Case study
Brabant Alucast
Automotive parts supplier boosts stock reliability to 96%+ with RFgen for Microsoft Dynamics.
Results
- Increased employee satisfaction
- Enhanced regulatory compliance
- Reduced overhead costs
- Increased operational flexibility
- Reduced staffing costs due to elimination of manual processes
Challenge
European automotive parts manufacturer Brabant Alucast worked with a legacy ERP system that was only partially automated. The fork truck drivers in their Oss and Heijen plants recorded all dislocated stock on paper and their logistics department processed the information manually into the computer system. This process was prone to clerical and typing errors.
To ensure accurate stock records, Brabant Alucast had to perform manual stock checks every month that were still fraught with inaccuracies. If the company had more stock than expected, it was wasted overhead. But if Brabant had less than expected, this created bigger problems because the automotive industry has very tight restrictions when it comes to delivery times and accuracy.
Results
- Increased employee satisfaction
- Enhanced regulatory compliance
- Reduced overhead costs
- Increased operational flexibility
- Reduced staffing costs due to elimination of manual processes
Solution
Brabant Alucast was already in the process of replacing the legacy ERP with Microsoft Dynamics. Now, they wanted to add mobile barcode scanning to reduce errors and eliminate manual stock checks. This led them to select RFgen Mobile Foundations for Microsoft Dynamics. Through a combination of barcode scanning, mobile apps, and hardware, RFgen automates workflows for greater accuracy and efficiency.
The implementation went well and was on schedule throughout the carefully managed RFgen project timeline. “We kept the system flexible to have the option to make more improvements in the future, with more options to optimize processes even further,” explains Andre Voskes, the project lead for Brabant Alucast.
“We gave our fork truck drivers the scanners and said ‘go and play with it’. They learned to work with it very fast and were very enthusiastic. Now with the scanners, they can continue their work without any problems,” he continues.
We gave our fork truck drivers the scanners and said 'go and play with it.' They learned to work with it very fast and were very enthusiastic.
Andre Voskes, Project Lead
Brabant AlucastResults
Six months after the implementation, stock reliability increased from 70% to 96% and is still rising.
Other key achievements include:
- Increased employee satisfaction
- Enhanced regulatory compliance
- Reduced overhead costs
- Increased operational flexibility
- Reduced staffing costs due to elimination of manual processes
Brabant’s future plans include integrating the rest of their business processes, including suppliers and buyers, with RFgen. Most importantly, “a stock reliability of 100% is now realistic,” enthuses Voskes.
After the implementation, stock reliability increased from 70% to 96% and is still rising.
Andre Voskes, Project Lead
Brabant Alucast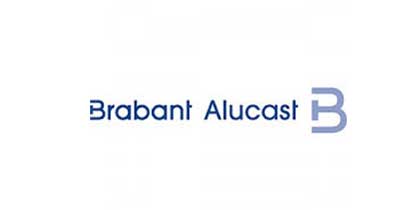
Brabant Alucast International, based in Oss, Netherlands, was originally a family business but has now been part of Volvo for many years and has expanded strongly internationally. During this early period, the company specialized in molding and in CNC operations and assembly. When the automotive industry turned its focus on core design and assembly, the company became autonomous and continued under the name, Brabant Alucast International, which now owns seven factories worldwide of which three are in the Netherlands. The company supplies car engines, car engine parts, and body parts to most of the major automotive manufacturers.