Understanding the Bullwhip Effect: Causes, Examples, and Strategies for Prevention
- Data Collection
- Mobile Inventory Management
- Inventory Management Software

Managing inventory effectively is a constant challenge for businesses. Balancing supply and demand requires careful planning and the ability to adapt to changing market conditions, especially when considering the bullwhip effect in supply chain management. Misunderstandings about the dynamics of inventory fluctuations, like the bullwhip effect, can exacerbate these challenges.
Often, what’s perceived as the bullwhip effect is actually a related but distinct phenomenon: the inventory accelerator. Jason Miller, Professor of Supply Chain Management at Michigan State University, clarifies the difference: “The bullwhip effect is the idea that the variance in orders becomes amplified as you move upstream in the supply chain…from retailer to wholesaler, wholesaler to manufacturer, and so on.” He distinguishes this from the inventory accelerator: “A firm’s level of inventory is positively correlated with its level of demand.” This means that as demand increases, inventory levels typically rise, and conversely, when demand falls, inventory levels decrease. While this seems straightforward, the consequences for businesses can be substantial.
Jason uses the example of machinery wholesaling to demonstrate the inventory accelerator. Referring to the post-2008 period, he notes: “Sales are rising rapidly from 2017 through 2018. During this same period, inventories are also increasing. Manufacturers benefit twofold because replenishment orders exceed sales at the wholesale level.” However, this advantage can quickly reverse when demand declines, impacting manufacturers with both lower sales and excess inventory.
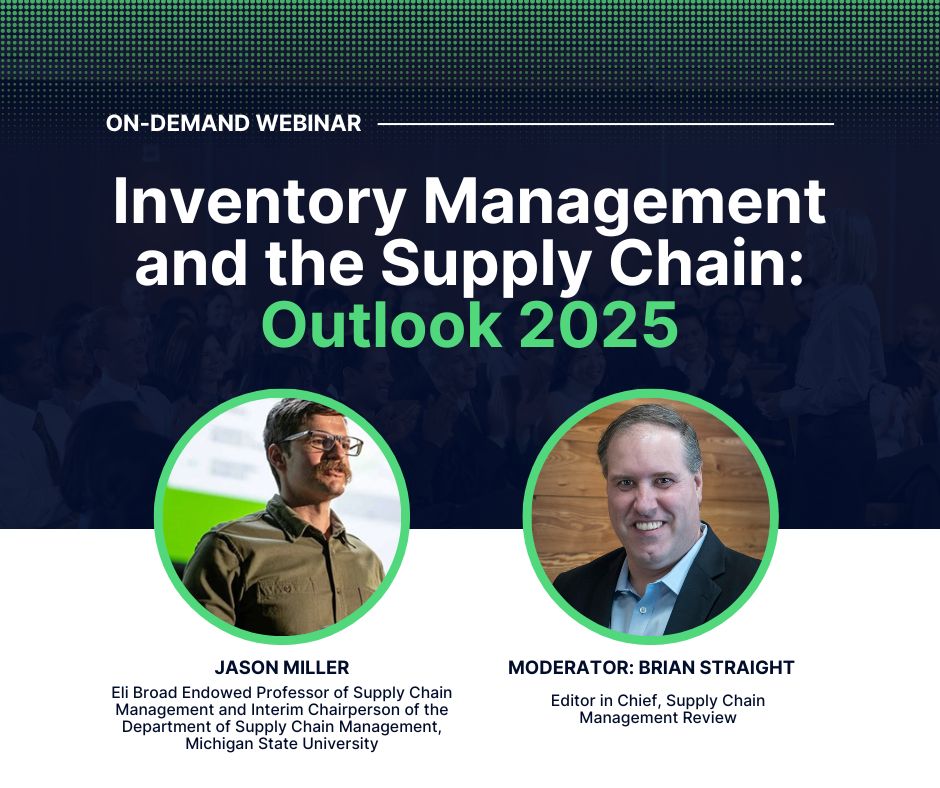
Mastering Inventory in 2025: Key Trends Watch Webinar Now
WATCH WEBINAR »Understanding the difference between the bullwhip effect and the inventory accelerator is essential for effective inventory management. This article will examine the causes of these phenomena, provide real-world examples from different industries, and offer strategies to mitigate their effects. By gaining a clearer understanding of these inventory dynamics, businesses can improve their ability to meet demand and optimize their supply chain.
