Case study
National Rail Operator
National Rail Operator manages equipment, plant maintenance, and parts inventory with an automated data collection solution for Oracle’s JD Edwards.
Results
- Mobilized inventory transactions and inquiries.
- Eliminated time-consuming paperwork.
- Complied with regulations that require the serialization of every part on each train.
- Optimized inventory cycle counting, even in locations without Wi-Fi connectivity.
Challenge
The company uses Oracle’s JD Edwards EnterpriseOne to track spare parts inventory and maintenance activities. To update the system, they were using a paper-based manual process where information was collected and then data was entered into JD Edwards. This not only made inventory management difficult, but it was inefficient and error-prone. It also impacted productivity since nighttime personnel who needed to issue parts for work orders did not have after-hours access to the JD Edwards system.
Furthermore, the company procured spare parts and other inventory items from suppliers via purchase orders in JD Edwards. A requirement under national safety regulations mandated the collection and tracking of serial numbers on train parts. Compliance with this government mandate required more steps in the company’s manual receiving process.
To address these issues, the company began looking for an automated data collection software solution that could integrate with its JD Edwards system and extend JD Edwards transactions onto wireless RF devices in the shop and store room, thus enabling the company to improve receiving parts issuance, and inventory management. Using mobile devices with barcode scanning would also make it easier to comply with the government regulation about serialization of spare parts.
Results
- Mobilized inventory transactions and inquiries.
- Eliminated time-consuming paperwork.
- Complied with regulations that require the serialization of every part on each train.
- Optimized inventory cycle counting, even in locations without Wi-Fi connectivity.
Mobile barcoding would simplify compliance with government regulations for serialization of spare parts.
Sr. Consultant
RFgen SoftwareSolution
RFgen Mobile Foundations for Oracle’s JD Edwards was selected as the best platform to address the challenges. After evaluating three solutions, the company chose RFgen because of its open architecture and flexibility to adapt to the unique needs of its business.
RFgen delivers certified integration with JD Edwards and is highly customizable. For security and tracking purposes, RFgen connects to JD Edwards using a named user configuration, with user accounts authenticated by Microsoft Active Directory.
To comply with the regulation requiring serial numbers on all train parts, the company affixes barcode labels to all inventory items. When inventory is received or consumed, employees scan the attached barcodes and RFgen captures details about the transactions and posts them to JD Edwards in real-time.
The company asked RFgen to customize and implement the solutions in just one month. The RFgen team got to work and delivered a solution that matched their exact requirements while staying on time and budget. The entire solution was deployed in just three weeks.
When inventory is received or consumed, employees can scan barcodes to capture information and posts them to JD Edwards in real time.
Sr. Consultant
RFgen SoftwareResults
The company uses RFgen with mobile devices (Motorola bar code scanners) to receive JD Edwards purchase orders by line. As each line is received, RFgen posts the receipt to JD Edwards and prints out serialized labels for the items received. If the supplier is not ISO certified, a work order is automatically issued to initiate quality control processes.
RFgen also facilitates the issue of spare parts and inventory items from the storeroom to work orders. Technicians can issue their own parts to a repair order using RFgen on a mobile device. This is especially helpful for the nighttime technicians since by using RFgen, they no longer need access to JD Edwards to complete their work.
Using RFgen in its operations has enabled this transportation company to:
- Mobilize inventory transactions and inquiries so workers in the store room and on the shop floor can use JD Edwards without directly accessing a workstation session.
- Eliminate much of the time-consuming paperwork associated with inventory management.
- Comply with regulations that require the serialization of every part on each train.
- Optimize inventory cycle counting, even in locations without Wi-Fi connectivity.
RFgen helps manage inventory throughout the warehouse and storeroom. Using mobile devices, workers can easily perform inventory transfers, issue items out of inventory, and make inquiries about item inventory levels, location, and history by serial number.
The company also automated cycle counting with RFgen. In locations where there is no Wi-Fi connectivity, the RFgen cycle count application is used in a disconnected mode with results cached locally on mobile devices. When finished, the user uploads the cycle count to the RFgen server for processing against JD Edwards.
Based on the success of this project, RFgen is currently being implemented across other divisions of the larger parent company, starting with a division that maintains petroleum industry assets including offshore drilling rigs and pipelines.
Technicians can issue their own parts to a repair order using RFgen on a mobile device. This is especially helpful for the nighttime technicians since by using RFgen, they no longer need access to JD Edwards to complete their work.
Sr. Consultant
RFgen Software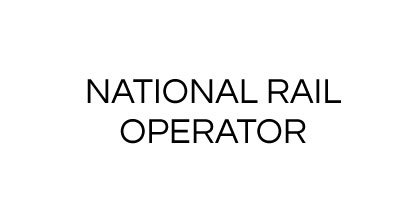
A transportation company is the private operator of an automated rail-based rapid transit system serving a large city and a metropolitan airport. The company warehouses many spare parts to maintain the trains and employs specialized technicians to make repairs and perform preventative maintenance.