Embracing Mobility Essential in MRO Inventory, Field Service Operations
- Offline Mobility
- Inventory/Warehouse
- MRO
Maintenance and repair operations (MRO) demands managing a wide variety of materials. From equipment and expensive parts to inventory spares and consumables, each item must be tracked and stored. Failure to do so effectively risks loss of materials and operational delays.
Historically, organizations have used manual paper-based processes to manage MRO inventory. But these methods are not particularly accurate or efficient. Lost, misplaced, or out-of-stock materials are inevitable, delaying crucial maintenance.
To solve these challenges, MRO inventory management must catch up to modern standards. Mobile inventory solutions can digitize paper processes and automate manual tasks. The end result is real-time information with reliable visibility at reduced cost—an integral facet of today’s MRO inventory best practices.
The MRO Problem: Hidden but Solvable
Don’t let maintenance become an afterthought. Seemingly small issues can add up to big problems in the long run.
In a Modern Materials Handling report, industry experts Rick Wakeland and Phil Hebert sum up their experiences consulting on MRO projects. The two experts pooled their knowledge from initiatives spanning multiple industries and found common challenges.
For most MRO teams, the problems stem more from underlying issues of how maintenance and field services are handled than unique industry requirements.
A key problem for many organizations is a lack of awareness and transparency into MRO tasks. Maintenance is often overshadowed by other operational facets, leading to neglect. Over time, however, relegating MRO and field services to an afterthought allows small issues to escalate until they create major problems.
Common issues emphasized by Hebert and Wakeland included:
- Storing large quantities of outdated materials
- Inability to find materials to keep pace with work orders
- Frequent inventory discrepancies due to inaccuracy
- Extremely high back order rates
These day-to-day inventory management issues reduce productivity, increase downtime, and exacerbate the costs of expediting parts during an emergency. Wakeland and Hebert recommend developing key performance indicators (KPIs) to allow for greater day-to-day oversight of MRO activities.
To correct inefficient processes and track KPIs, companies must upgrade their maintenance inventory management software. Only then can real-time tracking and visibility be ensured, leading to lower costs.
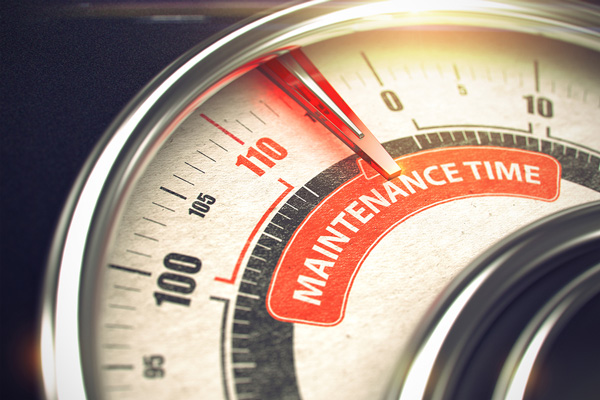
What MRO Metrics Matter?
READ NOW »The Importance of Constant Visibility in MRO
Real-time transparency in MRO might seem superfluous to some. After all, many inventory items, when viewed in isolation, may not appear to warrant meticulous tracking due to their low individual value. But perception can be misleading.
On any regular day, the consumption of materials follows a predictable pattern. Yet, when emergencies arise, this pattern can be disrupted, leading to sudden, unforeseen demands. When an emergency strikes, unexpected consumption can quickly escalate costs to the point that they far outweigh the value of the item itself.
Organizations often err by not investing in detailed tracking of low-cost consumables, deeming their wastage or excess supply as negligible. Yet, when emergencies strike, and a vital consumable is missing, the cost implications can be staggering.
To exacerbate matters, distributors are rapidly modernizing, integrating technologies that revamp inventory replenishment processes. If organizations remain stagnant, they risk being left behind, unable to leverage the efficiencies offered by today’s tech-infused operations.
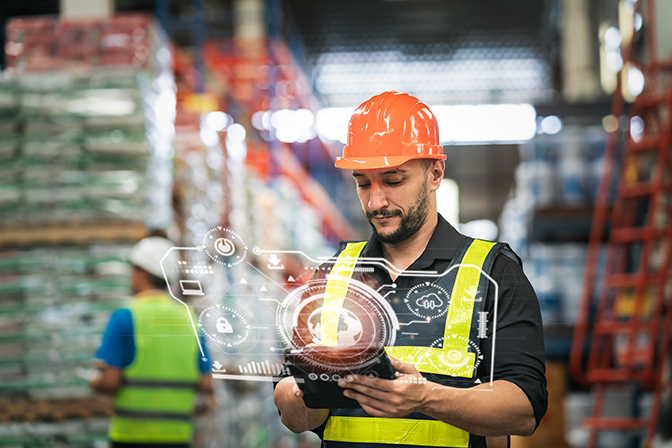
Tips on Jumpstarting Digital Transformation in MRO
LEARN MORE »An MRO Case Study
Manual paper-based operations may have served industries in the past, but they are riddled with inefficiencies and risks in the present context.
