Your Guide to Understanding & Minimizing Inventory Costs (with Formula)
- Digital Transformation
- Inventory/Warehouse
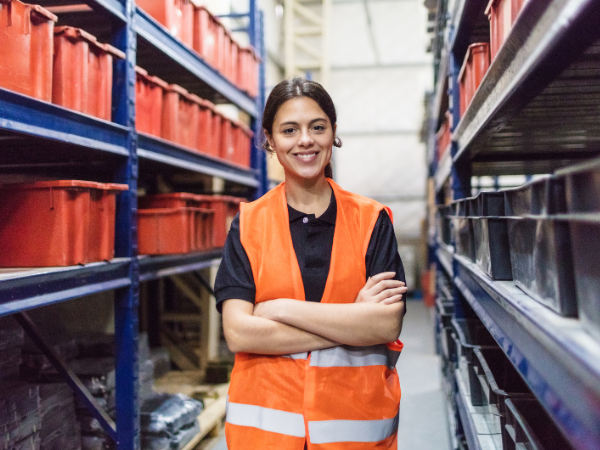
Managing inventory costs is a constant struggle. Between rising costs for materials and endemic labor shortfalls in the warehouse, many supply chain professionals may feel trapped in an endless cycle of shrinking profit margins.
Managing inventory costs is important because high inventory costs can erode the bottom line. On the other hand, optimized inventory levels can enhance it.
herefore, a strategic approach to managing these costs through efficient warehouse organization is not just beneficial but essential for maintaining a competitive edge and financial health.
With the aid of automation technology, businesses are able to streamline inventory management and cost control. The high levels of efficiency created this way help minimize inventory costs.
But we’re getting ahead of ourselves.
To better understand how organizations like yours can better manage inventory costs, let’s start at the beginning—
The Basics of Inventory Costs
Inventory costs encapsulate all expenses incurred throughout the inventory lifecycle. This includes acquiring, storing, and managing stock.
Money spent on these areas influences your business’s operational budget and profitability. Therefore, the goal is to optimize cost to optimize profits and catalyze growth.
To start with, inventory costs go beyond the initial purchase price of goods. Hidden costs may accumulate after purchase if not meticulously monitored and managed.
Even the initial purchase of inventory triggers a cascade of additional expenses, like shipping, handling, taxes, and so on.
Next is the cost of storing the inventory. Expenses like utilities, security, insurance, and other warehousing line items may be involved.
In addition, inventory is associated with carrying costs. Unsold stock can tie up capital that could otherwise be invested in revenue or growth opportunities.
And then there are administrative costs for inventory management and accounting, which are easily overlooked but not insignificant.
Inventory costs are incurred in four main areas:
- Ordering Costs
- Carrying Costs
- Stockout Costs
- Inventory Management Costs
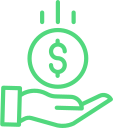
How to Reduce Inventory Costs & Increase Profit Margins
LEARN MORE »The 4 Pillars of Inventory Costs
1. Ordering Costs
Ordering costs represent the expenses associated with replenishing stock. In addition to the purchase price, secondary costs can include:
- Shipping fees
- Payment processing
- Handling labor
- Administrative costs
- Management of supplier relationships
Think of it like this: Every time your business places an order with the supplier, a series of actions unfold, starting from generating purchase orders to receiving and inspecting the goods upon arrival.
From there, the goods are received and put away in the warehouse.
Some fees are more obvious, like shipping charges. Others are less visible, such as the cost of administrative tasks for procurement and order management.
Recognizing and understanding these costs can help you improve inventory management and reduce overhead.
To gain even more order efficiency, technologies like mobile barcoding can help automate manual tasks. The efficiencies gained by eliminating extra steps and human error directly improve the costs of inventory management.
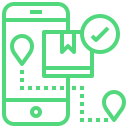
Mobile Barcoding: Automate Manual Processes and Go Paperless
DOWNLOAD NOW »2. Carrying Costs
Carrying costs, or the cost of holding inventory, remain a constant concern in the warehouse.
Holding onto inventory incurs multiple indirect expenses, from rent or mortgage payments for storage space to utilities, insurance, and personnel.
These costs accumulate over time, affecting the financial health of a business.
Inefficient inventory control often leads to a buildup of excessive overstock. Whether your business is attempting to stockpile “just in case” materials to avoid a shortage or your operation doesn’t have the visibility it needs to streamline stock levels, overstocking detracts from profits.
If you’re in an industry like food and beverage or electronics manufacturing, perishable goods add another layer of complexity. Spoilage or obsolescence create losses. Therefore, these products must be managed with meticulous care.
Balance must be maintained between minimizing the resources tied up in inventory and reducing the risk of stock obsolescence.
One way to reduce carrying costs is through a mobile warehouse solution. By leveraging real-time barcode scanning connected to the ERP system, transactions are instantly recorded, enhancing visibility, traceability, and throughput. All of these factors help reduce carrying costs.
In addition, mobile technology plays an important role in enabling accurate demand forecasting, thus allowing for more precise inventory control and lower carrying costs.
