Inventory Management and Warehouse Management: A Detailed Comparison for Supply Chain Professionals
- Inventory/Warehouse
Top Takeaways:
- Inventory management and warehouse management sound like synonyms, but there are several differences between them.
- While inventory management is more specific, warehouse management tends to be broader and more holistic.
- Understanding their overlap, differences, and how they interact is crucial for mastering supply chain best practices.
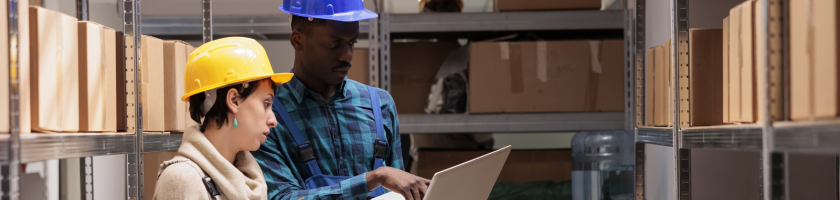
When it comes to handling inventory in supply chain management, a lot of terminology gets thrown around. For newcomers and business partners, many of these terms may sound like different jargon all referring to the same thing.
Take inventory management and warehouse management. Inventory handling is part of managing a warehouse, so does that mean they are interchangeable?
While inventory management is theoretically a part of warehouse management, they refer to two separate but related concepts. Both are vital components of effective supply chain management. Both work hand-in-hand. Both ensure product flows through your operation.
So what’s the difference?
This article will explain the difference between inventory management and warehouse management, where they overlap, and how they are different.
Inventory Management
What is Inventory Management?
Inventory management is the tracking and controlling of products. This includes all inbound processes for goods and materials, such as ordering, receiving, storing (“put-away”), moving, and usage.
“Inventory” can take the form of finished goods, raw materials, unfinished or WIP items, spare parts, consumables, and fixed assets.
Managing inventory means monitoring stock levels to ensure sufficient levels for manufacturing and order picking, as well as maintaining the optimal balance between having too much inventory and not enough.
Inventory tracking ensures smooth supply chain operations while minimizing overhead.
Key Concepts & Principles
Key concepts of inventory management include:
- Stock control
- Demand forecasting
- Reorder points (replenishment)
- Safety stock
- Inventory turnover (“turns”)
- Cost management
Understanding inventory management best practices requires mastery over principles such as:
- Balancing inventory cost with the cost of stockouts
- Aligning optimal inventory levels with customer demand
- Continuous monitoring of stock levels and inventory processes
- Evaluation and refinement of material handling processes
- Leveraging technology to optimize efficiency and accuracy
Types of Inventory Systems
Many types of inventory management strategies exist. Each methodology has its own strengths and weaknesses and is best suited for certain situations depending on the needs of the business.
Common types of inventory systems include:
- Fixed Order Quantity (FOQ) system
- Fixed Time Period (FTP) system
- Continuous Review system
- Reorder Point system
- Just-In-Time (JIT) system
Ultimately, the choice of system—or blend of systems—will depend on the type of operation, type of product, rate of sales, lead time, cycle time, and stocking requirements.
Regardless of type, an effective inventory management software system (IMS) will be needed for all but the smallest businesses. Larger companies with high-volume operations will use an Enterprise Resource Planning (ERP) platform coupled with a mobile barcoding component to handle complex, fast-moving inventory flows.
“Used correctly, inventory management software can be an essential starting point for businesses to better manage stock levels and materials while driving down expenditures.
The Comprehensive Guide to Mobile Inventory Systems
ALSO READ »Benefits of Good Inventory Management
The benefits of good inventory management practices are numerous. They include:
- Improved customer satisfaction by ensuring stock availability
- Increased efficiency and reduced lead times
- Reduced costs by minimizing overstocking, stock obsolescence, and shortages
- Improved cash flow from lower carrying costs and better use of working capital
- Better decision-making through accurate and up-to-date inventory data
Inventory management best practices dictate the need for mobile software that improves KPI metrics while reducing overhead costs. Having a mobile inventory platform in place helps companies evaluate stock levels in real-time, operate more efficiently, and improve customer satisfaction and profitability.
