The Top Inventory Management KPIs Manufacturers Should Be Tracking
- Data Collection
- Inventory/Warehouse
- Manufacturing
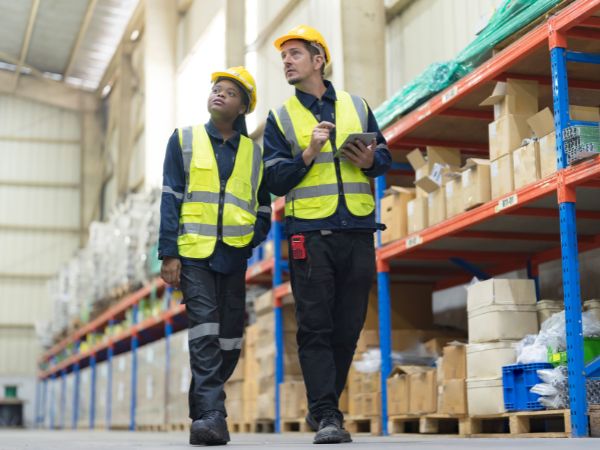
If data is king, accurate and accessible data is emperor.
Without solid data, businesses fly blind, unable to measure what is working and what is not. Metrics provide the benchmarks needed to gauge performance.
According to the Aberdeen Group, organizations that analyze their KPIs outperform their competitors, gaining 10% faster decision-making time and 9% increased profitability.
But tracking irrelevant data isn’t helpful, businesses must monitor the right key performance indicators (metrics tied to specific business goals) to get the most out of their efforts and outpace their competitors.
What are key performance indicators? What are inventory management KPIs? Why do they matter?
To understand the best KPIs to track for optimal inventory management, we’ll explore those questions and more, so you can take back control of your operations and improve decision-making.
What are Key Performance Indicators for Inventory Management?
Key performance indicators are metrics businesses track to measure performance. Unlike other metrics, KPIs are directly relevant to your business’s goals.
KPIs are measurable values that indicate how well a company is achieving business outcomes and reaching targets. Every effective KPI must be relevant, measurable, actionable, and time-bound.
When it comes to KPIs in inventory management, it refers to metrics that help you monitor and make decisions about your stock. They offer information on storage, turnover, process success, costs, and movements of a company’s stock matter most.
Why are KPIs important for Inventory Management
You can’t improve your business if you don’t know how it’s performing. That’s why monitoring inventory management KPIs is paramount.
For instance, if a worker using manual processes miscounts stock items, and enters outdated data into an ERP system, this can lead to over-purchasing or stockouts and force a customer or business to be put on back-order.
That’s where KPIs enter. With effective KPI tracking for inventory management, warehouse managers can get ahead of productivity bottlenecks, and inefficiencies that threaten to disrupt production and hurt profitability.
Moreover, managers can benchmark current performance against their industry peers to find improvement areas.
Additionally, investing in mobile inventory software with a built-in KPI tracking module can help managers track the inbound, outbound, and employee KPIs without the large investment into a WMS or a third-party tool, often having more modules and features than enterprises need.
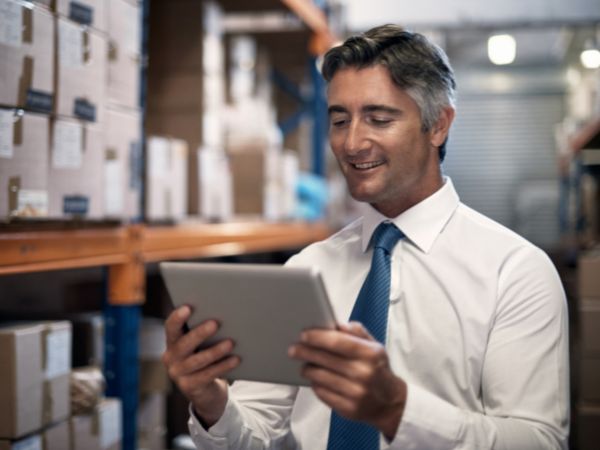
An Intelligent Alternative to WMS: Gaining Real-Time Inventory Visibility Without the Complexity
READ NOW »Time to Receive
Time to receive calculates the average time it takes workers to receive and process new shipments.
With this KPI, warehouse managers can identify inefficiencies in the receiving process, and make the necessary changes to enhance efficiency, which in turn, affects other warehouse processes.
Formula: Time to Receive = time for stock validation + time to add stock to records + time to prep stock for storage
Put Away Time
Put away time measures how long it takes workers to transport goods from the receiving area to the correct storage area on shelves or warehouse racks.
