Overview:
- A Short History of Voice
- Voice Technology in the Supply Chain
- Real Results
- How Voice Works
- What is the Bottom Line?
- Frequently Asked Questions
The questions in the minds of today’s information technology (IT) executives run in an endlessly agonizing loop:
- Do I have the right infrastructure in place?
- Are my servers and databases and applications doing what they need to do?
- How do I separate valuable new technology from all the junk?
- Is my system secure?
These are tough questions. But as any business-minded IT practitioner knows, these concerns aren’t about technology on its own. They are about technology as it relates to corporate strategy and the bottom line.
The biggest question that keeps the strategic IT executive awake at night is: How can I use technology to boost productivity, make the supply chain more efficient, and maximize ROI?
Many are finding the answer to be voice-enabling their warehouse.
The use of voice picking solutions in the warehouse is gaining momentum. Hands-free, eyes-free task execution at high speed and volume for key inventory processes offers great promise. Many organizations are seeing immediate value from the technology. Today, hundreds of thousands of end-users use Vocollect products with great success.
For some IT thought leaders, voice has become a catalyst for re-engineering warehouse best practices and technology systems.
A Short History of Voice
Voice recognition and speech technology began deep inside the workshops of Bell Laboratories during WWII, where researchers believed in a radical new idea: that one day, machines would be able to recognize and respond to human voice commands.
Gradually, other researchers outside of Bell Labs caught wind of the idea and they, too, shared the excitement about the advances possible if computers could talk and be spoken to. These researchers toiled away silently for years. Then, in the late 1980s, voice recognition and speech technology began to grow into their potential.
Today, interactive voice technologies are everywhere, from mobile phones to virtual assistants like Amazon’s Alexa. In the business world, banks use voice to help consumers complete transactions over the phone. Even airlines and weather bureaus use automated voice systems to share information.
So bringing voice-directed to the warehouse is a logical next step.
Voice Technology in the Supply Chain
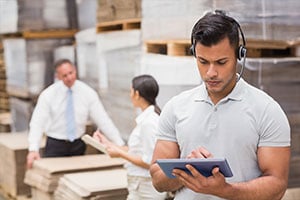
Voice-directed work has been making significant inroads into the global supply chain. Here, solutions like voice picking are freeing up workers and allowing them to be safer, more accurate, and more productive.
For inventory handling in particular, voice alleviates the strenuous multitasking that is typical of work in the distribution center (DC) or shop floor. Voice enables companies to sharply reduce the time it takes for new and seasonal workers to become fully functional in their role.
The benefits of more efficient receiving, put-away, cycle counting, replenishment, and picking have led many major grocery distributors to become early adopters. Today, more than three quarters of the top 75 grocers in the U.S. are Vocollect Voice customers.
Warehouse voice technology’s ease of use has led to its adoption in manufacturing, retail, third-party logistics (3PL), and healthcare. Many household names now use the technology, including Office Depot, Pep Boys, and Pepsi Bottling Group in North America; and Norauto, Easydis, and Primafrost in Europe.
Real Results
In one real-world instance, Smith Drug Company, a wholesale pharmaceutical distributor based in Spartanburg, South Carolina, installed Vocollect Voice. They experienced an immediate 20% jump in productivity. Delivery accuracy soared to 99.99%. Voice technology also eliminated the need for overtime and long training periods for new workers.
Pep Boys offers another compelling use case. As one of America’s leading automotive aftermarket retail and service chains, its 593 stores in 36 states deliver more than 75 million items a year. Within 6 months of deploying voice into 5 DCs, Pep Boys documented a 21% increase in worker productivity while accuracy rose from 98.68% to 99.46%. Training time was cut in half. The company expected to save $3 million annually as a result.
How Voice Works
During a typical day in the warehouse, work assignments are generated and then distributed to staff via paper printouts or technologies like pick-to-light systems. But these methods can be labor-intensive, error-prone, and can’t be scaled.
But in a voice-enabled operation, the process is much simpler and more accurate. Voice-directed work takes the intuitive human approach to communication—two-way dialogue—and literally talks people through their daily tasks.
Here’s how it works:
- Employee assignment tasks (put-away, order selection, etc.) are generated by the system of record, such as an ERP or WMS.
- Assignments are sent wirelessly via RF to a lightweight, battery-powered mobile computer worn by the employee.
- Tasks are converted to discrete verbal commands by the wearable computer, which the employee hears through a lightweight headset. The instructions direct the employee to an aisle/section and slot location.