Warehouse Management
What is Warehouse Management?
Warehouse management refers to the oversight of the storage, handling, and movement of goods and materials within a warehouse. This includes the organization, layout, and storage of inventory, as well as all outbound inventory processes, such as picking, packing, and shipping orders.
The goal of warehouse management is to minimize waste and overhead costs while improving efficiency and accuracy to deliver the best possible customer service and profit margins.
Key Concepts & Principles
Key concepts of warehouse management include:
- Storage layout, design, and utilization
- Inventory control
- Order pick/pack/ship
- Material handling equipment
- Accuracy and quality control
The most important principles of warehouse management often include:
- Maximizing space usage (“cube utilization”)
- Streamlining warehouse processes
- Enhancing efficiency and performance with technology
- Tracking of KPIs for continuous improvement
Types of Warehouse Systems
A variety of warehouse systems are typically employed in any given operation. Each type comes with advantages and disadvantages and may only be useful for certain types of facilities, depending on company size and the level of automation desired.
Common types of warehouse systems include:
- Manual systems (paper, spreadsheets, tribal knowledge)
- Basic computerized systems (requires data entry)
- Automated storage and retrieval systems (ASRS)
- Cross-docking systems
- Mobile warehouse management systems
Large enterprise operations often use warehouse management software (WMS) to handle highly sophisticated supply chain workflows. WMS platforms integrate with other enterprise software, including production and sales programs, as well as ERP systems.
However, WMS software is expensive and lengthy to implement, and not always needed. Many companies opt for more lightweight solutions like WMS-lite or mobile inventory software to achieve the most critical WMS capabilities.
How to Create Value with Warehouse Automation Software
ALSO READ »Benefits of Good Warehouse Management
Implementing warehouse management best practices is the best way to gain the most benefits: Benefits can include:
- Improved process efficiency and space utilization
- Heightened quality with accurate data, stock levels, and orders
- Reduced operating, carrying, and labor costs
- Improved order delivery speed and customer satisfaction
- Increased security of goods and safety of personnel
Technology shouldn’t be overlooked when looking to maximize these benefits. Highly effective mobile solutions that unify data from different systems into one interface enable accelerated inventory workflows without burdening operations with a slow return on investment (ROI).
Differences Between Inventory and Warehouse Management
Key Differences Between the Two Systems
Of the two, inventory management is more specific. Whereas inventory management takes a basic approach to handling stock, warehouse management offers a more comprehensive methodology that encompasses all aspects of running and improving warehouse operations.
Inventory management focuses on material handling, including ordering, receiving products, tracking inventory levels, and pick/pack/ship for production and outgoing orders.
Warehouse management focuses on the day-to-day operations of the warehouse, which may or may not overlap in some areas with inventory control.
Some supply chain professionals may also use the terms “inventory management” and “warehouse management” to refer to inbound and outbound processes, respectively.
What Do They Have in Common?
While there are differences between inventory and warehouse management, they also have several things in common:
- Both are critical components of supply chain management, using oversight to ensure the efficient flow of goods from suppliers to customers.
- Both require careful planning and organization to optimize operations and reduce costs.
- Both need accurate, up-to-date data to make informed decisions and minimize errors.
- Both benefit from the use of technology (e.g., barcoding, RFID, etc.) to improve accuracy and efficiency.
- Both require close collaboration and alignment between different departments to ensure customer satisfaction and profitability.
How They Interact With One Another
Inventory and warehouse management are closely linked. They interact with each other in several important ways:
- Inventory management provides the critical data needed for effective warehouse management.
- In turn, warehouse management provides the physical storage, infrastructure, and logistics for material handling.
- Because the two are interconnected, storage utilization and bin placement are determined by stocking requirements and inventory turnover.
Ideally, companies will dedicate resources to optimizing both inventory management and warehouse management synergistically, since the performance of one inevitably affects the other.
