The Role of Stock Balancing in Supply Chain Optimization
- Data Collection
- Mobile Inventory Management
- Inventory Management Software
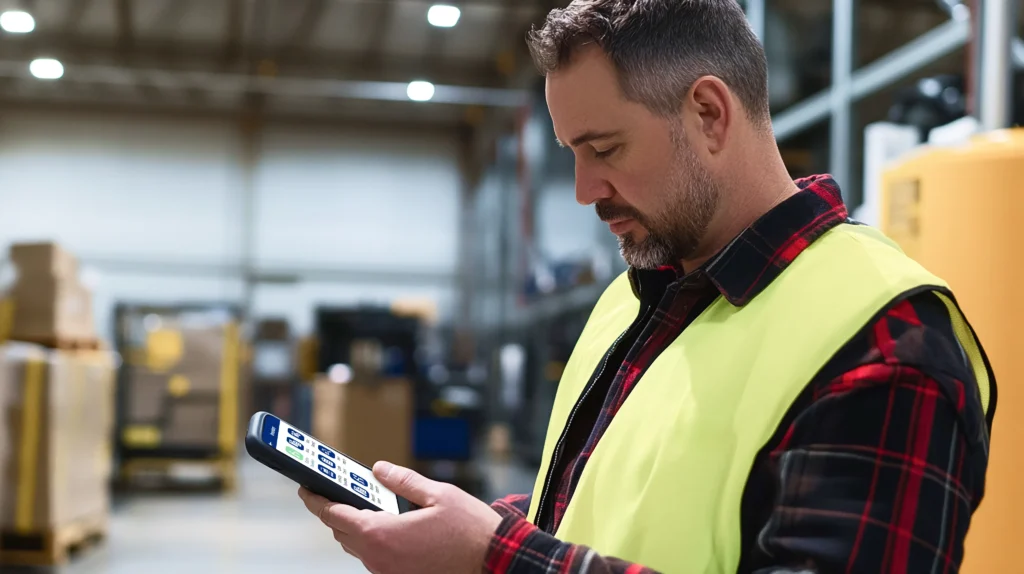
Supply chain disruptions have become all too common. But the realities on the ground are often far more nuanced than a simple shortage or surplus. While some warehouses overflow, others sit nearly empty, creating a frustrating paradox of excess and scarcity. This imbalance isn’t just an operational headache; it’s a drain on efficiency and a major threat to customer satisfaction.
The problem lies in effectively balancing inventory across the supply chain. This critical aspect of optimization is often overshadowed by flashier supply chain trends. When demand surges, inventory needs to rise, and vice-versa. However, as we’ve seen in recent years, predicting these shifts and adjusting inventory accordingly is far from simple.
Businesses must move beyond reactive responses to anticipated demand shifts. Stock balancing, the strategic redistribution of inventory across locations, emerges as a key solution. By ensuring optimal stock levels where demand exists, businesses can minimize holding costs, prevent lost sales due to stockouts, and ultimately, keep customers happy.
In this article, we’ll delve into the challenges of stock balancing, explore effective strategies, and examine how this often-overlooked practice can significantly impact your bottom line.
