Boost Efficiency with Automated Inventory for Faster Fulfillment
- Digital Transformation
- Inventory/Warehouse
Today’s supply chain is all about efficiency and customer satisfaction. The speed of your order management processes is crucial to both. If your order management procedures are subpar—or you’re still using manual processes—then improving order fulfillment speed is a matter of survival.
How quickly and accurately an organization can process sales orders and production orders directly impacts downstream operations. Hindrances to the continuous flow of goods hurt the bottom line. Ultimately, customer service declines.
That’s why efficient order management processing is essential for today’s distribution and warehouse operations. And automated inventory management may hold the key.
Why Bother with Automation?
Automation is the crux of “worker smarter, not harder.” Intelligent software solutions can automate inventory management processes like order picking and fulfillment to remove human error and manual tasks.
Essentially, for a one-time investment in automated inventory management software, your operation repays those costs and expands profit margins for years to come.
Less time manually keying data into workstations or sifting through spreadsheets means more time to take on higher-value activities. A more optimal distribution of work allows your people to focus on what matters most—serving your customers.
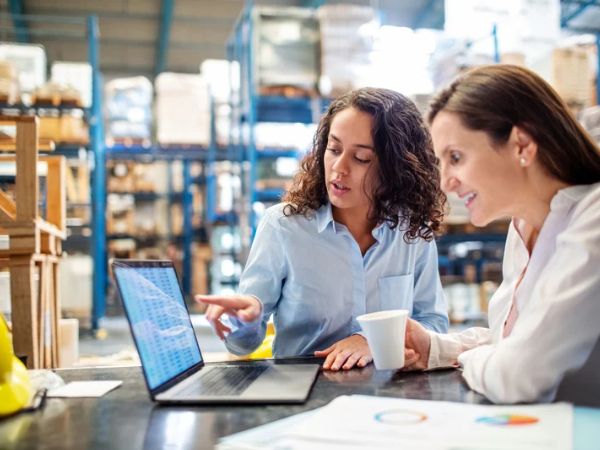
The Insider’s Guide to Choosing the Best Inventory Management Software for Your Business
READ NOW »The ABCs of Automated Inventory Management
Automated inventory control covers a lot of operational areas, not just order fulfillment. Since supply chain workflows operate end-to-end, inventory automation can affect all of those processes. Bringing automation into the warehouse typically brings the following benefits:
Real-time Inventory Updates: All material movements transact in your ERP system as they occur on the floor. No more blind spots, no more guessing games. You’ll always know exactly what’s in stock, where time to find it, and when it’s time to reorder.
Automation of Processes: This is a big factor, accelerating processes like receipts, put-away, picking, packing, and shipping. Less manual labor speeds up the entire order fulfillment process.
Reduced Errors: With automated data capture and built-in data validations, the chances of making an inventory management mistake becomes negligible. Fewer errors mean fewer delays in order fulfillment.
Improved Order Accuracy: Mobile solutions can help improve order accuracy by providing workers with exact item information and location in detail, ensuring the correct item is picked.
Enhanced Employee Productivity: With handheld devices, employees can access critical information on-demand and transact stock from anywhere in the warehouse. This saves time that might otherwise be spent going back and forth between a stationary computer and the warehouse floor.
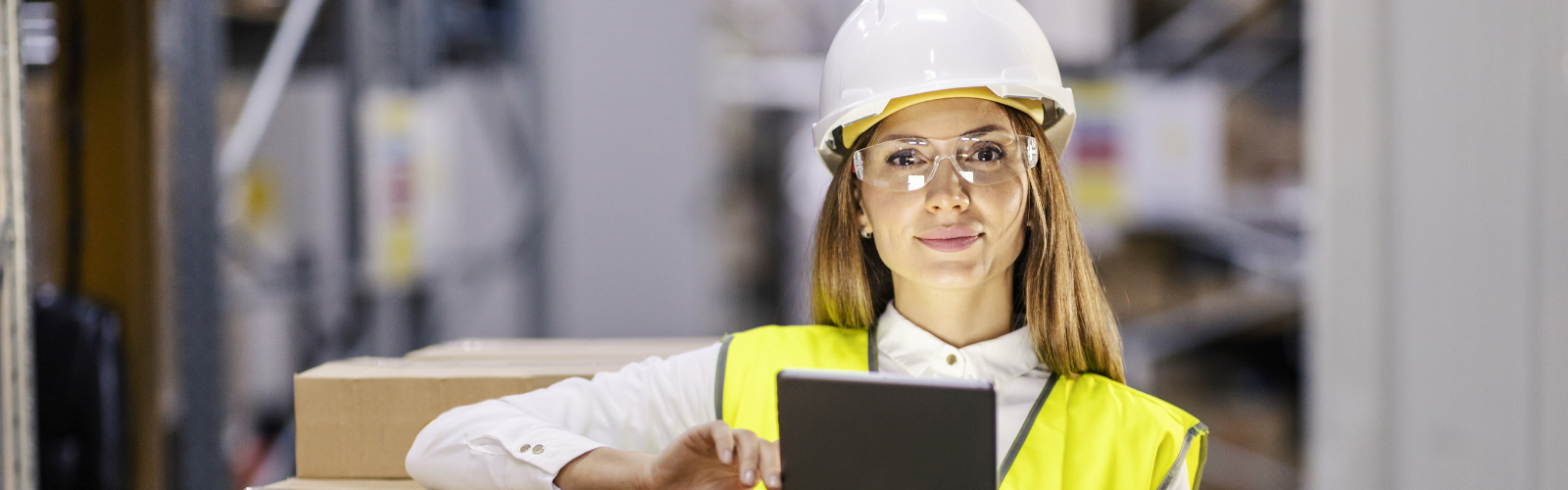
Mastering Order Management in Supply Chain Management: A Comprehensive Guide
LEARN MORE »The Impact of Automation on Order Fulfillment
By automating order fulfillment workflows, organizations experience:
Reduced Order Fulfillment Time
By streamlining the entire order fulfillment process, items for each order can be located, picked, packed, and shipped—with live updates at every step. For manufacturing, consumption of raw materials in real time ensures availability for ongoing and future projects.
