Overview
- Too many utility companies lose track of valuable inventory and assets in the field.
- By mobilizing manual inventory processes, utilities gain crucial oversight of inventory—even in disconnected environments.
- Key benefits of mobile inventory management for utilities include: continuous ERP-connectivity in the field, a 40% increase in technician productivity, an 80% reduction in non-compliance fines and safety violations, and a 50% reduction in maintenance backlogs.
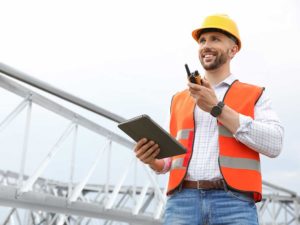
Utility companies provide foundational infrastructure for our everyday lives. But until something goes wrong, as with recent wildfires in California and energy shortages in Texas, most people don’t realize their far-reaching impact.
That’s why utilities must take a proactive approach to all facets of everyday operational oversight. This includes choosing the best inventory management solution that drives inventory visibility and efficiency.
If you currently use manual or outdated inventory processes, now is the time to mobilize and digitize your solution.
Here’s why:
You Need to Collect Data in the Field
You need to track high value inventory in the field across large coverage areas. Delivery, transport, and large spare parts warehouses further complicate effective inventory management.
If you use manual inventory processes, your workers and technicians lose visibility of your inventory as it moves from site A to site B. With no way to transact inventory against your ERP in real-time, even expensive inventory items and assets can be lost or misplaced.
Instead, mobile inventory solutions equipped with offline data collection connect field engineers and technicians to your ERP—no matter the location.
This lets your workers collect accurate inventory data in real-time to reduce lost or missing inventory.
DOWNLOAD: Must-have Benefits of Mobile Digital Inspections »
You Need Mobile Work Order Management
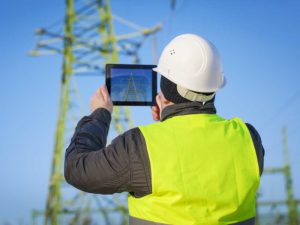
Mobile Work Order Management (WOM) replaces paper in the field with mobile apps. Technicians simply follow step-by-step guided instructions to complete inspections and repairs directly from a mobile device. This digital process reduces errors caused by a lag in reporting. And boosts technician productivity by 40%.
Since you know your inventory records are timely and accurate, you can be more confident in your regulatory compliance as well. In fact, mobile inventory management and WOM for utilities can reduce non-compliance fines and safety violations by 80%.
LEARN MORE: Mobile MRO Solutions »
You Need More Effective Utility Asset Management
Utility companies also need to prioritize Enterprise Asset Management, or EAM. Managing spread out, disorganized warehouses is inefficient, costly, and unsustainable.
Mobile inventory solutions let you monitor essential utility assets in real-time, from anywhere. With mobility, you can reduce your maintenance backlog by 50% while also:
- Reducing last-minute shipping costs for out-of-stock inventory
- Minimizing unplanned downtime
- Maximizing equipment life
Utility Management Solutions in Action
A large California utility company manages a series of small warehouses across a 50,000 square mile radius. Its employees had been using paper processes to track expensive assets and inventory in the field. Inventory would be loaded into a truck and then disappear from the tracking system until delivery. Sometimes, this meant inventory would go missing or be lost.
After integrating a mobile inventory solution, the company can now track all inventory in real time and in the field. When a major capital tool went missing, the manager could easily look-up the date, time, pick-up location, drop-off location, and employee sign-in/out to track it down quickly.
Mobilizing Utility Inventory in the Field
With consumer and regulatory oversight intensifying, utility companies can’t afford to lose inventory and assets in the field.
Mobilizing and automating inventory with an effective utility inventory management solution provides the oversight needed to stay ahead of future challenges.
Additional Resources
Blog: Power Problems in Thailand Highlight Need for Supply Chain Software »
Blog: Top RFgen Case Studies for SAP Mobile Barcoding Software »