What is the Bullwhip Effect in the Supply Chain?
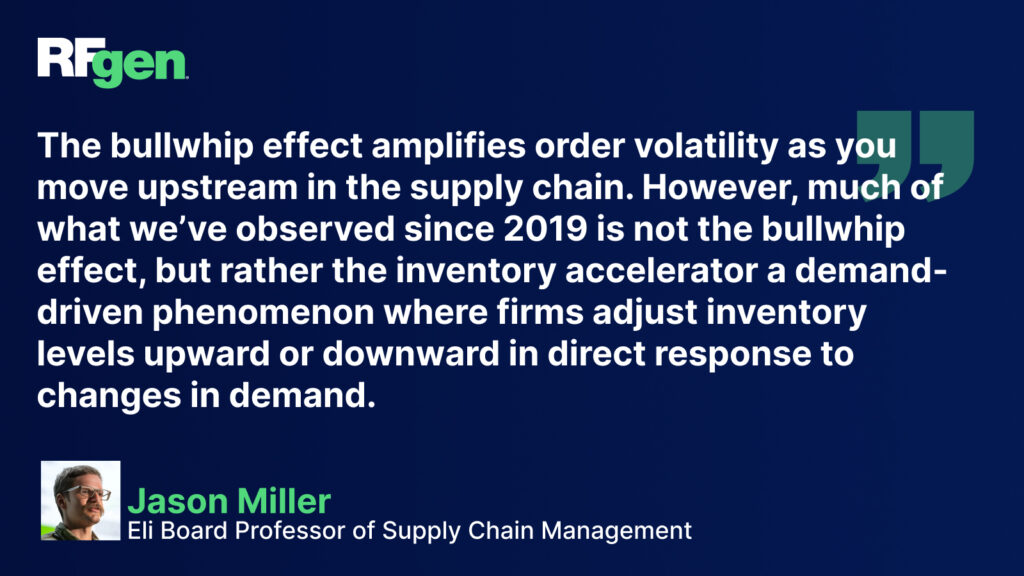
The bullwhip effect, a well-established concept in supply chain management, describes the phenomenon where demand variability increases as you move up the supply chain.
Imagine a retailer experiencing an uptick in customer demand. They might place a larger order to prepare for even higher demand and ensure they have enough stock. The wholesaler, in turn, amplifies the order further when contacting the manufacturer, and so on, up the supply chain. This creates increasingly larger order fluctuations at each stage, resembling the motion of a cracking whip.
In a complex supply chain with multiple intermediaries, these fluctuations can become even more pronounced, complicating demand forecasting and inventory management.
As Jason explains, the variance in orders gets “more amplified as we move upstream in the supply chain.” This amplification can lead to significant inefficiencies, including excess inventory, production bottlenecks, and increased costs. While the bullwhip effect is often associated with rapid shifts in demand, it can also be triggered by inaccurate forecasting, order batching, and price fluctuations.
A key aspect of the bullwhip effect is that it occurs even when consumer demand for the end product is relatively stable. Jason highlights this, using the example of diapers: “Think something like diapers…sales tend to be very steady. So you have consumer sales of some products where sales tend to be very steady. And what happens here is in the middle, you have a little bit of a spike.”
This small spike in demand at the retail level can then be magnified as it moves up the supply chain, creating large swings in inventory and production further upstream. This distinction is crucial because it highlights the inherent instability that can arise even in seemingly predictable markets.