Increased Throughput
Faster order fulfillment means more orders can be processed in the same amount of time, increasing the overall throughput of the warehouse. The ability to scale SKUs and orders is crucial to expansion and growth. Meanwhile, spending less time on each order—not to mention holding costs—helps reduce labor and operational expenses.
Improved Accuracy
When it comes to technology, automating data collection with mobile barcoding is unbeatable. Scanning barcodes with a mobile device captures information perfectly, driving inventory accuracy above 99.9%. Fewer mistakes cut down on costly mispicks, misshipments, and returns.
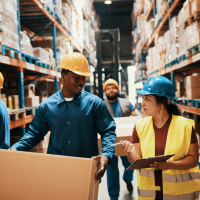
The Insider’s Playbook to Outsmarting Misships
READ NOW »Enhanced Customer Experience
When orders are processed faster and more accurately, customers are happier. If a customer needs a last-minute adjustment, greater agility allows you to meet that need and go the extra mile. Happy customers translate to repeat business and assured revenue.
Competitive Advantage
Faster fulfillment speeds can provide a competitive edge in the marketplace, especially in industries where fast delivery is a key differentiator. Better efficiency, greater visibility, the ability to pivot quickly, and cost reduction easily put you ahead of competitors lagging behind in automation.
Factors to Consider when Implementing Automated Inventory Management
In most cases, a need to improve order fulfillment speed is a symptom that other areas of your warehouse could use optimization as well. Luckily, automation software can enhance any aspect of inventory management suffering from performance issues.
When evaluating what type of automated inventory management solution you should choose, first consider these three major points:
1. Integration with Existing Systems
Will your new inventory software play nicely with your existing technical environment? What about your ERP system? Does the potential solution include certification, validation, case studies, or a history of successful implementations?
2. Cost vs. Benefit
Investing in automation can be a significant expense—at first, anyway. But the long-term benefits often outweigh the initial costs. This is called return on investment, or ROI. Be careful when evaluating ROI in your cost-benefit analysis. An expensive, overly complex solution like a WMS may end up costing your warehouse more than a simpler, more cost-effect solution like enterprise mobility.
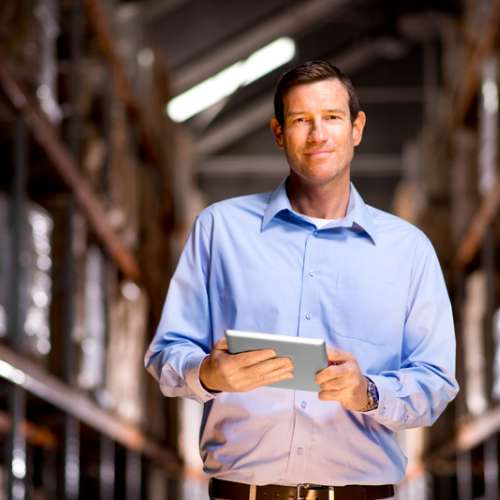
Get the guide: How to find and calculate ROI for warehouse automation software.
DOWNLOAD NOW »3. Training and Support
Even if the software you consider is functionally identical, how the providers support you on your new technology journey may differ drastically. Look for a software provider with a dedicated team committed to your success—not one that disappears after you’ve made the purchase. A long-term strategic partner can save you time and money far beyond your software investment.
But don’t forget about training! Putting your personnel through proper training on the new solution is the best way to get more out of your new acquisition.
FAQs
Automated inventory management is a system that uses technology to maintain and control inventory levels, thus improving order fulfillment speeds. This system tracks inventory in real-time, forecasts demand, and sets reorder points, making the entire process more efficient and less prone to error. Inventory management automation takes many forms, from mobile inventory software to WMS, to other ERP-based solutions.
How does automated inventory management improve order fulfillment speeds?
By automating tasks such as inventory tracking, receipts, transfers, picking, and order management, organizations can process orders more quickly and accurately. This results in faster delivery times, fewer errors, and happier customers.
What factors should I consider when implementing automated inventory management?
Key factors include the system’s compatibility with your existing software, the cost versus benefit analysis, and the quality of support and training from the provider.
How does automated inventory management enhance the customer experience?
With faster and more accurate order fulfillment, customers receive their orders on time and with fewer mistakes. This leads to higher customer satisfaction and repeat business—not to mention the opportunity for growth.
Is automated inventory management suitable for my business?
Whether you’re a small business or a large enterprise, if you deal with inventory, automated inventory management can streamline your processes, save time, and reduce errors. For medium to large enterprise organizations using ERP software, mobile inventory solutions can extend automation to point-of-work for employees in the warehouse or on the shop floor.
Does automated inventory management require a significant investment?
While there may be upfront costs, the long-term benefits significantly outweigh the initial investment. Improved accuracy, efficiency, productivity, and quality offer high returns on investment (ROI) and a quick path to increased profit margins.
How to Improve Order Fulfillment Speeds with Automated Inventory Management
As we’ve seen, supply chain operations rely on fast, effective order fulfillment speeds to remain competitive and stay ahead of the curve. It’s not just about working harder but working smarter with strategic inventory software investments. With automation, you can streamline processes, reduce errors, increase throughput, and ultimately create a better experience for your customers. (And if it makes leadership happy along the way, that’s okay, too).
Every day you wait to automate your inventory processes is another day you give the competition already leveraging automation to take the lead. Don’t miss out!