Case study
NLMK USA
Leading global steel manufacturer with a small IT team implements RFgen for Oracle E-Business Suite to track inventory, create mobile apps, and deliver superior customer service in a highly competitive market.
Results
- Transformed inventory management with real-time control and analytics
- Strengthened team’s ability to ship product accurately and on-time
- Improved data accuracy and visibility on finished goods beyond expectations
- Reduced labor time by 60% for cycle counting inventory
- Launched rapid in-house mobile app development with little training
- Supported and enhanced the company goal of delivering superior customer service
Challenge
NLMK USA’s ability to continue delivering superior customer service was slipping because their team was having difficulty tracking and locating finished steel coils, which impacted their ability to stage and load product onto trucks in time for delivery to customers.
NLMK USA operates three busy steel mill facilities in the United States, manufacturing steel coils ranging in size from 30,000 to 50,000 pounds for use as critical components in other manufacturing operations. The company prides itself on being customer-oriented, responsive and lean in a highly competitive marketplace.
“We have a high degree of quality standards and we are here to make our customers happy,” says James Rowe, Director of IT at NLMK USA. “Superior customer service – that’s our niche in the market.”
“Our customers want materials delivered on time,” explains Matthew Hemmerlin, Manager, Special Projects for NLMK USA’s IT department. “Our guys were spending most of their time locating coils, causing us to miss the window of loading time for the trucks. If you start missing on-time deliveries and shipments, the customers aren’t happy. In the last few years, the trucking industry has experienced a dramatic decrease in drivers, so the deadline to get trucks loaded is tight. If you can’t load trucks in time, they will leave.”
They had stopped using their current Telnet-based coil management system because it had become obsolete. Not only did it lack controls for effective tracking, it could only be used with handhelds scanners that were over 25 years old, many of which were broken and unusable.
“We decided we really needed to fix that system,” says Hemmerlin.
Results
- Transformed inventory management with real-time control and analytics
- Strengthened team’s ability to ship product accurately and on-time
- Improved data accuracy and visibility on finished goods beyond expectations
- Reduced labor time by 60% for cycle counting inventory
- Launched rapid in-house mobile app development with little training
- Supported and enhanced the company goal of delivering superior customer service
I was impressed with how quickly we were able to build an application, get it deployed on a device and get it communicating with our business systems. It was very quick, based on my experiences developing from scratch.
Matt Hemmerlin
Manager, Special ProjectsSolution
In order to continue running a cost-effective operation, make tight turnarounds and fulfill customer needs, Hemmerlin set out to find a new inventory tracking solution and mobile app platform for the NLMK USA operation. After conducting thorough research into potential options, Hemmerlin elected to implement RFgen Mobile Foundations for Oracle’s E-Business Suite, a mobility solution that communicates bi-directionally with EBS in real-time.
RFgen would provide Hemmerlin’s team with significant flexibility, the ability to automate data collection using mobile devices and barcodes, and real-time inventory tracking with a short ROI period.
One major selling point for Hemmerlin was how quickly his team would be able to install and deploy new or modified mobile apps using RFgen, including the on-premise server and mobile device clients.
“I was impressed with how quickly we were able to build an application, get it deployed on a device and get it communicating with our business systems,” explains Hemmerlin. “It was very quick, based on my experiences developing from scratch.”
Additionally, RFgen comes equipped with the Mobile Development Studio, a mobile app development platform (MADP) that uses pre-built functions and an easy-to-use UI. Leveraging the flexibility of the RFgen Mobile Unity Platform™, RFgen’s Mobile Development Studio enables even junior-level programmers to easily build and modify mobile apps with little training, driving development productivity increases by 70-percent or more.
Hemmerlin started by introducing RFgen into their Portage, Indiana location to help with conducting nightly cycle counts in storerooms, and soon expanded to tracking coil inventory as well. The success of the RFgen solution prompted Hemmerlin and the team to expand usage to their Pennsylvania headquarters galvanizing operation.
“The RFgen project worked really well in Indiana,” said Hemmerlin. “What started out as one specific, targeted solution we’ve now expanded to different functions across multiple facilities.
The number one feature for us was the ability to rapidly build and develop mobile apps with very little technical training. That's critical for us.
Matt Hemmerlin
Manager, Special ProjectsResults
Delivering Superior Customer Service
RFgen helped NLMK USA uphold its core value of delivering superior customer service across all three U.S. facilities. The ability to accurately store, track and stage coils, conduct cycle counts, and easily modify or create new mobile apps has enabled Hemmerlin, Rowe, and the rest of the NLMK team drive out inefficiencies and run a leaner, tighter operation without negatively impacting the bottom line. Some of the many competitive benefits NLMK USA experienced as a result of implementing RFgen include:
RFgen has definitely improved our delivery to customers to ensure we get their steel out the door when the customers want it.
Matt Hemmerlin
Manager, Special Projects60% Time Savings for Cycle Counts
In order to control inventory, the NLMK team previously conducted an annual physical inventory in a storeroom containing over 10,000 items and parts each Fall. Employees recorded counts with pen and paper, followed by manually entering that data into the ERP system. “It was very time consuming to do once a year,” explains Hemmerlin. “Since using RFgen, we’ve cut our cycle counting time by 60%. What used to take half a day now takes only two or three hours.” RFgen’s real-time inventory data also enabled the team to start generating analytics on those counts. The operation’s ability to track what products are on the shelf, missing or moving at an acceptable rate, has been helpful in driving future improvements. After RFgen, their accuracy rate is 96-100%. “From an IT perspective, what I like best about RFgen is that it communicates with our SQL server and Oracle environment simultaneously,” says Hemmerlin, who believes this to be one of the top features of their RFgen solution.