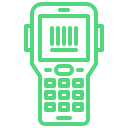
The Comprehensive Guide to Mobile Inventory Systems
GO NOW »3. Stockout Costs
Stockout costs emerge when businesses fail to meet demand due to inadequate inventory levels. Warehouse managers dread stockouts.
Stockouts cause disruptions or delays in customer orders and production lines, and lead to missed sales opportunities.
Ultimately, these issues can have a long-term impact on customer satisfaction—or dissatisfaction, as the case may be. Loss of customer loyalty and brand reputation are difficult to calculate, but real nonetheless.
Not only do dissatisfied customers tend to stop buying, they often go to competitors, damaging your bottom line twofold.
To avoid stockouts, your organization must take a proactive approach to inventory management. Technology is virtually the only way to do this effectively.
In this case, mobile inventory solutions can help optimize stock levels, automate re-order points and replenishment, and boost the accuracy of demand forecasting.
Embracing technology for real-time inventory tracking and analytics equips businesses with the insights they need to maintain resilience in the face of demand fluctuations and the unexpected.
4. Inventory Management Costs
Lastly, the handling of items themselves affects inventory costs. For the warehouses using manual processes or limited automation, these costs can be significant.
Not only is inventory frequently misplaced, but it can also be re-ordered (and overstocked) due to lack of visibility or timely information in the ERP system.
Labor expenses factor heavily into inventory costs as well. Consider the following:
- Accuracy of inventory, picking, and orders
- Speed of task completion
- Time spent searching for inventory
- Error corrections and re-work
- Training time for new or seasonal workers
Again, mobile technology provides transformative benefits. By automating manual processes and replacing dated practices with real-time digital inventory, your warehouse can significantly improve accuracy, speed, and training time.
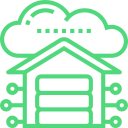
Getting Started with Warehouse Automation
GET THE GUIDE »Other Key Factors Affecting Inventory Costs
Operational Efficiency
As with inventory management, operational efficiency ultimately influences total inventory costs as well.
In short, operational efficiency determines how well your business can manage its inventory to meet demand without incurring unnecessary expenses.
This means warehouse management procedures affect the bottom line. Ideally, a company will want to make its warehouse as efficient as possible.
There are several important areas to look at:
- Time spent on each inventory stage (receiving, cycle counting, picking, etc.)
- Labor productivity
- Ability to effectively forecast demand
- Amount of waste
- Level of automation
- Hidden bottlenecks
Technological advancements in warehouse automation are helping businesses to streamline inventory activities and lower overhead costs.
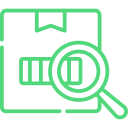
3 Hidden Costs of Manual Processes
READ NOW »Implementing a mobile inventory management solution is one possibility. By connecting an enterprise mobility solution to your ERP system, you can accelerate operations into real time with reliable data, visibility, and analytics capable of driving more effective decision-making.
In addition, a mobile solution with a consumer-like UI/UX enables workers to learn their jobs in 80% less time. Faster and more qualitative training improves handling and storage practices, reducing losses, and further lowering carrying costs.
External Factors
Although harder to predict, external factors play a role in inventory costs, too. External factors can be anything from market trends, seasonal or fluctuating demand, global economic conditions, localized disruptions from natural disasters, and so on.
Depending on your business, these factors may impact your inventory costs.
For instance, an unexpected surge in demand can lead to rapid stock depletion, necessitating urgent restocking at potentially higher costs.
In another example, a sudden market downturn might result in overstock, increasing carrying costs.
Additionally, supply chain disruptions from natural disasters, political instability, or pandemics can lead to delays and inflated costs.
For these reasons, businesses must rely on technology and operational health to stay agile. Having reliable data that’s always up to date is key. Only then can decisions be made quickly and effectively to pivot when faced with uncertainty or changing conditions.
Strategies for Managing and Reducing Inventory Costs
Inventory Optimization Techniques
The most important thing you can do to reduce inventory costs is to optimize your inventory control. This way, you can align your stock levels as closely as possible with customer demand.
Many techniques abound. Some strategies include:
- ABC analysis, which categorizes inventory based on its importance, prioritizes faster moving inventory and resources.
- Economic Order Quantity (EOQ) is a model that determines the optimal order size to minimize both ordering and carrying costs.
- Just-in-time (JIT) inventory system reduces inventory levels by arranging for goods to arrive only as they are needed.
Implementing any of these techniques requires precise monitoring and forecasting. The only way to do that in today’s fast-moving supply chain is through the use of technologies like mobile data collection.
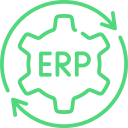
RFgen Mobile Data Collection Solutions for Your ERP
LEARN MORE »Leveraging Technology for Inventory Management
Warehouse technology is a game-changer for managing inventory costs efficiently. In addition to an ERP that enables digital records, implementing mobile software brings the power of that system to point-of-work.
A mobile solution like RFgen transforms obsolete inventory control practices. With built-in manufacturing traceability solutions, asset tracking, offline inventory management, and more, every area of inventory can be optimized, from stock levels to turnover rates and costs.
Investing in RFID tags and barcode scanners can also improve throughput and reduce errors, further improving cost control.