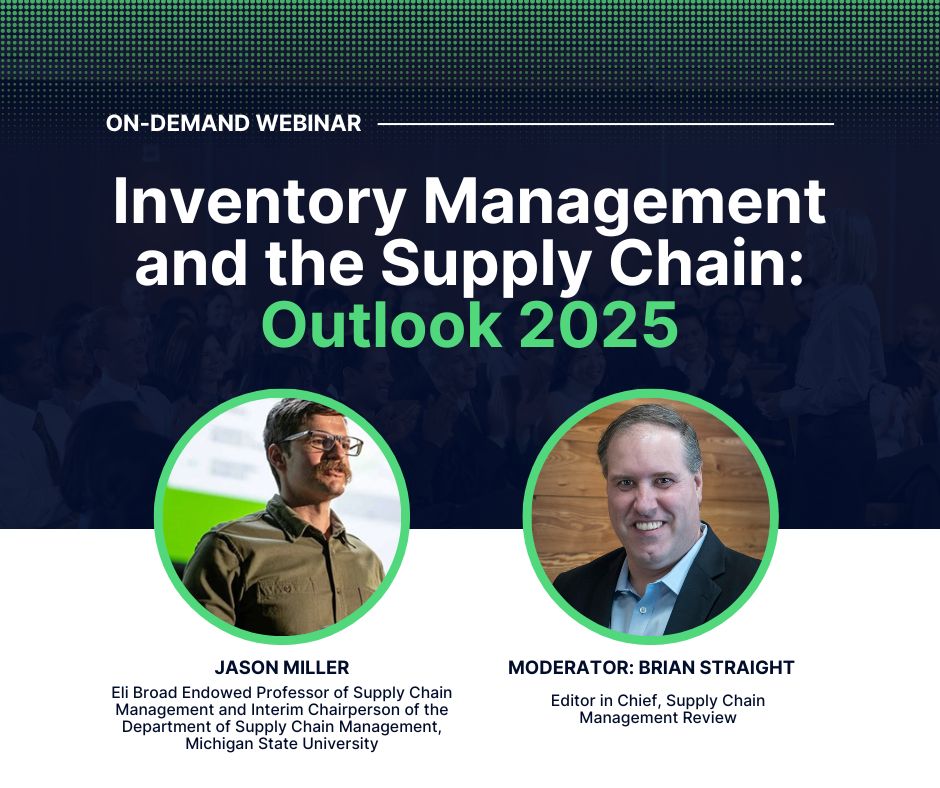
Mastering Inventory in 2025: Key Trends Watch Webinar Now
WATCH WEBINAR »What is Stock Balancing?
Inventory balancing is the strategic redistribution of inventory across different locations within a supply chain. It’s about ensuring the right amount of product is available at the right place, at the right time. Instead of having excess stock sitting idle in one warehouse while another location faces stockouts, inventory balancing aims to optimize inventory allocation based on actual demand.
Jason Miller, the Eli Broad Endowed Professor of Supply Chain Management at Michigan State University, explains that effectively managing inventory requires an understanding of the dynamic relationship between demand and supply.
A practical example of inventory balancing in action would be a national retailer noticing high demand for winter coats in their Northeast stores, while Southwest stores experience a surplus. By transferring excess inventory from the Southwest to the Northeast, the retailer meets customer demand, minimizes the risk of lost sales, and avoids unnecessary storage costs. This proactive approach ensures that products are available where and when they are needed most.
Poor inventory balancing can have significant negative consequences on the bottom line. Excess inventory ties up valuable capital and increases carrying costs, as Jason explains. Simultaneously, stockouts lead to missed sales opportunities and damage customer relationships, impacting both immediate revenue and long-term brand loyalty. Inventory balancing, therefore, becomes a crucial strategy for reducing costs, increasing efficiency, and ultimately, satisfying customers.
Challenges in Stock Balancing
Maintaining the optimal balance of inventory across a distributed network is a complex undertaking. Stock balancing requires a delicate interplay of forecasting, real-time visibility, and agile responsiveness. In fact, over 70% of supply chain inefficiencies originate from poor visibility into inventory levels across locations. Supply chain disruptions can exacerbate these challenges, making it even more difficult to maintain optimal inventory levels.
Lack of Real-Time Data on Inventory Levels
Operating without up-to-the-minute data on inventory quantities is akin to navigating in the dark. Delayed information leads to reactive, rather than proactive, decision-making. This makes it nearly impossible to identify and address imbalances before they escalate into costly stockouts or overstock situations. Imagine a retailer relying on weekly reports to discover a critical stockout that occurred days prior — the damage to customer satisfaction and lost sales is already done. Inventory management software can provide real-time data and improve decision-making, helping businesses maintain optimal stock levels and enhance operational efficiency.
Mastering the Art of Inventory: Unlocking Business Success with Accurate Management and Barcode Technology
READ NOW »Difficulty Forecasting Location-Specific Customer Demand
Demand is a dynamic force shaped by local market conditions, seasonal variations, and even unpredictable events. Forecasting demand at a granular, location-specific level is essential for effective stock balancing, but achieving this precision is notoriously difficult, especially when trying to meet what customers demand.
