Navigating the Warehouse Labyrinth: Unraveling the Mystery of Mispicks and Crafting Foolproof Solutions
- Data Collection
- Inventory/Warehouse
Anyone who handles inventory is familiar with the dreaded “mispick.”
Mispicks, a common issue in warehouses and distribution centers, occur when an incorrect item is picked from inventory during the order fulfillment process. Often, this is attributed to human error.
These simple mistakes can lead to financial losses and dissatisfaction among customers.
Understanding the underlying causes of mispicks is important in order to implement effective strategies that prevent them from happening in the first place.
In this article, we will look at the common causes of mispicks and provide practical solutions to help you reduce errors, improve efficiency, and enhance customer satisfaction.
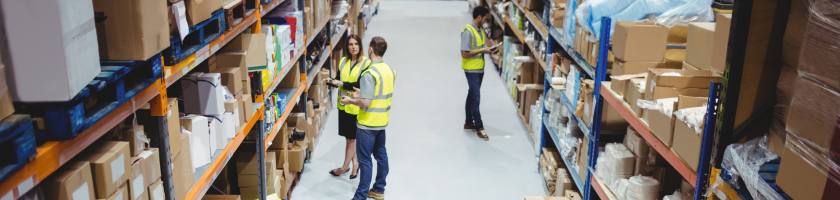
Common Causes of Mispicks
Human Error
Simple mistakes are a leading cause of mispicks. These errors usually arise from:
Misreading product labels. Warehouse employees may inadvertently pick the wrong item if the labels are confusing, poorly printed, or too similar to other labels. Additionally, employees may struggle with illegible handwriting or mistakes on handwritten labels.
Miscommunication. Miscommunication between warehouse employees can lead to mispicks. For instance, employees may receive incorrect or unclear instructions from their supervisors or colleagues, leading them to select the wrong items from the inventory.
Manual processes. As long as human beings are involved, there’s always a risk of a mispick—especially if workers are rushing to get the job done. The risk is significantly greater if workers rely on tribal knowledge and paper printouts. Employees can easily misread a SKU or skip a critical item on an outgoing order.
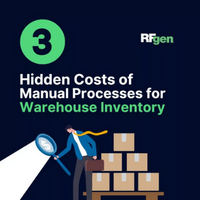
Uncover the 3 Hidden Costs of Manual Warehouse Processes
DOWNLOAD NOW »Inadequate Training
Insufficient training is another common source of mispicks, especially among new or seasonal employees. Newer employees tend to lack full understanding of the inventory management system and are more likely to make mistakes. Manual processes present a drastically longer and more difficult learning curve than mobile automation.
Workers may also have subpar knowledge of the technology tools they use, such as barcode scanners and other mobile devices.
Poor familiarity with the facility layout and product locations also impacts accuracy, necessitating training in this area as well. A rushed employee is apt to pick a similar-looking item from nearby shelves instead of the correct item stored elsewhere.
Poor Warehouse Organization
Warehouse organization is very important for efficient inventory control, leading to mispicks. Two major areas are to blame:
Inefficient Product Layout
An inefficient product layout can contribute to mispicks, as it may make it challenging for staff to locate and identify the correct items. For example, placing similar items close together may lead to confusion, while an unorganized layout may cause employees to waste time searching for products and increase the likelihood of picking errors.
Inaccurate or Outdated Inventory Records
Inaccurate or outdated inventory records can cause mispicks because workers rely on these records to locate and pick items. If the inventory records do not accurately reflect the actual stock levels and locations, team members may pick the wrong items or be unable to find the correct items in the warehouse.
Suboptimal Picking Processes
The Holy Grail of mispicks is the picking process itself.
Any inefficient picking method leads to mispicks, especially when employees struggle to keep track of multiple orders and items at once. Manual picking processes inevitably lead to wrongly picked items, especially in large warehouses with diverse product ranges.
A lack of standardized picking procedures also contributes to mispicks, as staff may develop their own methods and shortcuts, leading to inconsistencies and errors, not to mention siloed knowledge. Standardization is central to ensuring all team members follow the same process and pick the right items.
Strategies to Prevent Mispicks
There are a number of proven strategies to reduce mispicks, such as:
Implementing Technology Solutions
Barcode Scanning Systems
Implementing barcode scanning systems is the best way to minimize the risk of mispicks. Barcoding automates the identification and verification of items during the order picking process. Employees can use handheld barcode scanners or mobile devices equipped with scanning capabilities to scan the barcodes on products and confirm that they have picked the correct items.
Mobile barcoding solutions can also be integrated with ERP systems and other enterprise software platforms to update inventory records in real time, ensuring that employees have access to accurate and up-to-date information when picking items.