Imagine you have a maintenance worker heading to a remote facility to perform a repair. There’s a small warehouse at that location and your records indicate the necessary parts are present. The employee gets there, only to find that a necessary material has passed an expiration date and isn’t usable.
That means another trip back to the main warehouse to start over, leading to wasted time, increased costs, and potentially, extended downtimes.
Even if the records had been stored in an ERP system, there’s no guarantee that the records are accurate or timely.
All of these issues could be avoided with a modern mobile inventory system with real-time management of MRO spare parts, consumables, and fixed assets.
Watch Video: Defense Contractor Transforms MRO Supply Chain
Or read the case study here.
Leveraging Mobile Data Collection to Enhance MRO and Field Services
The problems shown above illustrate the need for mobile data collection in MRO and field services. Mobile barcoding extends the power of ERP systems into the hands of workers.
Using intuitive mobile apps and barcode scanning, they gain instant access to accurate information, in the warehouse and out in the field. Inventory visibility becomes live and reliable.
Mobile apps can be leveraged to manage fixed assets, automate cycle counts, provide access to maintenance documentation while on-site, and transact against the ERP under virtually any conditions.
Instead of making regular trips to the central office or various warehouses to transfer maintenance logs or check stock levels, these tasks are digitized and instantaneous. Enormous amounts of time, money, and productivity are saved.
In addition, mobile MRO inventory management software can:
- Reduce inventory errors to a minimum
- Optimize stock levels (reduce carrying costs)
- Streamline reordering and replenishment
- Track fixed asset expiry, check in/out, etc.
Thanks to mobile integration, real-time tracking of maintenance inventory generates upticks in productivity, efficiency, accuracy, and visibility. Day-to-day work for employees is greatly simplified. Pivoting to more value-added activities becomes possible—all while trimming operational costs.
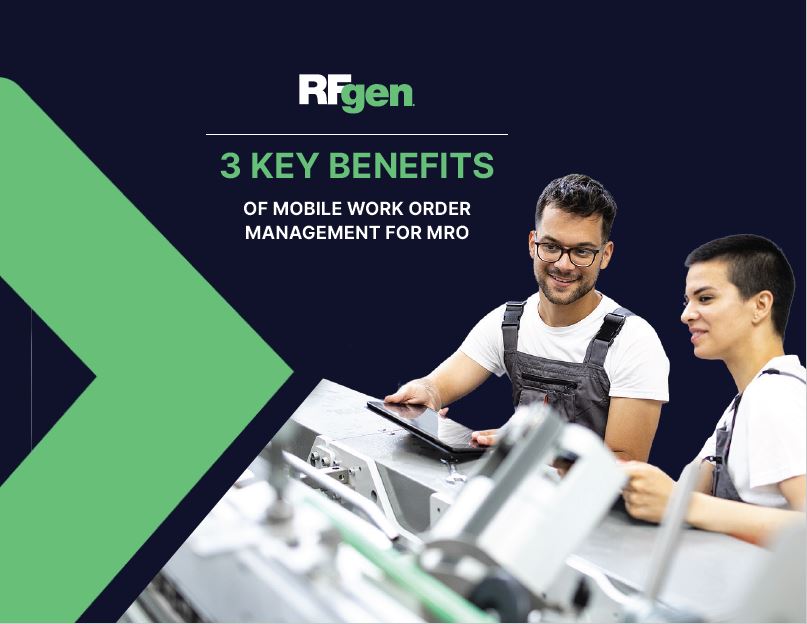
3 Benefits of Mobile Work Order Management for MRO
DOWNLOAD NOW »It’s Time to Modernize MRO & Field Services
As technological innovations continue to evolve in the supply chain, MRO and field services risk being left behind. Embracing mobile devices and data collection strategies can seemingly minor challenges to enhance efficiency, reduce costs, and create unparalleled operational transparency. Organizations must harness robust enterprise mobility solutions to empower the workforce, driving productivity—and profitability—to new heights.
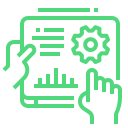