infrastructure already in place doesn’t mean either is necessarily sufficient for the company’s needs.
Fast-moving supply chains demand continuous investment and improvement to remain competitive. Transportation networks, distribution centers, and production plants require constant attention for the efficient movement of goods. Technology ages out and so must be replaced, improved, or developed to keep up with the needs of the business.
When evaluating technology and infrastructure, consider the following components:
- Transportation and logistics infrastructure: Assess transportation and logistics infrastructure thoroughly, including vehicle fleets, warehouses, and manufacturing plants.
- Software systems: Evaluate supply chain software regularly, including enterprise resource planning (ERP) systems, mobile barcoding and inventory systems (IMS), warehouse management systems (WMS), and transportation management systems (TMS).
- Data management and analytics tools: Don’t overlook data management and analytics tools, including storage, business intelligence, big data, machine learning, and data collection practices.
Evaluate these areas of the business with end goals in mind. Upgrades shouldn’t take place for their own sake, but to improve efficiency, transparency, decision-making, and overhead spend.
Your guide to 100% paperless inventory control
READ MORE »Step 5: Develop a risk management plan
As complex, dynamic systems that can be geographically far-reaching, supply chains are subject to many types of risks. Therefore, managing risk is always top-of-mind. Failing to account for risk often results in unnecessary costs and loss of sales.
Even if your organization has a risk management plan in place, now is the time to re-evaluate its effectiveness to minimize the impact of disruptions. Otherwise, sustainable long-term success becomes impossible.
These are some of the most common supply chain risks to consider:
- Disruptions from plant shutdowns, labor strikes, production failures, supplier bankruptcies, unpredictable supply and demand, ransomware, and geopolitical uncertainty.
- Delays due to transportation problems, wait times in customs, insufficient raw materials, and worker shortages.
- Natural disasters such as hurricanes, earthquakes, fires, and flooding that can cause damage to equipment and infrastructure.
To manage these risks, your plan should:
- Identify potential risks, including both internal and external factors.
- Account for contingency plans, such as by including backup suppliers or alternative transportation methods.
- Be subject to regular monitoring and updating. Risks change over time, so what worked previously may no longer be valid at some point in the future.
How to Mitigate Supply Chain Disruptions with Mobile Barcoding
DIG DEEPER »Step 6: Optimize your supply chain network
Improving established supply chain networks should be an ongoing process. There are always new opportunities to optimize the delicate equation of cost, service, level, and risk.
Ideally, refinements will help with cost savings and customer service through gains in efficiency and responsiveness. Once again, technology often plays a vital role.
When considering new optimization initiatives, pay close attention to these three principal areas:
- Demand Forecasting: Analyzing data to predict future demand provides valuable insights for production, inventory, and staffing. The right technology will be needed to collect data quickly and accurately to achieve “true” visibility.
- Inventory Management: Often overlooked as a bottleneck, technology can help eliminate manual work, data entry, and superfluous steps in the material handling process.
- Transportation Planning: In addition to adjusting modes of transportation, seek to leverage software and GPS to gain efficiency in routing and delivery scheduling.
For technology, software solutions provide a cost-effective means of optimization. Requiring minimal or no infrastructure, mobile inventory solutions and warehouse automation software drive improvements and bridge operational gaps in all principal areas of the supply chain.
Lessons learned from the Coca-Cola supply chain
YOU MAY ALSO LIKE »Step 7: Improve supplier relationships
The supply chain only functions if every member of the “chain” has a good working relationship. Therefore, improving supplier relationships to build reliability and trust should be a continuous goal. Without either, companies will struggle to meet demands and make a profit.
Suppliers can impact your supply chain in many ways, including:
- Quality of goods
- Delivery
- Cost
- Innovation
- Competitiveness
When revising your strategy, consider the many ways your company can strengthen relationships with suppliers and manage those relationships more effectively.