- Once there, the employee confirms location arrival and completes the task by speaking into the headset.
- Voice recognition software on the wearable computer translates the spoken response into data and sends that data back to the system of record.
- The system of record issues the next appropriate command and the process repeats itself.
ALSO READ: Speaker-dependent vs speaker-independent software »
What is the Bottom Line?
By replacing time-consuming, inaccurate inventory handling with more efficient voice-directed systems, companies experience:
Increased Productivity
Voice-directed work generates productivity gains of 50% or more.
Voice increases productivity by making workers more efficient. When using paper labels, archaic barcode scanners, and systems that need to be deactivated, an employee’s attention is frequently being diverted and productivity lessened. Because voice is a hands-free/eyes-free operation, workers can devote total attention to the task at hand, cutting out unproductive time and mistakes. And because voice accommodates multiple languages and training time takes just a few hours, onboarding is short and simple.
Productivity gains from these efficiencies can easily reach 50% or more, translating to hundreds of thousands of dollars in annual savings.
Improved Accuracy
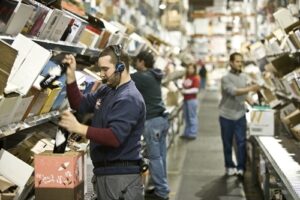
Voice enforces order accuracy through the use of random check digits. The check digits are placed directly at the product’s location and must be read when the worker is at that location. Because the voice system won’t allow the worker to continue unless he or she reads the appropriate digits, accuracy is guaranteed nearly 100% of the time.
Enhanced Worker Safety
Because the employees’ hands are free and their eyes are not distracted by holding a device or paper printout, they can focus on the critical activities going on around them. The ability for employees to keep their heads up makes them much more aware of potential safety issues in their surroundings.
Reduced Turnover
Voice allows workers to perform at higher levels with reduced effort. This means they take more pride and ownership in their work. A longer-tenured warehouse workforce reduces the cost and time waste of turnover and excessive new-hire training.
Frequently Asked Questions
Is voice difficult to implement?
No. Voice-directed work has a tremendous impact and is quite easy to install. Installation time takes only one day while training only takes a few hours.
It’s important to work with a supplier that has a strong track record and extensive understanding of job functions, operating environments, and business realities of inventory management.
Is the technology mature?
Voice-directed work has been successfully deployed by both large and small companies for many decades. The leading voice-directed work supplier, Vocollect, has hundreds of thousands of users in over 30 countries and 6 continents.
How does the voice connect to my system of record?
A voice deployment requires special software to enable the two-way dialogue required to give assignments and confirm that tasks are completed.
Many major software providers of ERP systems, mobile barcoding, and WMS already have the necessary interfaces in place. The best voice systems are designed to integrate directly with popular commercial systems. A direct interface can even be implemented for home-grown legacy systems.
What does the IT infrastructure framework look like?
Voice-directed systems interface with our existing infrastructure, either via a direct communications interface to the system of record, or via middleware. Hardware devices leverage existing wireless networks. Integration is straightforward and IT infrastructure impact is minimal.
What security standards are supported by voice?
The best voice suppliers support all standards, such as WPA-Enterprise.
What device management tools are necessary?
Since efficient voice systems must manage voice-related configuration information beyond the capabilities of common mobile device management software, full-featured voice systems have device management functionality built in as an integral part of the system.
What is the burden on IT?
Once the technical interfaces are completed and the system is up and running, the requirements on IT will be minimal. Maintenance overhead is negligible. Experienced suppliers know how to take the lead on designing, developing, testing, project managing, and implementing voice systems.
Can voice be deployed in distributed IT environments?
Yes. As wide-area networks (WAN) become faster, centralized systems are becoming more popular where only the voice terminal and headsets are in use at the facility while the ERP remains centrally located. Experienced voice providers can accommodate this scenario as well as create systems for use in distributed environments.
What does the implementation process look like?
Naturally, the installation process will vary depending on the voice supplier selected. You’ll want to look for a company whose implementation process has been finely-tuned, based on hundreds of successful installations. Ideally, a voice supplier should work with you to accomplish the following steps to ensure a successful installation.
Voice: An Important Strategic Weapon
With its multi-decade proven track record of achieving productivity, performance, and high-yield ROI, voice is a low-risk investment. Senior IT executives making large-scale technology purchases for their companies can rely on knowledgeable, experienced solution providers to implement voice-directed work successfully.
By partnering with an established voice supplier, technology buyers can help voice-directed solutions become one of the most important strategic weapons in a company’s supply chain.