Consumer preferences can shift rapidly, and relying on historical data alone may not capture emerging trends or sudden disruptions. Maintaining optimal stock levels is a tricky balancing act made even more challenging by the intricacies of regional demand variations.
Coordination Issues Between Distribution Centers and Retail Locations
Even with perfect forecasting and real-time visibility, stock balancing can be undermined by coordination breakdowns between distribution centers and retail locations. A lack of seamless communication, logistical bottlenecks, such as transportation delays or warehouse capacity constraints, and differing priorities between these key nodes in the supply chain can create friction. This can lead to delays in replenishment, exacerbating stockouts in high-demand locations and contributing to overstock in others.
The “Double Punishment” Effect
This misalignment between different tiers of the supply chain can have cascading negative effects. Jason illustrates this with the concept of the “double punishment”. He explains how manufacturers can be hit twice: first, when wholesalers reduce their orders due to decreasing retail sales, and second, when wholesalers simultaneously draw down their existing inventory rather than placing replenishment orders. This creates a situation where manufacturers experience a sharper decline in demand than what is reflected at the retail level. This amplified reduction in orders forces manufacturers to drastically adjust production, potentially leading to layoffs, idle capacity, and increased per-unit costs.
The “double punishment” effect demonstrates how a lack of coordination and information sharing across the supply chain can exacerbate inventory imbalances and create significant challenges for upstream suppliers. This misalignment makes the already complex task of achieving optimal inventory balance even more precarious, requiring businesses to prioritize communication and collaboration across all tiers of their supply chain.
The cascading compliance model further exacerbates this effect. Large multinational corporations (MNCs) often shift the burden of monitoring and compliance to tier-one suppliers, pushing compliance onto their suppliers. This results in poor enforcement at lower levels, making it difficult to coordinate inventory needs efficiently.
Data Analytics: The Secret Ingredient to Efficient Inventory Management
READ NOW »Real-World Examples of Coordination Breakdowns
The consequences of poor coordination can be seen across industries:
- Automotive Supply Chain Disruptions: During the COVID-19 pandemic, automakers cut semiconductor orders due to an anticipated demand drop. However, when demand rebounded, chip manufacturers had already reallocated production to consumer electronics, leaving automakers unable to ramp up production. This resulted in severe shortages and months-long delays.
- Retail Inventory Failures: In 2022, major retailers such as Target and Walmart faced excess inventory crises due to misaligned demand forecasting. They ordered massive amounts of goods during pandemic-driven surges, only to see demand shift as consumer behavior normalized. With distribution centers overwhelmed, companies had to heavily discount products, resulting in billions in losses.
Legal Implications of Coordination Failures
Poor coordination can also lead to significant legal ramifications:
- Regulatory Non-Compliance: Businesses failing to align supply chain operations with sustainability laws may face fines and penalties. The cascading compliance model often fails to reach lower-tier suppliers, leading to hidden labor abuses and environmental violations.
- Contractual Liabilities: If retailers or distributors fail to meet delivery obligations due to poor coordination, they may be held liable for breach of contract. This was seen in global shipping disruptions in 2021, where firms faced lawsuits for failing to deliver goods on time.
Impact on Individuals
Coordination failures don’t just affect corporations—they have direct consequences for workers, consumers, and local economies:
- Worker Exploitation and Layoffs: When manufacturers face a sudden drop in demand due to double punishment effects, they often cut jobs to stay afloat. Lower-tier suppliers, already operating on razor-thin margins, struggle to maintain ethical labor standards.
- Price Inflation for Consumers: Poor coordination can lead to product shortages, driving up prices. For example, supply chain bottlenecks in 2021 caused household essentials and electronics to spike in cost, disproportionately affecting lower-income consumers.
Mitigating Coordination Issues
To combat these challenges, businesses must:
- Adopt a Shared Responsibility Model: Instead of shifting compliance burdens down the chain, firms should ensure direct engagement with lower-tier suppliers, improving transparency and ethical sourcing.
- Leverage Technology for Real-Time Visibility: Implementing AI-driven demand forecasting and blockchain for inventory tracking can improve synchronization between distribution centers and retail locations.