Effective supplier relationships may require:
- Clear Communication: Establish open and transparent communication channels with suppliers to ensure expectations and requirements are clearly defined and understood by both parties.
- Contract Management: Develop clear and concise contracts that outline the terms and conditions of the relationship, including delivery schedules, quality standards, and pricing. Periodically update supplier contracts and agreements to ensure they reflect current business needs.
- Performance Management: Regularly assess the performance of suppliers and provide feedback to help them improve. Use metrics to measure performance and track progress over time.
- Joint Problem Solving: Collaborate with suppliers to identify and resolve any issues that may arise, such as delivery delays or quality concerns.
- Mutual Benefits: Foster mutually beneficial relationships with suppliers by sharing information, knowledge, and resources. This can lead to increased innovation and collaboration, as well as a stronger relationship overall.
Step 8: Develop a sustainability plan
Sustainability helps supply chains ensure the long-term viability of operations. The environmental, social, and economic impact of each component of the total network should be considered.
Ultimately, the goal is to meet the evolving needs and expectations of customers, stakeholders, and society while reducing environmental footprint.
Making an organizational commitment to sustainability comes with numerous benefits, such as:
- Cost savings from reduced waste and efficiency gains
- Improved reputation and brand image
- Enhanced customer satisfaction and loyalty
- Greater compliance with environmental and industry regulations
The risk of not committing to sustainability cannot be understated. Once the company’s brand becomes associated with practices that harm the planet and human health, that reputation can be very difficult to shed.
Why people are the best investment you can make in a sustainable supply chain
RELATED »Step 9: Implement the plan
Your supply chain management strategy should include a serious discussion about how your team will implement the plan into the company’s operations. This process can be difficult to accomplish, especially if employees are set in their ways. But it shouldn’t be cast aside.
With the plan drafted, now it’s time to:
- Gather Employee Feedback: Poll employees about what bothers them most about the current supply chain management strategy, and what they’d like to see improved. Then try to incorporate their feedback into your plan.
- Create an Eye-Pleasing Report: A well-designed and organized report will go a long way in helping you present your ideas in the most impactful way possible.
- Present to Upper Management: You need to know your audience, and make sure you’ve addressed all their concerns in your report. Even if you don’t have a solution for all the issues, showing that you’ve extensively researched the problem will demonstrate to leadership that your team is taking the initiative and can be trusted. This is crucial to convincing the C-suite to support and fund the new strategy.
- Roll out the Plan: Your strategy should include how you plan to implement the strategy into your employees’ day-to-day jobs. It should also address the role your team members will play. This may include educating managers and departments, for example, so they can then pass the knowledge down to their employees.
- Evaluate the Results: No plan is complete without a section that addresses how success will be measured. Companies need to evaluate the strategy by collecting both quantitative and qualitative data over the course of days, weeks, months, and even years.
As always, communication will play a major role during this phase of the strategy. Maintaining alignment among all stakeholders is pivotal for success.
Step 10: Monitor and measure performance
As an extension of Step 5 above, once the plan is implemented, tracking its performance will assist with making informed decisions about current adjustments and future improvements.
Regular monitoring and measuring can help organizations to:
- Identify areas for improvement
- Ensure compliance with goals and objectives
- Enhance visibility and control
- Manage risk and minimize disruptions
- Improve decision-making
And, when the time comes, performance may indicate when it’s time to create a new supply chain strategy altogether.
3 Steps to Run a Successful Warehouse
SIMILAR »A Supply Chain Built on Continuous Improvement
Forming a new supply chain strategy isn’t easy—and implementing it can be even more challenging. Still, an effective strategy forms the bedrock for a vibrant supply chain.
By investing in and continuously improving supply chain processes, businesses can gain a competitive advantage and succeed in today’s fast-paced world. Technology remains a proven channel for achieving immediate, salient efficiency gains.
By following the steps outlined in this guide, you can take the first steps in formulating a new strategy that will help your organization overcome operational challenges and deliver the best possible products and services to your customers, now and in the future.