Differentiating the bullwhip effect from normal inventory fluctuations is essential. While some level of inventory variation is expected, the bullwhip effect represents a distortion of actual demand, leading to unnecessary costs and complexities within the supply chain. The next section will explore the key factors that contribute to this disruptive phenomenon.
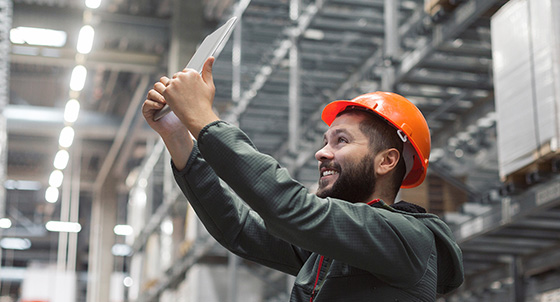
Mastering the Art of Inventory: Unlocking Business Success with Accurate Management and Barcode Technology
READ NOW »Key Causes of the Bullwhip Effect
1. Demand Forecasting Errors: Inaccurate demand forecasting is a primary driver of the bullwhip effect. When retailers overestimate demand, they order more than necessary, leading wholesalers and manufacturers to inflate their projections and production further. Conversely, underestimated demand can lead to stockouts and lost sales. This is compounded when each tier in the supply chain adds a safety stock buffer, magnifying the initial forecasting error
2. Order Batching: Ordering in large batches can create artificial spikes in demand. This is often done to take advantage of economies of scale, such as quantity discounts or reduced shipping costs. However, these large, infrequent orders distort the true demand signal, making it difficult for upstream suppliers to accurately gauge ongoing needs. This can lead to excessive inventory, as suppliers overestimate the ongoing demand. Jason explains that order quantities increase as demand goes up, but “at a less than linear rate.” This non-linearity contributes to the distortion and amplifies the bullwhip effect.
3. Price Fluctuations: Promotional pricing and discounts can also trigger the bullwhip effect. When retailers offer temporary price reductions, customers often stockpile products, creating a surge in demand followed by a sharp drop-off. This artificial demand spike makes it challenging for suppliers to differentiate between true demand increases and temporary fluctuations due to pricing strategies. This can result in increased storage costs as businesses hold onto unsellable inventory.
4. Lack of Communication: Poor communication and information sharing across the supply chain exacerbate the bullwhip effect. When different tiers operate in silos, they lack visibility into the true end-customer demand and rely on potentially distorted information from their immediate trading partners. This lack of transparency leads to reactive and amplified ordering patterns, contributing to the bullwhip’s oscillations.
These four factors often act in concert, creating a complex web of interconnected causes. For example, a demand forecasting error can lead to order batching to compensate for perceived shortages, further distorting upstream suppliers’ demand signal. By understanding these key drivers, businesses can begin to develop strategies to mitigate the causes of the bullwhip effect and create a more stable and efficient supply chain.
RFgen’s inventory management solutions—such as real-time data collection, automated workflows, and barcode scanning—help businesses reduce forecasting errors, improve order accuracy to 99.99%, and reduce carrying costs by 3%-5% by preventing excess inventory buildup.
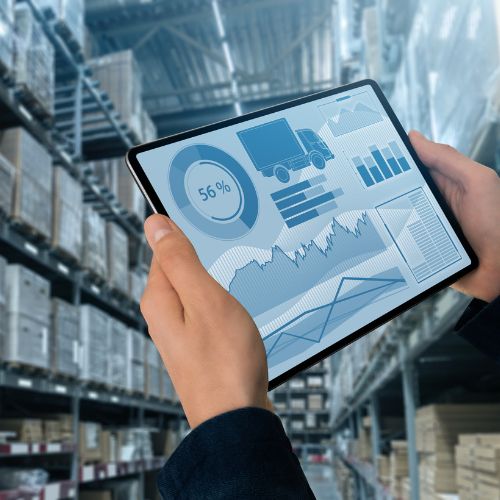
Data Analytics: The Secret Ingredient to Efficient Inventory Management
READ NOW »Real-World Examples of the Bullwhip Effect Leading to Excess Inventory
The bullwhip effect isn’t just a theoretical concept; it plays out in real-world scenarios across various industries, often with significant consequences.