- Enhance Supplier Collaboration: Businesses should build long-term partnerships to mitigate supply chain shocks.
The “double punishment” effect demonstrates how a lack of coordination and information sharing across the supply chain can exacerbate inventory imbalances and create significant challenges for upstream suppliers. This misalignment makes the already complex task of achieving optimal inventory balance even more precarious, requiring businesses to prioritize communication and collaboration across all tiers of their supply chain.
Benefits of Effective Stock Balancing
Effective stock balancing is more than just a logistical exercise; it’s a strategic lever that can significantly impact a company’s bottom line and customer relationships. By optimizing inventory allocation, businesses can unlock a range of benefits that drive operational efficiency and enhance customer satisfaction.
- Improved Customer Satisfaction: Perhaps the most immediate benefit of effective stock balancing is the reduction of stockouts in high-demand locations. Ensuring product availability precisely when and where customers need it is paramount for maintaining satisfaction and loyalty.
- Lower Costs: Stock balancing plays a crucial role in cost reduction across several areas. Redistributing overstock from low-demand locations to high-demand areas minimizes unnecessary carrying costs associated with storing excess inventory. Furthermore, efficient stock balancing reduces the need for costly emergency replenishments, which often involve expedited shipping and premium freight rates. Effective stock balancing also improves cash flow by reducing excess inventory and avoiding stockouts, which can tie up capital and lead to lost sales.
- Increased Efficiency: Stock balancing streamlines warehouse operations and improves overall efficiency. With better inventory allocation, warehouse staff can avoid time wasted searching for misplaced or overstocked items. This optimized organization allows for quicker and more accurate order fulfillment, contributing to smoother workflows and improved productivity.
Jason believes that proactive inventory management, through techniques like safety stock optimization, can prevent stockouts without leading to excessive overstocking. By aligning inventory levels with actual demand, businesses can transform their supply chain from a source of frustration and expense into a driver of customer satisfaction and profitability.
How to Achieve Flawless Fixed Asset Tracking with Mobile Barcoding
DOWNLOAD NOW »Strategies for Successful Stock Balancing
Implementing a successful stock balancing strategy requires a multi-faceted approach that incorporates advanced analytics, real-time visibility, and flexible inventory management practices. Here are some key strategies:
- Forecasting and Analytics: Accurate demand forecasting is foundational. Leveraging predictive analytics, powered by machine learning and historical sales data, helps anticipate location-specific demand. This predictive capability is critical. For instance, retail chains use sales data, weather patterns, and other relevant factors to predict demand and proactively adjust inventory levels, preventing stockouts and overstock situations.
- Technology Integration: Integrating systems across the supply chain is crucial for real-time visibility. ERP systems, coupled with real-time tracking solutions, provide a centralized view of inventory. RFgen’s mobile data collection tools are a practical solution for real-time stock tracking, enabling dynamic reallocation decisions.
- Dynamic Reallocation: Businesses need a flexible system to adjust inventory dynamically. Adjusting based on real-time demand fluctuations ensures inventory is available where needed while minimizing carrying costs. This constant optimization helps meet customer demand by ensuring the right amount of stock is available to satisfy customer needs. Within this dynamic reallocation strategy, businesses can also incorporate elements of safety stock optimization, ensuring they have a buffer against unforeseen disruptions without tying up excessive capital.
Measuring Success in Stock Balancing
Implementing a stock balancing strategy is only the first step. To ensure its effectiveness and optimize performance over time, businesses need to continuously monitor key performance indicators (KPIs). These metrics provide quantifiable data that reveals the impact of stock balancing efforts and identifies areas for improvement.
- Service Level Improvement: A primary goal of stock balancing is to improve service levels by ensuring product availability for customers. Fill rate, the percentage of customer orders that are fulfilled completely from available inventory, is a crucial metric for measuring this improvement. Higher fill rates directly correlate to increased customer satisfaction and reduced lost sales opportunities.
- Inventory Turnover: This KPI measures how efficiently a company utilizes its inventory. It tracks how quickly inventory is sold and replenished, indicating the health of the inventory flow. A higher inventory turnover rate generally suggests efficient stock management and reduced carrying costs.