3 Steps to Run a Successful Warehouse
KEEP READING »How They Can Be Integrated
When it comes to integrating inventory and warehouse management, enterprise resource planning (ERP) systems are fundamental. Not only does an ERP standardize procedures, it offers a centralized platform for tracking inventory, costs, and material movements.
Additional technologies can further enhance the ERP’s functionality. Barcode software helps ensure inventory accuracy. Mobile inventory can extend ERP capabilities to point-of-scan, freeing workers from menial data entry and fixed workstations.
Other supply chain tech, like RFID and pick-to-light systems, offers additional layers of tracking and productivity. A WMS platform offers the greatest capabilities of all, but with a tradeoff of high cost and complexity. Core WMS functions like intelligently directed material movements and optimized picking paths can still be achieved with WMS alternatives, like a WMS “lite” or warehouse automation software.
Regardless, integrating all methods of data collection into a singular system of record is ideal. Assembled data can then be leveraged to provide more granular and actionable insights for the business. Enhanced insights and decision-making translate to greater performance and faster ROI from the warehouse technologies that helped the operation get there.
Future Outlook for Inventory and Warehouse Management
Inventory management and warehouse management share several common goals. Effective coordination between the two areas is crucial to ensure smooth, efficient supply chain management.
Integrating keystone technologies like an ERP platform and mobile barcoding will be an essential best practice for larger warehouse facilities, especially those running high-capacity, complex operations at multiple sites.
In addition to these “must-have” prerequisites, the supply chain’s technological landscape is one of continuing growth and innovation, driven by an ever-changing market.
Some of the major developments that will impact the future outlook of inventory and warehouse management include:
- Increased use of advanced technology: While the Internet of Things (IoT), warehouse co-bots, and automation are already on the rise, the disruptive impact of artificial intelligence (AI) looms on the horizon.
- E-commerce growth: Consumer behavior will continue to drive demand for more efficient and effective warehouse management and inventory control systems, particularly in order fulfillment and last-mile delivery.
- Big data and analytics: The increasing availability of data and the use of insights from in-depth predictive analytics will enable supply chain professionals to make more informed decisions, but requires automated data capture.
- Sustainable supply chain practices: Increasing emphasis on sustainability and waste reduction will push companies toward more environmentally friendly inventory handling, warehouse management practices, and purchasing procedures, such as digitization.
- Customer-focused approach: As always, businesses must position themselves to deliver superior customer experience, with a particular emphasis on speed and flexibility, courtesy of real-time inventory tech.
Why Doing Nothing Can Cost You Big in the Warehouse
READ MORE »FAQs
What is the difference between inventory and warehouse management?
Inventory and warehouse management have some overlap but also several important differences. Whereas inventory management involves the oversight and control of materials, warehouse management is focused on the storage and movement of goods. Sometimes they both can refer to material handling in general. Other times, supply chain professionals may refer to “inventory management” for inbound processes and “warehouse management” for outbound processes.
How do inventory and warehouse management interact with one another?
Inventory management and warehouse management are interconnected components of supply chain management that work together to ensure the effective flow of goods. While inventory management determines the quantities and placement of items, warehouse management focuses on the storage and logistics of those items.
What are the benefits of good inventory management?
Good inventory management offers many benefits: greater inventory and order accuracy, boosted efficiency, lower overhead costs, faster inventory turns, increased customer satisfaction, and better decision-making. By accurately tracking inventory levels and movements, businesses can avoid stockouts, reduce emergency and last-minute restocking, and pivot quickly to changing market demands.
What are the benefits of good warehouse management?
Good warehouse management provides multiple benefits: improved efficiency, greater workforce productivity, reduced costs, more profitability, and elevated customer service. By effectively optimizing the storage and movement of goods, businesses can reduce errors, minimize waste, and ensure smooth operations.
How can inventory and warehouse management be integrated?
Inventory and warehouse management can be integrated by using keystone technologies like ERP software, mobile inventory management solutions, and warehouse management systems (WMS/WMS alternatives). Close integration of these systems enables real-time visibility, accuracy, and control.