Identifying Warehouse Management Best Practices
- Inventory/Warehouse
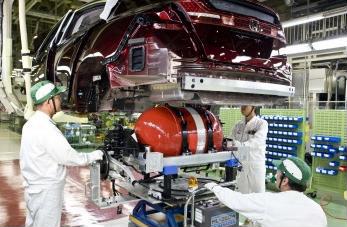
As manufacturers incorporate new components into their existing supply chain structures to meet growing demand, warehouse managers may find that maintaining oversight across their operations has become significantly more difficult. After a substantial uptick in production, manufacturers will have to contend with more inventory to track, employees, to manage, and shipments to monitor. Should manufacturers falter in these duties, the result could be operational inefficiencies and bottlenecks, leading to costly service disruptions. To ensure that manufacturing operations continue uninhibited, business leaders should adhere to warehouse management best practices.
In addition to various structural design choices, Cirrus Logistics suggested that manufacturers consider how a warehouse management solution will be deployed when constructing or altering their facilities to meet future expansion needs. One of the primary issues facing manufacturing executives is how RF devices such as a mobile barcode reader will be used in the warehouse environment, as administrators must ensure the software is compatible with existing systems. However, with a comprehensive data collection software solution such as RFgen, these solutions can be seamlessly integrated with critical legacy software such as ERP applications.
Reducing Inventory Inefficiencies
Warehouse inventory management systems are critical to tracking the various stages of the manufacturing process. From production to delivery, officials need to be able to monitor inventory as it makes its way through the supply chain. This is especially relevant during periods of growth, as a sudden influx of inventory may overwhelm employees on the floor, leading to costly errors. Without a robust inventory control system, managers may have difficulties locating materials or finished products, causing them to dedicate more manpower and resources to this process. Officials with Land Rover dealt with this issue on a regular basis, according to Zebra Technologies. When vehicles rolled off the assembly line, they were subject to a number of finalization processes, including testing, setting configurations and addressing any existing errors. Managers had a great deal of difficulty identifying where individual items were located along the supply chain, resulting in a high degree of uncertainty and risk.
To address these concerns, the automaker implemented an RFID-based system to better track inventory movement and streamline production, testing and shipping operations. After the inventory management software was deployed, company leaders reported a higher rate of production as vehicles progressed more seamlessly through the supply chain, a reduction of inventory and carrying costs, and the ability to expedite a shipping order when needed. A sophisticated warehouse automation system can help managers ensure that critical components of the supply chain are performing as needed and eliminate harmful bottlenecks.