1. The Semiconductor Industry: The global chip shortage of 2020-2021 provides a stark example of the bullwhip effect in action. As noted by Nicolás Rivero in Quartz, a relatively small initial increase in demand for electronics, driven by the pandemic shift to remote work and increased demand for home entertainment, triggered a cascading surge in orders throughout the semiconductor supply chain. “The companies that build those devices then sent a wave of semiconductor orders rippling up the supply chain, which quickly overwhelmed the few chip foundries that manufacture virtually all of the world’s computer chips,” Rivero explains.
This panic buying and hoarding behavior, described by Harvard Business School professor Willy Shih as a common element of the bullwhip effect, exacerbated the shortage far beyond actual consumer needs. Accurate forecasting of future demand could have mitigated some of the panic buying and hoarding behavior.
The resulting impact was felt across numerous industries, from car manufacturers to appliance makers, illustrating how interconnected and vulnerable global supply chains can be to this phenomenon.
2. The Food and Beverage Industry: The COVID-19 pandemic provided a real-time demonstration of the bullwhip effect’s impact on the food and beverage sector. Fluctuating consumer demand, driven by pantry-loading and shifting consumption patterns, created significant challenges for manufacturers. Initial panic buying led to increased demand and strained supply. However, this was followed by decreased demand as consumers worked through stockpiles, creating a “total guessing game” for producers.
This volatility, combined with challenges in communication throughout the supply chain, resulted in overproduction and excess inventory, a costly problem for perishable goods. Using advanced analytics to predict future demand can help manufacturers better align their production with actual market needs. Accurately forecasting and planning become extremely difficult when trends shift dramatically and inconsistently, emphasizing the need for real-time visibility and digital readiness to mitigate the bullwhip effect’s impact.