As a cloud-ready solution, RFgen offers unparalleled flexibility and scalability when optimizing your warehouse and inventory workflows. This enables you to reduce overhead costs associated with ordering, carrying, stocking, receiving, picking, production, and more.
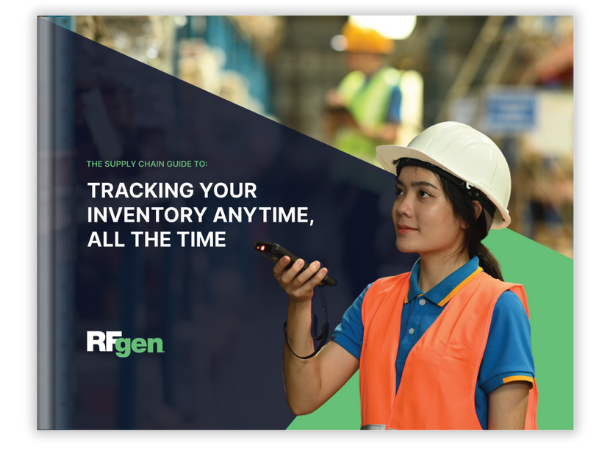
Leverage RFgen to Track Your Inventory Anytime, All the Time
LEARN MORE »Calculating and Tracking Inventory Costs
If you’re wondering how to calculate inventory costs, look no further. The basic inventory cost formula is:
Inventory Cost = (Beginning Inventory + Inventory Purchases) – Ending Inventory
This formula calculates the total cost of inventory over a specific period. Knowing this provides insight into how inventory management affects profitability.
If you want a more accurate result, include cost modifications from the four pillars mentioned above as well as the impact of operational efficiency and external factors.
Because the calculations get pretty complicated, you may wish to turn to a free online inventory cost calculator that can automate some of the manual work.
In larger organizations, calculating inventory costs can be especially complex. When evaluating new inventory technologies, consider reaching out to potential technology vendors who can help you calculate the cost savings associated with implementing the new solution.
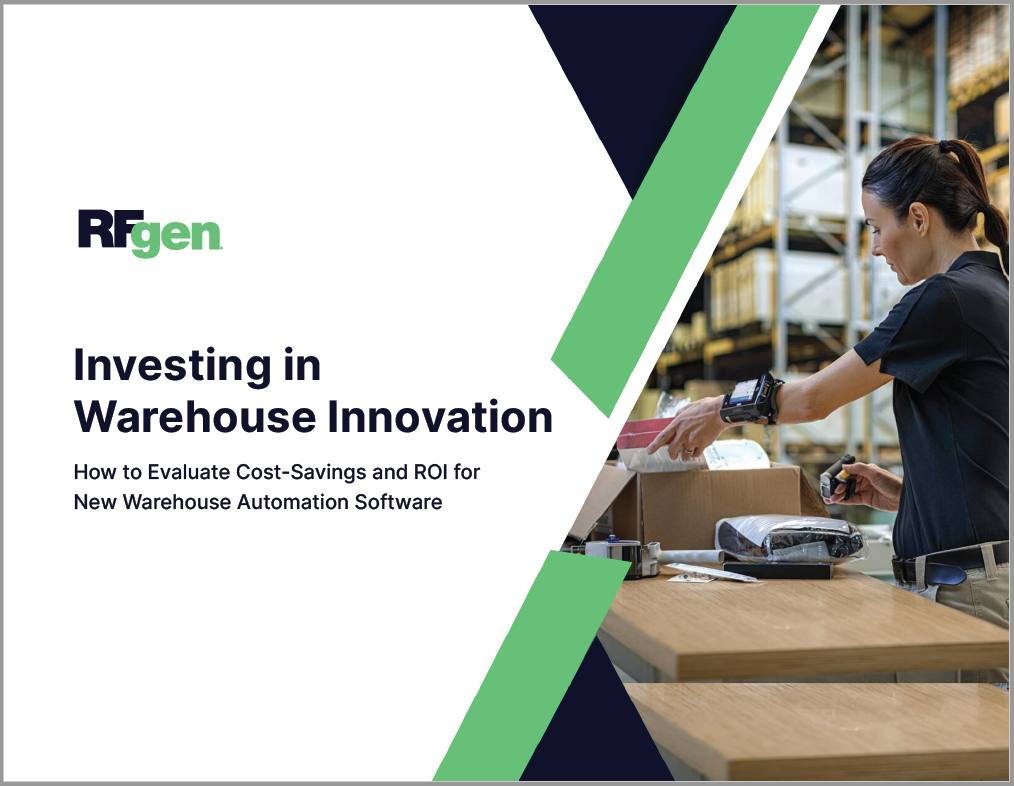
Investing in Warehouse Innovation: Calculating ROI
DOWNLOAD NOW »Maximizing Profits Through Strategic Inventory Management
For businesses looking to maintain a competitive edge and reduce overhead, minimizing inventory costs is a necessity. Understanding the factors that contribute to inventory costs and how to more effectively manage stock with technology will help you optimize cost control. With the aid of mobile technology, you can drive scalable, sustainable growth in a fast-paced world and emerge more resilient, agile, and profitable.