Monitoring this metric can help managers identify areas of inefficiency in this process and how they might improve productivity.
Formula: Put Away Time = total time to stow received stock
Putaway Accuracy
Putaway Accuracy measures the percentage of items workers place in their correct bins or locations after receiving them.
Managers must monitor putaway accuracy to prevent or minimize picking errors and enhance order fulfillment.
Formula: Putaway Accuracy = (total putaways / total correct putaways) × 100
Order Picking Accuracy
Order Picking Accuracy measures how many items were accurately picked out of the total items picked.
Monitoring order-picking accuracy helps reduce costs. By tracking this KPI, warehouse managers can also identify errors in the picking process and implement corrective measures such as better training, improved picking systems, or enhanced automation solutions to ensure accuracy.
Formula: Order Picking Accuracy Rate = orders picked accurately / total number of orders
Order Picking Time
Order Picking Time calculates the average time taken to pick items for orders, which works to assess the efficiency of the picking process.
Managers should strive to reduce order picking time to achieve faster order fulfillment and improved customer satisfaction.
Additionally monitoring this KPI can help managers evaluate the performance of their picking strategies and technologies, making necessary adjustments.
Picking can be prolonged when workers have to wander around the warehouse because they aren’t sure where items are. To solve this, many managers are investing in mobile inventory software with improved UI/UX designs that simplify the process for workers, reducing wasted time, and enhancing productivity.
Formula: Order Picking Time = total time spent on picking / total number of orders picked
Inventory Accuracy
Inventory accuracy compares the real-life inventory levels on the shelves and in storage to recorded levels, measuring the accuracy of a company’s inventory data and system.
Without accurate data, manufacturers struggle to deliver on customer expectations. For instance, if a manufacturer accepts an order of 100 parts, but when workers go to fulfill the order and discover they are 20 parts short, their reliability is severely impacted.
Thus, accurate inventory records give manufacturers the operational efficiency they need to keep their customers happy.
To improve this metric, many manufacturers across industries are going from paper-based processes to mobile automation. With mobile data collection, workers gain real-time entry and updates of inventory data and avoid the data gaps inherent to manual data entry.
Formula: Inventory Accuracy = (counted items / items in records) x 100
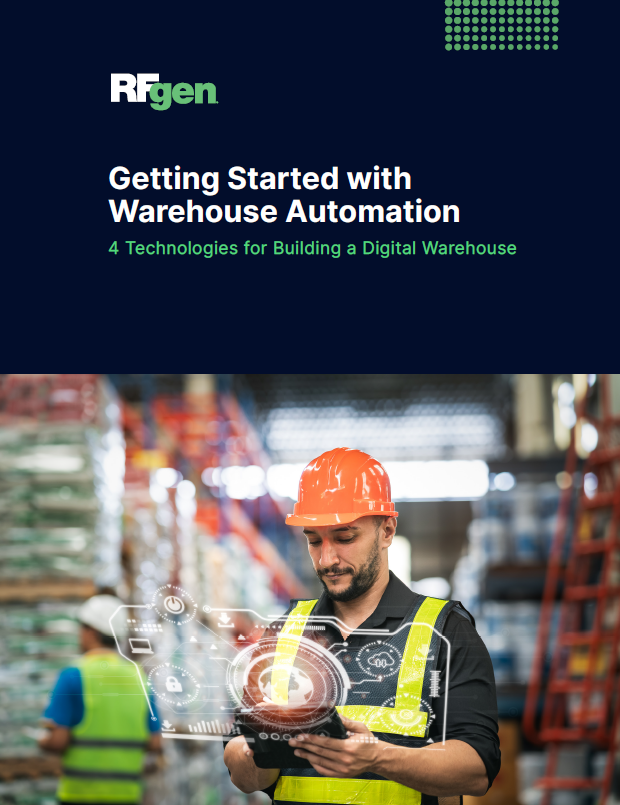
Getting Started with Warehouse Automation
GET THE GUIDE »Inventory Write-Off Rate
Inventory write-off rate tracks the percentage of food inventory that gets written off because of
- spoilage
- damage, or
- theft.
A high write-off rate typically indicates signs of excess inventory or poor inventory management. This can result in compliance failure and a significant financial loss for businesses.
Keeping an eye on this KPI helps you better allocate inventory space, allocate resources and keep goods from becoming unsellable in the first place to reduce waste. spot issues early and cut down on waste
Formula: Inventory Write-Off Rate = (written-off inventory / total inventory) x 100
Order Lead Time
Order lead time measures the time between the customer’s order and order fulfillment.