3. The Craft Beer Boom: Imagine a small craft brewery experiencing a sudden surge in popularity. Local retailers, seeing the increased demand, place larger orders. The brewery, excited by the growth, ramps up production, ordering more ingredients from its suppliers. The suppliers, in turn, increase their production of hops, barley, and other raw materials. However, the brewery’s initial popularity spike may be temporary, driven by a local festival or positive media coverage.
These examples illustrate how the bullwhip effect can impact businesses across diverse sectors. The next section will explore strategies to mitigate this effect and create a more resilient and responsive supply chain.
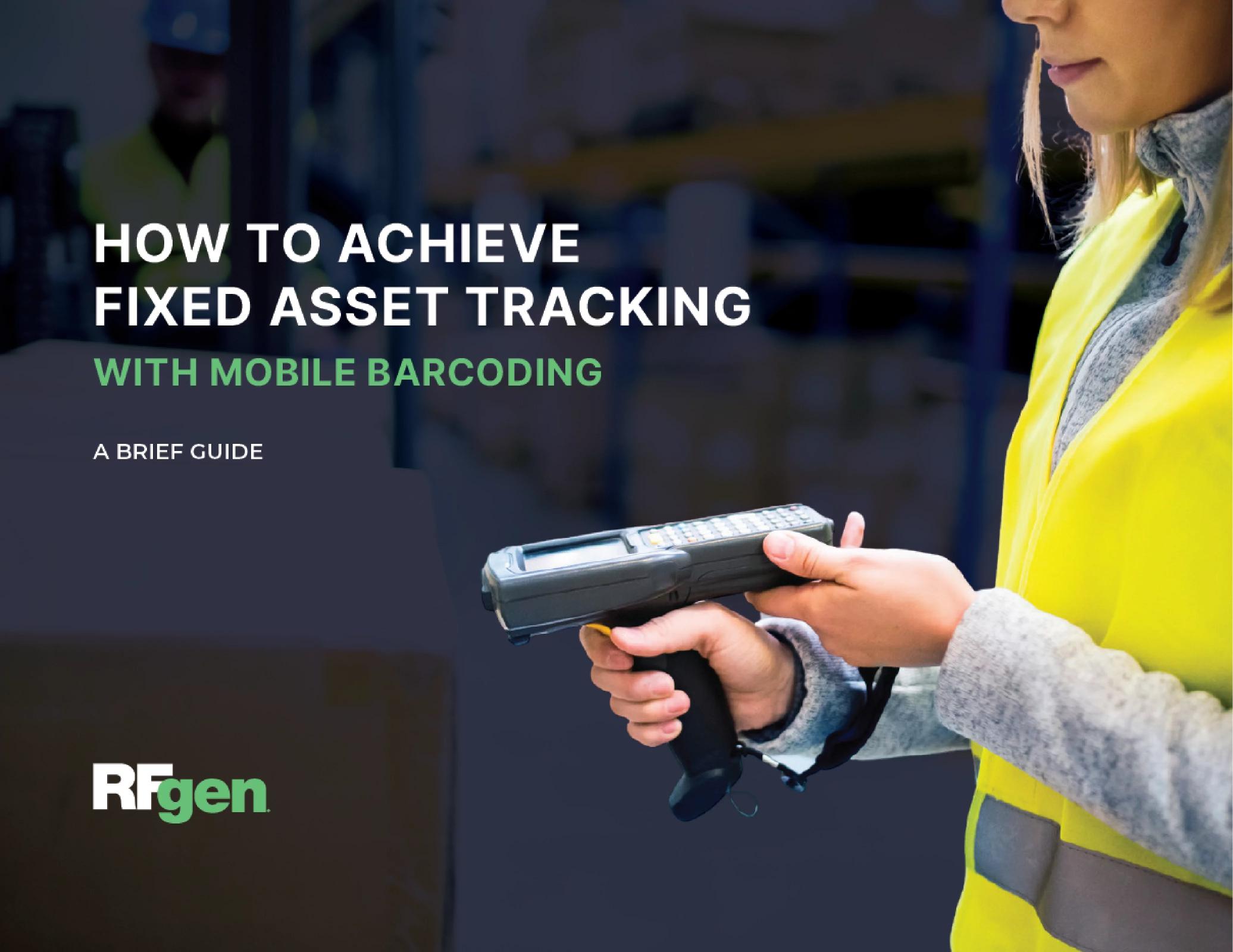
How to Achieve Flawless Fixed Asset Tracking with Mobile Barcoding
DOWNLOAD NOW »Strategies for Preventing the Bullwhip Effect
While the bullwhip effect can pose significant challenges, businesses can implement various strategies to mitigate its impact and create a more stable and responsive supply chain. These strategies focus on improving information sharing, forecasting accuracy, and overall supply chain coordination.
1. Improved Demand Forecasting: Accurate demand forecasting is crucial for preventing the bullwhip effect. Instead of relying solely on historical data, businesses should incorporate real-time data, market intelligence, and collaborative forecasting techniques involving input from multiple stakeholders across the supply chain. Advanced analytics and machine learning algorithms can help identify demand patterns, seasonality, and external factors that influence sales, leading to more accurate predictions. Accurate forecasting can significantly bolster supply chain efficiency by reducing unnecessary fluctuations.
2. Collaboration Across the Supply Chain: Breaking down silos and fostering open communication between different tiers of the supply chain is essential. Sharing information about inventory levels, sales data, and upcoming promotions allows all parties to have a clearer picture of true demand and adjust their production and ordering accordingly. This transparency helps prevent the amplification of demand variability that characterizes the bullwhip effect. Effective communication and timely information sharing among supply chain partners are crucial for minimizing forecasting errors.
