How Tariffs Disrupt Supply Chains: A Closer Look at Strategy, Inventory, and Resilience
- Supply Chain
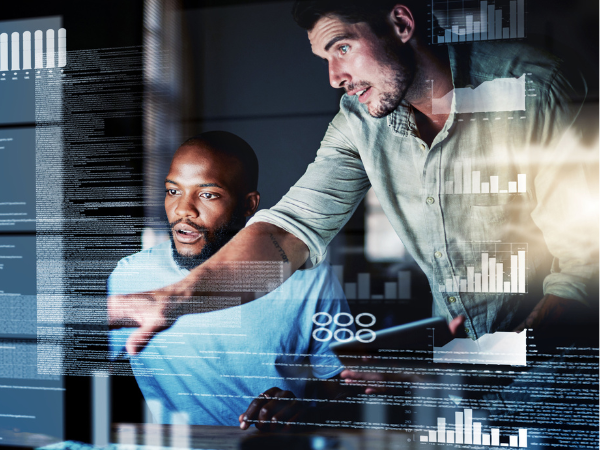
Tariffs were once background noise for most companies. They were a variable to watch but rarely something that rewired entire operations. That’s changed. The impact of tariffs on supply chains is no longer abstract. It’s direct, expensive, and increasingly hard to plan around.
From the new tariffs’ impact on supply chains to newer policy shifts between the U.S., China, and the EU, trade barriers are driving more than price changes. Tariffs are reshaping sourcing strategies, forcing tech upgrades, and making inventory planning a lot more complicated.
For global businesses relying on real-time logistics and lean inventory models, the question is how prepared is your supply chain when tariffs hit?
How Do Tariffs Affect Supply Chains? Immediate Cost Surges and Planning Chaos
The most obvious tariff impact on supply chains is pricing. Import tariffs raise the cost of raw materials, components, and finished goods. But the real disruption is in predictability. Companies operating on tight margins can’t always pass those cost increases onto customers. That means reworking contracts, renegotiating supplier deals, or even abandoning entire product lines. The cost of these downstream hurdles is lost time.
Renegotiating Contracts:
When tariffs suddenly raise the cost of raw materials or finished goods, companies face the challenge of deciding whether to absorb the cost or pass it on to customers. For businesses with slim margins, simply increasing prices isn’t an option. This forces companies to revisit and rework contracts with suppliers and customers, a process that demands time-consuming negotiations and legal reviews.
Supplier Deal Adjustments:
With tariffs altering cost structures, businesses must reexamine their supplier relationships. Negotiating new terms or finding alternative suppliers takes time—time that would have been better spent on refining production and enhancing efficiency. The uncertainty in pricing means that even established, long-term supplier agreements might need to be adjusted, leading to disruptions and delays in the supply chain.
Strategic Reevaluation:
Tariff-induced cost pressures might even push companies to abandon entire product lines that can no longer be profitable. This strategic pivot requires comprehensive analysis, market research, and operational adjustments. Such evaluations are not instantaneous; they involve multiple departments and careful planning, which further translates into valuable time lost.
Operational Delays:
All these adjustments—contract revisions, supplier renegotiations, and strategic shifts—delay day-to-day operations. Instead of focusing on production, innovation, or customer service, companies are forced to manage these administrative hurdles, delaying activities that generate revenue and improve business growth.
Imagine a mid-market fitness equipment company sourcing metal frames from Taiwan. A sudden 20% tariff hits, raising costs overnight. Do they absorb the blow, hike prices, or race to find a new supplier in Vietnam? None of those choices are cheap or fast.
This is the dilemma many companies face. And when tariff decisions drop with little warning, companies are forced into reactive mode. That kind of volatility breaks traditional supply chain models.
When Tariffs Disrupt Global Supply Chains, Inventory Models Shift
Traditionally, companies have relied on just-in-time (JIT) inventory strategies to minimize storage costs and reduce waste. But when tariffs disrupt global supply chains, JIT becomes a liability. Instead, companies start shifting toward just-in-case (JIC) models and stockpiling inventory to insulate themselves from sudden trade barriers.
Consider a hypothetical example: a U.S.-based cosmetics brand sources glass jars from Europe. Instead of waiting for an unexpected EU tariff to force a reaction, the brand closely monitors market and policy trends. By proactively diversifying suppliers and integrating dynamic risk assessments into their planning, they set up strategic inventory buffers well in advance. This approach avoids the need for reactive measures such as suddenly leasing a warehouse in New Jersey to store six months of inventory. This would lock up cash and drive-up warehousing costs.
By planning ahead, companies can balance operational efficiency with flexibility, ensuring that when tariffs or other trade disruptions hit, they are not scrambling to rebuild their supply chains. Proactive strategies not only reduce the risk of costly reactive measures but also help maintain a competitive edge in an unpredictable global market.
Creative Moves: Tariff Engineering and Supply Chain Rerouting
One of the more creative responses to tariffs and supply chain challenges is product modification. Some companies engage in “tariff engineering,” tweaking product specs to fit into lower-duty classifications.
Example: A bicycle manufacturer adds a rear reflector and bell, reclassifying the bike as a safety transport device, reducing the duty rate by 10%. This strategy, while niche, shows how adaptive companies can be when incentives are clear.
Another trend? Rerouting global supply chains to minimize tariff exposure. That could mean shipping through tariff-friendly trade zones or taking advantage of agreements like USMCA.
A German auto parts supplier that once shipped directly to U.S. ports may now route through Mexico. It adds days to delivery—but saves millions in duties.
