Reasons for Physical Signs in a Digital Warehouse
- Asset Tracking
- Offline Mobility
- Inventory/Warehouse
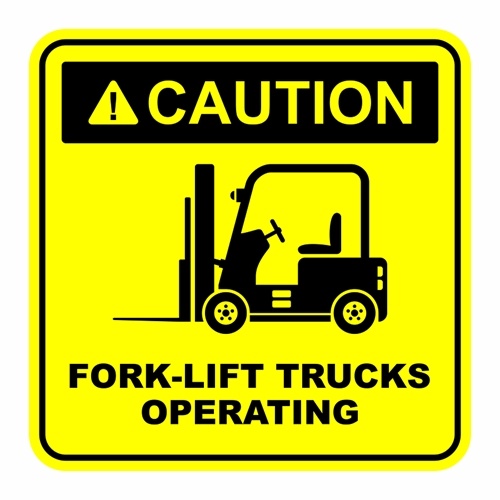
Warehouse automation software should provide employees with all the information they need to perform their daily duties. If companies supply inventory workers with mobile automated data collection solutions, the users should be able to look up order information, management instructions and material handling procedures.
The use of physical signs may seem superfluous when compared to the wealth of information digital solutions can provide. Companies shouldn’t neglect signage, however. Warnings, reminders and labels used throughout a business space provide the consistency workers need to succeed. Here are a few ways signs can work in conjunction with mobile data collection solutions:
Safety
Warehouses can be dangerous places. Many inventory spaces utilize some combination of hazardous equipment, storage locations reaching potentially dangerous heights and heavy materials. To keep everyone safe, a company must ensure everyone who walks the area has the necessary information.
Mobile devices are great security solutions. They can provide detailed instructions and best practices for working with dangerous materials and deliver automatic warnings for when forklifts operate for too long or if products need special storage locations. Not everyone who walks through a warehouse is an employee, though. Riskex Pty Ltd., a safety assessment company, reminded business managers dangerous spaces receive outside visitors and detailed signage is important to warn everyone of hazards.
Businesses can never be too cautious about safety. While employees have all the details they need on mobile data collection solutions, eye-level warnings keep safety forefront in their minds and remind them to drill down into information systems to learn more.
Efficiency
Mobile solutions provide warehouse workers with convenient devices. If an employee needs to double-check order information when picking products, a mobile data collection device allows him or her to see the details that came straight from the customer. Sometimes it’s much faster to just check the information right in front of his or her face, however.
The Construction Equipment Distribution Blog said managers should label their warehouses so clearly that brand-new employees could perform tasks. Providing workers with multiple options for complete information resources allows them to choose the method most convenient for the particular task. Employees should be able to search for layout details on their phones, with their co-workers or on the shelves.
Consistency
When companies have each source of business data displaying the same details, it drives home the information employees need for routine success. An RFgen datasheet said consistent data is one of the primary advantages a mobile enterprise application platform provides. Signs can help by offering another source of data that supports consistent warehouse procedures.
If warehouse workers perform operations utilizing a mobile device like voice picking, they need to communicate what they see in the same language managers expect from the software. Warehouse signs help create an easy transition from digital layouts to physical spaces. If the software segments an aisle and labels it with a certain code, having that code on display for workers who frequent the aisle ensures there’s no confusion between plans and actions.
Visibility
Companies may augment physical signs to make them more helpful. Workers can use signs with barcode data collection tags to report regular activities. Warehouse labels that provide information for automated data collection solutions can give managers the details they need to turn real-world events into recordable data.
Employees who scan shelves at the same time they scan products create an even clearer picture of performance. A properly implemented system may prevent workers from storing items on the wrong shelves or taking merchandise from existing orders. Automated data collection visibility may also inform signage procedures. If constant reporting indicates unsafe trends or a need for further instruction, it lets managers know when more signs are necessary or if current labels should change.