3. Lean Inventory Management: Adopting lean inventory principles, such as just-in-time inventory management, can significantly reduce the impact of demand fluctuations. By minimizing inventory levels and focusing on delivering products only when needed, businesses can reduce the risk of excess stock and minimize the impact of demand variability. This requires close coordination with suppliers and efficient logistics processes.
4. Stabilizing Prices: Reducing the frequency and depth of price promotions can help stabilize demand. While promotions can drive short-term sales spikes, they often contribute to the bullwhip effect by creating artificial demand fluctuations. Focusing on consistent pricing strategies provides a more stable demand signal for the entire supply chain.
5. Leveraging Technology: Technology plays a crucial role in mitigating the bullwhip effect. Real-time data capture technologies, such as RFID and barcode scanning, provide accurate visibility into inventory levels and movement throughout the supply chain. Cloud-based platforms facilitate information sharing and collaboration between different stakeholders, enabling faster and more informed decision-making. Implementing supply chain management software can provide real-time visibility and facilitate accurate forecasting. Jason mentions the importance of understanding “simple rules for inventory control” and utilizing tools like the Economic Order Quantity (EOQ) to optimize inventory levels.
Businesses implementing RFgen saw a 20% reduction in excess inventory by eliminating inefficiencies in stock replenishment and aligning purchases with real-time demand signals. Additionally, order accuracy improved by 15% as automated data capture minimized manual entry errors, ensuring that procurement and fulfillment processes were more precise and responsive.
By implementing these strategies, businesses can create a more resilient and responsive supply chain, reducing the disruptive impact of the bullwhip effect and improving overall efficiency and profitability.
Conclusion
The bullwhip effect, characterized by disruptive demand distortions, poses a significant challenge for businesses across various industries. From inaccurate forecasting to lack of communication, the causes of the bullwhip effect can significantly impact efficiency and profitability.
By implementing the strategies discussed — improved forecasting, enhanced collaboration, lean inventory practices, and price stabilization — businesses can create a more resilient and responsive supply chain. Leveraging technology can further enhance visibility and control, enabling proactive management of demand variability.
Ultimately, mitigating the bullwhip effect requires a commitment to continuous improvement and strong partnerships, transforming potential disruptions into opportunities for growth. Assess your supply chain today and explore how these strategies can optimize your operations. Watch the webinar to learn how.
Frequently Asked Questions
What is the bullwhip effect in simple terms?
The bullwhip effect is a supply chain phenomenon where even small fluctuations in customer demand can cause increasingly large swings in inventory and orders as you move upstream from retailer to wholesaler, manufacturer, and supplier. It’s like cracking a whip – a small movement at the handle creates a much larger motion at the tip.
How does the bullwhip effect impact businesses?
The bullwhip effect leads to inefficiencies like excess inventory, production bottlenecks, stockouts, lost sales, increased costs, and difficulty meeting customer demand.
What are the main causes of the bullwhip effect?
Key causes include inaccurate demand forecasting, order batching (ordering in large, infrequent quantities), price fluctuations (promotions leading to artificial demand spikes), and lack of communication between different tiers of the supply chain.
Is the bullwhip effect the same as the inventory accelerator?
No, they are related but distinct. The bullwhip effect refers to the variance in orders increasing upstream, even with stable end-demand. The inventory accelerator refers to the general trend of inventory levels correlating positively with demand levels. Both can contribute to supply chain instability.
How can companies prevent or reduce the bullwhip effect?
Several strategies can help: improving demand forecasting accuracy (using real-time data and advanced analytics), increasing collaboration and information sharing across the supply chain, implementing lean inventory management practices (like just-in-time inventory), stabilizing prices, and leveraging technology for better visibility and control.
What industries are most susceptible to the bullwhip effect?
Industries with long lead times, complex products, or highly variable demand are particularly vulnerable. Examples include the semiconductor industry, fashion apparel, and food and beverage, as demonstrated during the COVID-19 pandemic.