- Reduction in Stockouts and Overstock: Tracking the frequency and severity of both stockouts and overstock situations is crucial for evaluating the success of a stock balancing strategy. By comparing data before and after implementation, businesses can quantify the improvements achieved. Monitoring stock outs helps in assessing how well the strategy prevents product unavailability, thereby reducing lost sales and enhancing customer satisfaction. This data-driven approach allows companies to fine-tune their stock balancing efforts and maximize their return on investment.
Future Trends in Stock Balancing
Stock balancing, as a key component of inventory management, is being shaped by these emerging trends.
- AI and Machine Learning: Artificial intelligence (AI) and machine learning are poised to revolutionize inventory management. Predictive analytics tools powered by AI can analyze vast datasets to forecast demand with greater precision than traditional methods. This enhanced accuracy enables more proactive and optimized stock distribution. AI can also identify subtle patterns and correlations that humans might miss, further refining inventory allocation strategies.
- IoT for Real-Time Tracking: The Internet of Things (IoT) offers unprecedented visibility into inventory movement and location. IoT devices, such as RFID tags and sensors, provide real-time data on inventory levels, location, and condition. This granular visibility empowers businesses to make more informed decisions about stock balancing, enabling dynamic adjustments based on real-time insights. This enhanced tracking capability also reduces the risk of lost or misplaced inventory.
- Sustainability: Stock balancing plays a key role in reducing waste by minimizing overstock and optimizing transportation routes. By strategically positioning inventory and reducing unnecessary shipments, businesses can lower their carbon footprint and contribute to a more sustainable supply chain. This includes minimizing waste from obsolete or expired products and optimizing transportation routes to reduce fuel consumption and emissions.
Conclusion
Stock balancing plays a critical role in reducing costs by minimizing carrying costs and eliminating the need for expensive emergency replenishments. By optimizing inventory allocation, stock balancing also improves efficiency, streamlining warehouse operations and accelerating order fulfillment. Most importantly, it enables businesses to consistently meet customer demands by ensuring product availability, enhancing satisfaction, and building loyalty.
Supply chain leaders looking to optimize their operations and gain a competitive edge should embrace advanced tools and technologies. Solutions like RFgen, with its real-time tracking capabilities and seamless integration with existing ERP systems, empower businesses to implement robust stock balancing strategies.
Don’t let inefficient inventory management hold your business back. Invest in the tools and strategies needed to transform your supply chain into a driver ofc growth and profitability.
Frequently Asked Questions
What is the difference between stock balancing and inventory allocation?
While the terms are often used interchangeably, stock balancing emphasizes the dynamic and ongoing nature of inventory redistribution across locations to maintain optimal levels. Inventory allocation refers to the broader process of assigning inventory to specific orders or locations, which can be a component of a stock balancing strategy.
How often should I rebalance my stock?
The frequency of stock balancing depends on factors like product type, demand volatility, and the specific industry. Highly perishable goods or items with rapidly changing demand might require daily or weekly rebalancing, while more stable products could be adjusted monthly or quarterly. Real-time data and analytics can help determine the optimal frequency for your business.
What are the biggest obstacles to implementing effective stock balancing?
Common challenges include inaccurate forecasting, lack of real-time inventory visibility, poor communication between different locations (e.g., warehouses and retail stores), and inadequate technology integration. Overcoming these obstacles often requires investing in advanced analytics tools, real-time tracking systems, and fostering better collaboration across the supply chain.
Is stock balancing only relevant for large businesses with complex supply chains?
While the complexities might be greater for larger organizations, the principles of stock balancing are relevant for businesses of all sizes. Even small businesses with a single warehouse and multiple retail locations can benefit from strategically distributing inventory to optimize availability and minimize costs.
How can I get started with stock balancing?
Begin by assessing your current inventory management practices and identifying areas for improvement. Consider investing in technology solutions that provide real-time visibility and enable dynamic inventory allocation. Start with a pilot program in a specific region or product category to test and refine your strategy before implementing it across the entire supply chain. Consult with supply chain experts to tailor a stock balancing approach that aligns with your specific business needs and goals.