Case study
Alliance Resources Partners
Leading U.S. coal mining operation automates inventory management processes for spare parts in Oracle E-Business Suite, maximizing uptime for profit-generating machinery and unearthing warehouse efficiencies.
Results
- Automated inventory control process
- Improved inventory accuracy by 40%
- Increased productivity
- Exceeded adoption expectations across operations
Challenge
Alliance Resource Partners relied on a paper-based tracking system for their inventory management. Each of eight mines maintained an open spare parts warehouse. Inventory counts were often inaccurate, meaning parts weren’t available to repair machinery, impacting productivity, uptime, and ultimately profitability.
“The mechanics would walk into the warehouse, grab their parts, and then hopefully write everything down,” recalls Owen Schlipf, manager of Accounting Business Processes for Alliance Resource Partners, a group of accountants that serve as a critical liaison between IT and Accounting. “The warehouse clerks could never fully trust what was done correctly, so they had to validate the truth by looking up the quantity in Oracle and double-checking it against actual parts on the shelves.”
With a warehouse operating in three shifts, 24/7, and each location employing up to 12 clerks, maintaining accurate inventory data using paper records proved very challenging and required a lot of extra manpower. Warehouse teams would perform quarterly cycle counts by printing out paper inventory reports from Oracle, circulating through the warehouse counting to note discrepancies in quantity, and finally returning to a fixed Oracle terminal to manually enter adjustments.
Schlipf and his team knew there had to be a better way.
“It’s all about mitigating the downtime,” explains Schlipf. “We don’t want mechanics looking for parts that are not actually on the shelf. But we also don’t want to order parts that aren’t needed because there are more on the shelf than in the system.”
Schlipf’s team began looking for an automation solution to save on personnel costs while also increasing accuracy, efficiency and productivity in the warehouse. They also wanted to extend their Oracle EBS workflows throughout the warehouse and receiving areas using mobile devices for automated data collection with barcodes.
Results
- Automated inventory control process
- Improved inventory accuracy by 40%
- Increased productivity
- Exceeded adoption expectations across operations
It's all about mitigating the downtime. We don't want mechanics looking for parts that are not actually on the shelf. But we also don't want to order parts that aren't needed because there are more on the shelf than in the system.
Owen Schlipf
Manager, Accounting Business ProcessesSolution
Alliance Resource Partners selected RFgen Mobile Foundations for Oracle E-Business Suite, a collection of ready-to-use, pre-tested mobile apps validated by Oracle.
“We selected RFgen because of its flexibility and its integration with Oracle EBS,” says Schlipf, “But another huge factor was the RFgen Mobile Development Studio.” With their own in-house IT team, Alliance developers could support, maintain and build on to the solution when new apps or customizations are required without having to wait on third-party vendors.
We selected RFgen because of its flexibility and its integration with Oracle EBS, but another huge factor was the RFgen Mobile Development Studio.
Owen Schlipf
Manager, Accounting Business ProcessesResults
RFgen enabled Alliance Resource Partners to eliminate paper-based processes and digitally automate inventory management for spare parts. Instead of signing a piece of paper or logging into an EBS workstation every time a part is pulled, now transactions automatically update the system in real time with a quick barcode scan. Alliance uses RFgen for issuing out inventory, returns, cycle counting and purchase orders (POs).
Our developers took a look at RFgen and gave us two thumbs up. Other solutions were just not as easy to modify.
Owen Schlipf
Manager, Accounting Business Processes40% Higher Inventory Accuracy
Automating inventory processes and eliminating paper in the warehouse have had a profound impact on inventory accuracy for Alliance Resource Partners. Using RFgen to issue inventory to mechanics, warehouse clerks accompany mechanics through the warehouse, scanning the parts they pull and entering a quantity. RFgen automatically updates inventory in Oracle in real time as each transaction occurs. If unused parts are returned at the end of a shift, it is just as easy to scan them back into inventory.
Significant Efficiency Gains
Automation with RFgen improved warehouse efficiency.
RFgen created a cycle count app that enabled Alliance Resource Partners to improve the efficiency and effectiveness of its cycle count process. As a result, the warehouse team eliminated the paperwork associated with the process.
Now, warehouse clerks can enter, scan or search an item. Clicking a search icon produces a list of items and descriptions. When they enter the quantity of items on the shelf, RFgen defaults to either Write-Up or Write-Off depending on the difference between quantities on hand and inventory levels in Oracle EBS.
“RFgen cycle counting saves time and reduces the risk of error by eliminating manual counting based on a printed report,” Schlipf explained. With four to six employees in each warehouse, this represents a significant efficiency improvement.
This extra efficiency has freed warehouse personnel to focus on tasks that improve the smooth operation of the warehouse.
Doubled Expectations
Alliance Resource Partners gives each facility wide latitude over operational decisions. All mines use the same corporate ERP instance, but other business systems, including RFgen, are adopted at management’s discretion. After a quick adoption by warehouse teams at the first location, the other sites realized the value and ease of implementing RFgen, making implementation an easy choice for each facility. Seven out of eight warehouses have already adopted RFgen, with the eighth planning to implement the solution after an upcoming move to a new location.
“Originally, I estimated a need for 10 to 15 devices, not knowing how many operations would adopt it and how quickly,” explains Schlipf. “Today, we’ve got 39 devices using RFgen, so it more than doubled my original expectation.”
Looking Ahead
This is only the beginning of Alliance Resource Partner’s journey with RFgen. Schlipf is already preparing to expand the use of RFgen in the warehouse with a Requisition application.
“RFgen was an important step to manage our costs and keep on top of our inventory spends,” Schlipf explains. “As we develop additional future uses of RFgen, they will revolve around controlling cost or helping us perform tasks easier, faster and more efficiently.”
Inventory is 40% more accurate with RFgen.
Owen Schlipf
Manager, Accounting Business Processes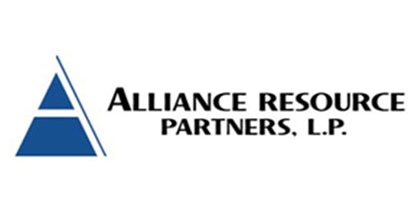
Alliance Resource Partners, L.P. (NASDAQ: ARLP) is a diversified energy company with significant operations in producing and marketing coal to major domestic and international utilities and industrial users. As one of the largest coal mining enterprises in the Eastern United States, Alliance Resource Partners operates eight coal mines that produce roughly 40,000 tons of thermal coal worth approximately $2 billion in revenue each year.