The Tariffs Supply Chain Playbook: Rethink, Relabel, Relocate
The broader tariffs supply chain is not just a checklist to follow when disruptions hit; it is a proactive strategy to future-proof your operations. Here is how each element addresses current tariff challenges while setting you up for long-term resilience:
Rethink Sourcing:
Companies are now diversifying suppliers to mitigate risks even when it means sacrificing the convenience of long-term contracts. A heavy reliance on a single region such as Southeast Asia exposes businesses to severe disruptions when tariffs shift. By expanding your supplier base early, you create a flexible network that adapts to market changes. This proactive approach lays the groundwork for a more resilient supply chain, a core tenet of RFgen offerings.
Relabel and Redesign:
Adjusting product designs to modify classification codes offers a strategic lever to reduce duty costs. Sometimes a minor design tweak can significantly cut tariff liabilities. This strategy is about embedding agility into your product development process instead of reacting after the fact. By considering these adjustments before tariffs hit, you can manage costs more effectively and remain ahead in a competitive market. We advocate for continuous innovation as a key tool in future-proofing supply chains.
Relocate Production:
Investing in nearshoring and moving production closer to end markets can minimize tariff exposure. Although this may result in higher production costs initially, advancements in automation offset labor cost concerns, making the trade economically viable. For example, a drone company that moved part of its assembly from China to Arizona experienced cost increases; however, the adjusted tariff math ultimately worked in their favor. Our approach emphasizes that strategic relocation is not merely a reaction but a long-term investment in a sustainable supply chain.
Together, these strategies emphasize an important message. Waiting for a tariff shock can leave you scrambling for solutions, whereas adopting proactive measures today transforms potential disruptions into opportunities for sustained competitive advantage.
One example? A drone company that once relied entirely on Chinese assembly moves part of its production to Arizona. The costs go up, but the tariff math still works in their favor.
How Do Tariffs Affect Global Supply Chains in the Long Run? More Than You Think
The impact of tariffs on global supply chains is about more than cost—it’s about control. In a tariff-volatile world, flexibility becomes more valuable than optimization.
That’s why companies are investing heavily in visibility tools. ERP and inventory systems are being upgraded to track landed costs, simulate tariff scenarios, and adapt procurement strategies on the fly.
In one case, a global retailer used machine learning to anticipate trade tension between two Asian economies. Their system flagged the risk weeks before a new tariff was announced. As a result, the company pre-ordered inventory and switched to a secondary supplier—beating the disruption and keeping product on shelves.
That kind of responsiveness is the new bar. If you can’t model tariff outcomes and adjust accordingly, you’re likely leaving money—and market share—on the table.
Digital Transformation Is the Only Way Forward
For companies still operating with legacy systems or spreadsheets, there’s no room for slow decision-making. Tariff complexity demands digital tools that can manage real-time data, compliance shifts, and logistics flows.
Advanced supply chain management systems now include modules for trade compliance, dynamic pricing, and international tax modeling. AI and machine learning are being deployed to predict regulatory changes, optimize inventory allocation, and even recommend supplier switches based on evolving tariff landscapes.
As more organizations embrace digital transformation, supply chain agility will become a key competitive advantage for cost savings and risk mitigation.
Businesses must embrace digital tools to manage real-time data, compliance shifts, and logistics flows. RFgen’s solutions enable automation, enhancing both efficiency and resilience by providing advanced capabilities like trade compliance, dynamic pricing, and AI-driven predictions for regulatory changes and supplier optimization.
Key Areas RFgen Transforms:
- Smart Inventory Management: RFgen enables real-time tracking of inventory accuracy and turnover, helping businesses make informed purchasing decisions and avoid overstocking or stockouts, even during market disruptions.
- Optimized Warehouse Operations: With RFgen, businesses gain visibility into order cycle times, perfect order rates, and supplier quality, improving order fulfillment and ensuring reliability despite economic volatility.
- Operational and Manufacturing Efficiency: RFgen automates data collection for production downtime, scrap rates, and OEE, enabling manufacturers to identify and address bottlenecks quickly, ensuring consistent productivity.
- Financial Impact and Cost Management: RFgen provides insights into revenue per unit, labor costs, and time-to-market, helping businesses adjust strategies to maintain profitability amid rising costs and tariffs.
By leveraging RFgen’s mobile solutions, businesses can streamline processes, enhance agility, and future-proof their supply chains to stay competitive in an unpredictable market.
New Tariffs Impact on Supply Chain Still Lingers
It’s worth noting that while tariff headlines have cooled temporarily, their long-tail effects still ripple through global supply chains. The current tariffs, particularly those targeting Chinese goods, forced companies to redesign sourcing strategies that took decades to build.
Even as some of those policies are revisited, the structural changes they triggered are here to stay. Many firms that pivoted during this period haven’t returned to old patterns. Instead, they’ve built redundancy into their supply chains—a hedge against future political disruptions.
The lesson? Tariffs may come and go, but the systems you build to handle them stick around.
Tariffs Are Testing Supply Chain Resilience
So, how do tariffs affect supply chains? In every way. They add cost, complexity, and uncertainty. They force businesses to reassess what resilience looks like and to put real resources behind building it.
The companies thriving under tariff pressure aren’t just the biggest or most established. They’re the ones that act fast, run smart systems, and make bold bets on agility.
Because in today’s trade environment, success is about absorbing the hit and coming out stronger, smarter, and more responsive than before.
Now is the time to future-proof your operations. By adopting a proactive strategy today, you can anticipate market shifts and emerging challenges before they disrupt your business. With RFgen’s industry-leading expertise and tailored solutions, we’re here to help you build a resilient supply chain that turns uncertainty into opportunity.
Get started now and secure your competitive edge for the future. Contact our experts today for a personalized assessment to see how our expertise can help you build a resilient, forward-thinking supply chain for the challenges of tomorrow.