Minimizing lead time leads to faster turnover. and when a company can sell and replace its inventory more quickly, it reduces the amount of time capital is tied up in unsold goods, increasing cash flow.
Additionally, manufacturers can reduce lead time by automating manual processes. For example, mobile inventory technology Can automate data collection and data entry to reduce errors and improve labor productivity.
Formula: Order Lead Time = receipt date – order placement date
Order Cycle Time
Order cycle time measures the average time taken to ship out an order from the time it was placed.
With this, managers can monitor their fulfillment process efficiency. Greater efficiency translates to better business agility.
Additionally, long order cycles can lead to longer delivery times, which results in unhappy customers. This KPI can help managers pinpoint areas where they can improve warehouse flow to optimize inventory and order management.
An effective strategy for improving order cycle times is with mobile. This technology can help optimize order management by automating processes like production orders, issuing materials, and tracking component scrap.
Formula: Order Cycle Time = (delivery date – order date) / total shipped orders
Cycle Count Accuracy
Cycle count accuracy measures the accuracy of inventory levels based on periodic cycle counts compared to recorded inventory. Without this metric, companies can experience unexpected stock-outs.
Regular cycle counts in warehouses help managers catch discrepancies early on to maintain accuracy and ensure the inventory records in their ERP system match actual stock levels.
Tracking this metric directly improves decision-making and overall efficiency in inventory management.
Moreover, integrating mobile technology into cycle counts can improve labor utilization, turning a perceived time-waster into a true value-add.
Formula: Cycle Count Accuracy = (accurate cycle counts / total cycle counts) x 100
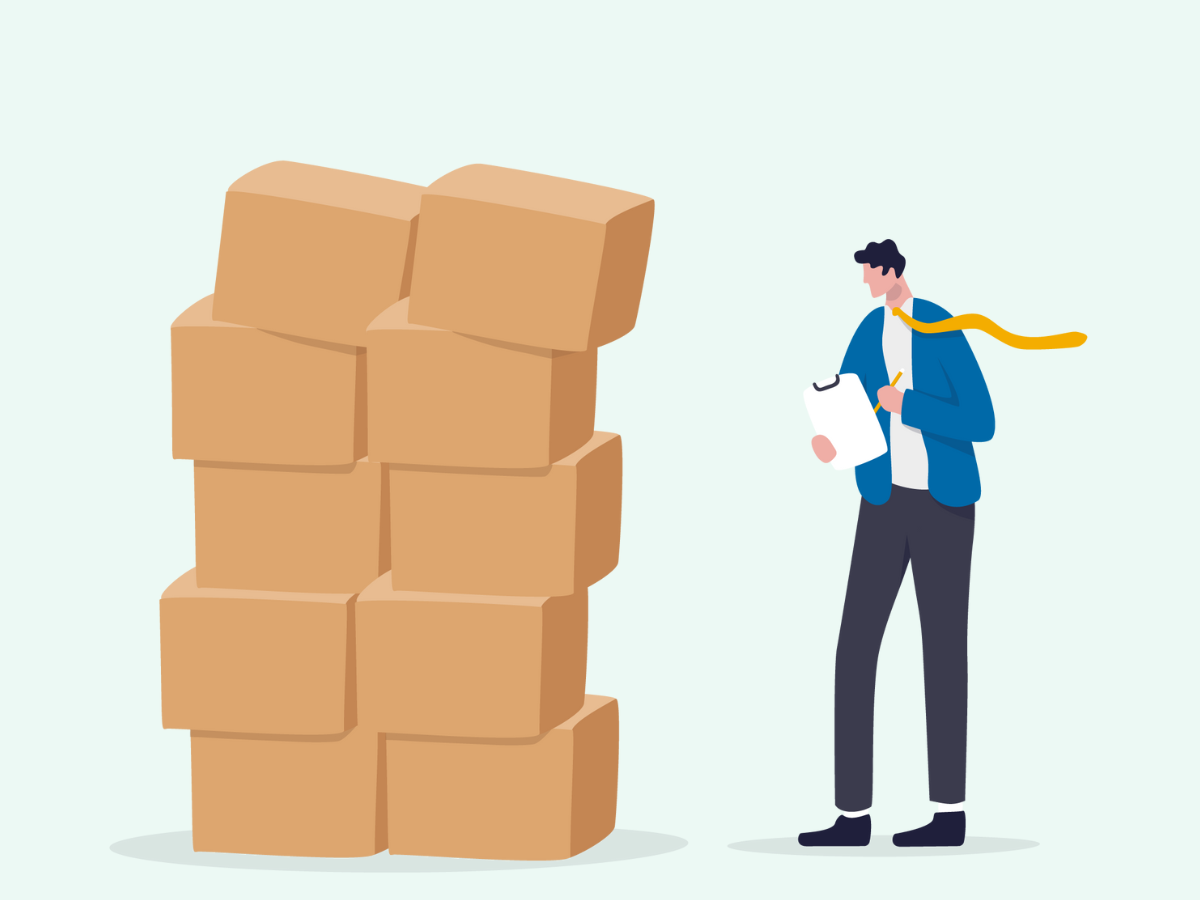
Why You Should Automate Your Cycle Counting
DOWNLOAD NOW »A Case Study: CPG Manufacturer Reduced Picking Time by 70% With Mobile Technology
Consumer packaged goods manufacturer, Big Dee’s, has been providing equine supplies and equipment for individual horse owners, businesses, and clinics across the United States.