Enhanced Customer Service Through Inventory Control
RFgen helped enhance delivery at the Sharon Coating facility by enabling the team to accurately track finished coil inventory in real time. This success led them to implement a similar system at other locations.
Rowe describes the former process: “Crane operators would move coils at night. So to track coil movements, a guy went out twice a day to write down coil locations–once in the morning and once at night. That way, on the following day, the team knows what coils to get and from where.”
“Our guys would spend a lot of time searching for coils to get them staged for loading the next day,” adds Hemmerlin. “Our on-time delivery was slipping.”
RFgen made a big difference by freeing employees from spending all day physically looking for coils, allowing them to be redirected onto other, more crucial functions.
“As a tracking system, it’s made a huge difference to be able to physically find our coils on the floor and stage them for shipping,” says Hemmerlin. “That’s been a big change for our process. RFgen has definitely improved our delivery to customers to ensure we get their steel out the door when the customer wants it. [RFgen] has made a big difference.”
Flexible, Rapid Mobile App Deployment
One of the most significant benefits NLMK USA experienced was through the RFgen Mobile Development Studio, an easy-to-use mobile app development platform (MADP) that empowers in-house developers to maintain, modify, create and deploy mobile apps without outside assistance.
“The number one feature for us was the ability to rapidly build and develop applications with very little technical training,” explains Hemmerlin. “That’s critical for us.”
In addition, the RFgen Mobile Development Studio’s standardized approach enables updates, bug fixes and new apps to be pushed out to all devices at once without having to physically obtain the device and update each individually.
“In the old system, we had no ability to make changes to the system,” recalls Hemmerlin. “Now we are free to build and deploy fixes and extra functionality.” Rowe adds: “What’s been really good for us with RFgen, is being able to deploy a mobile platform and handheld devices without building ten different custom little apps, and then trying to deploy and manage them, especially when you don’t have the resources to build those custom one-off applications for your floor employees.”
“From a development standpoint, mobile is not really our wheelhouse,” says Hemmerlin. “If we had to build these applications from scratch, it would have easily doubled or tripled the timeline and possibly the budget,” adds Rowe.
Accurate Data Validation and Control
With their legacy system, data fields were freeform without standardized controls to preserve data consistency.
“Every operator had his own location method,” recalls Hemmerlin. “Some guys would name it location 1-2-3 and another would name it location A-C-D-E, giving us two sets of data for the same location.”
This meant they had no way to verify if inventory IDs were true–or if that inventory even existed at all. It’s no wonder NLMK employees were spending so much time looking for coils on the floor.
Rowe adds: “[Hemmerlin] was able to leverage the RFgen platform to do more validation and control the process. We couldn’t really do that before.”
The RFgen platform enabled the IT team to build in controls around how operators scanned coils and location to prevent duplicated or inaccurate data. To ensure that items were scanned into the correct locations, Hemmerlin introduced a new process that consisted of hanging barcodes from the ceiling which could then be scanned using long-range scanners and validated in Oracle. This way, all coil locations and data sets could be standardized and made uniform throughout their operation.
Conclusion
In the end, Rowe and Hemmerlin felt using RFgen to transform their location tracking and cycle counting processes was a worthwhile investment with a scalable, self-sustaining Mobile App Development Platform solution.
“We’ve been running solid ever since,” adds Hemmerlin. “Overall, I think it was pretty successful.”
“It’s a good solution for a lot of problems we’ve faced here,” he goes on to add. “RFgen has been very responsive from a customer service standpoint. When we have questions, we reach out and get a good response time back from support. Our sales rep has been great.”
RFgen has been very responsive from a customer service standpoint. When we have questions, we reach out and get a good response time back from support. Our sales rep has been great.
Matt Hemmerlin
Manager, Special ProjectsLooking Ahead
The NLMK USA team plans to expand their location tracking to additional facilities as they continue to improve their physical inventory control process.
“We know we have a good platform to do these things on,” says Hemmerlin.
Rowe adds: “With this tool in our toolbelt, as things come up when we need to do something mobile or do something custom outside of Oracle and make it more mobile-friendly, we have this tool we can leverage to build apps very easily–as opposed to going out and trying to look for a tool every time we need to do something on a device.”
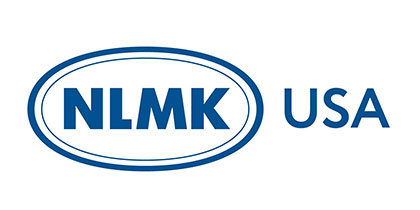
NLMK USA is a division of NLMK International, also known as Novolipetsk Steel (“NLMK”), a leading global manufacturer of high-quality flat-rolled steel products essential to modern manufacturing. With three facilities in the U.S., NLMK USA operates over two million square feet of manufacturing space with a production capacity of 2.7-million tons annually. They pride themselves on delivering superior customer service while retaining a focus on responsible leadership and sustainable development while supplying steel coils for the construction, automotive, pipe and tube, and heavy equipment industries in the United States.