RFID Technology
Radio Frequency Identification (RFID) technology is another solution that can help prevent mispicks. RFID tags attached to products store more information than traditional barcodes and can be read without direct line-of-sight, making the picking process faster and more efficient. Like barcode software, RFID can be integrated into other mobile warehouse management systems to provide real-time updates on inventory levels and locations.
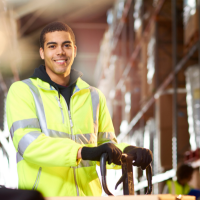
Learn more effective tips for finding and training top warehouse workers that stay.
READ NOW »Warehouse Management System (WMS)
A WMS is a heavyweight software solution that helps manage and optimize warehouse operations with high degrees of control. By implementing a WMS, businesses can improve inventory tracking, streamline picking processes, and automate warehouse tasks, reducing the likelihood of mispicks.
While WMS solutions provide valuable insights and analytics, they are also the most expensive and resource-intensive option for improving accuracy.
Some warehouses opt for a more flexible advanced warehouse alternative with some WMS capabilities.
Enhancing Employee Training and Development
As mentioned above, poorly trained workers tend to pick wrong items more often. To change this, consider investing in comprehensive training programs for warehouse employees. Training should cover the use of technology tools, such as handheld barcode scanners and mobile devices, as well as procedures and best practices.
Shadowing more tenured team members can help newer employees familiarize themselves with the warehouse floor plan and product locations.
Providing regular refresher courses and workshops can help reinforce best practices and keep employees up to date with operational changes. This way, workers will have the necessary skills and knowledge to accurately pick items in the most efficient means possible.
Improving Warehouse Organization
Since picking takes place in the warehouse, making adjustments to organization and layout is another foolproof way to reduce mispicks.
Optimizing product layouts can significantly reduce the risk of mispicks by making it easier for employees to locate and identify items. Items that are frequently picked for orders should be placed in areas that are accessible. Meanwhile, rarely picked items can be placed farther away.
Other product layout strategies may include grouping similar items together, kitting commonly associated items together, organizing items by popularity, or implementing a zone or wave picking system.
Regardless of which method you use, keep the end goal in mind—a more efficient, intuitive warehouse environment.
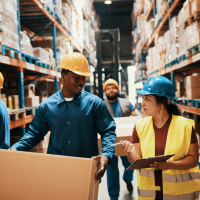
How to pick your way to success with faster picking speeds at maximum accuracy.
READ NOW »Streamlining Picking Processes
And don’t forget about the picking processes. If your current process is generating an unacceptable number of mispicks, then it’s time for a change.
First, consider adopting a standardized picking procedure. This will help ensure that all team members follow the same process. Standardized procedures should be clearly documented and communicated to all employees. Supervisors should monitor compliance to ensure consistency across the workforce.
Next, look into advanced picking strategies tailored to your business needs. Choosing a more appropriate methodology can be instrumental to squashing picking errors.
While advanced picking procedures reduce errors and improve efficiency, not every picking strategy will be equally effective for your specific environment. Evaluate multiple options, like batch picking, zone picking, wave picking, and directed picking, then select the one (or several) that best suits your operation’s requirements.
Monitoring and Continuous Improvement
Regularly Review Mispick Rates
Monitoring mispick rates can help you identify trends and patterns so you can address issues in the picking process. Even relatively small tweaks may affect mispick KPIs. By tracking the impact of new strategies, your operation can make data-driven decisions to determine which solutions are most effective at eliminating mispicks.
Encourage Employee Feedback
Employee feedback is a valuable resource for identifying areas for improvement and addressing the root causes of mispicks. Create open communication channels, such as suggestion boxes or regular team meetings, to encourage staff to share their ideas and concerns. Involving employees in the improvement process can also increase their engagement and commitment to preventing mispicks.
Adapt and Refine Strategies
As a business, continuous refinement and improvement is always a goal. When it comes to picking strategies, be prepared to analyze mispick data and weigh employee feedback before making process adjustments.
And just because you’ve improved mispicks with a new strategy doesn’t mean there isn’t further room for improvement. Continue to seek out opportunities for improvement.
Ensure your operation stays ahead of potential issues while also maintaining the highest level of picking accuracy.
Replacing Mispicks with Perfect Orders
The process of preventing mispicks is an ongoing struggle. Eliminating mispicks is essential to improving cost control and warehouse operations, not to mention that perfect orders keep customers happy.
By staying up to date with industry best practices, technological advancements, and evolving customer needs, businesses can proactively address potential issues and ensure that their picking processes remain accurate and efficient in the long term.
Remember: the key to creating a perfect order is a perfect pick, and a perfect pick requires flawless mobile tech to make it happen.