Relying on manual processes for their 103,000 sq. ft. warehouse, workers would handwrite notes and then hand key that information into their system.
Recognizing this was slowing operations, Big Dee’s was ready to digitize manual processes to achieve the traceability and accuracy necessary to fulfill customer orders more quickly.
RFgen gave Big Dee’s access to real-time KPI tracking so they could benchmark their performance against other retail manufacturers and make necessary improvements.
As a result, they reduced pick and pack time by 70% and were able to guarantee same-day shipping for orders placed at a certain time of day— A business model most of their competitors could not offer.
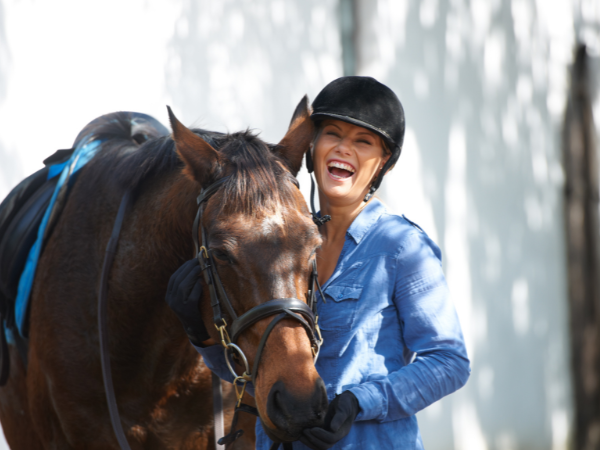
Retailer leverages RFgen to reduce picking time by 70%
READ THE FULL STORY »How Mobile Barcoding Can Help You Track Inventory Management KPIs
Without closely monitoring KPIs, businesses can’t accurately benchmark their performance against their peers. Unaware of inefficiencies and bottlenecks, costs will rise, productivity will fall, and chances of outpacing their competitors will become obsolete.
With a mobile solution like RFgen, monitoring KPIs can be easier. Our solution offers a KPI tracking module that allows managers to track and report performance for warehouse and manufacturing operations. Managers can track inventory processes, inbound processes, outbound processes, as well as employee tasks — all to set performance benchmarks and future goals.
With this KPI tracking module, managers can also visualize their data on live, interactive dashboards, for visual and shareable feedback in real time.
Accurate decision-making requires accurate data. For this reason, investing in mobile inventory control software like RFgen, can enhance your KPI tracking for faster decision-making time and increased profitability.
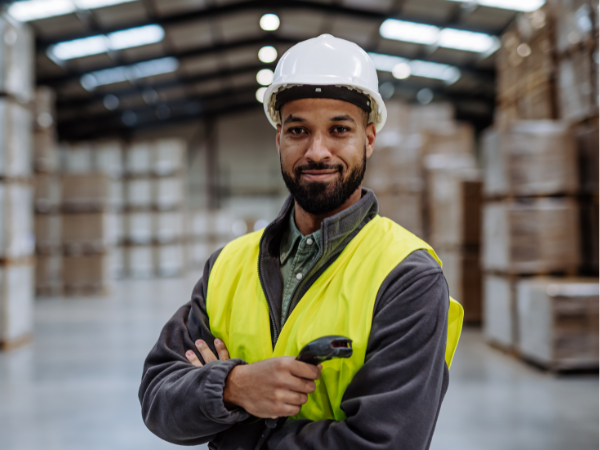