Case study
Remington Arms
Firearm manufacturer solves logistics issues using automated data collection for its ERP.
Results
- Warehouse staff productivity increased 10%, exceeding it’s
original goal - Shipping accuracy increased by as much as 8%
- Costs of the staff to manage the warehouse was reduced by 15%
- Enhanced responsiveness to customer needs
- Tightened supply chain management
- Increased accuracy of product information
Challenge
One of the ongoing challenges facing Remington and its retail supply chain is maintaining the optimum level of inventory. After parts and products are produced and delivered to distribution centers, the data must be counted, collected, organized and distributed as quickly as possible to narrow the gap between the time products are ordered and when products are delivered to retail outlets.
In order to deliver product purchasing and supply requests to the retail outlets more efficiently, Remington decided to consolidate two regional warehouses in Little Rock, AR and Syracuse, NY into a 300,000 square foot central distribution center in Memphis, TN. Combining two warehouses created a daunting data collection process which could cause extensive trouble managing the flow of the supply chain.
To hedge this concern, Remington began looking for a supply chain management technology solution that would accomplish the following:
- 5% increase in productivity and a 5% increase in shipping accuracy
- Provide process efficiencies reducing the workforce needed to run the new warehouse
- Enable management of the data collection process using existing Intermec RF data collection terminals and seamlessly integrate with current Remington database systems
Remington evaluated data collection software that was compatible with their data collection terminals, flexible enough to handle complex shipments with different parts and products in a single pallet, and sophisticated enough to manage the regulatory requirements regarding serial numbers of all completely manufactured firearms.
Results
- Warehouse staff productivity increased 10%, exceeding it’s
original goal - Shipping accuracy increased by as much as 8%
- Costs of the staff to manage the warehouse was reduced by 15%
- Enhanced responsiveness to customer needs
- Tightened supply chain management
- Increased accuracy of product information
Solution
The software Remington chose to implement was RFgen. Due to its open architecture, RFgen easily adapted to Remington’s supply chain requirements. The newly combined warehouse started using RFgen to automatically collect data beginning with tracking inventory receipts, movements, queries, shipments and serial numbers from the Little Rock and Syracuse warehouses. In addition, RFgen integrated the data seamlessly within the Remington database that saved countless hours on installation and gave a fully functioning solution in less time than expected.
Efficient distribution is an essential key of profitable supply chain operations. RFgen provides Remington with a real-time system that works with all of their existing data collection equipment to fuel a new, efficient distribution center.
Among the key considerations Remington used for selecting RFgen was that the technology accomplished the following:
- RFgen software was compatible with current data collection devices
- RFgen technology proved to be intuitive, facilitating an easy training process for the warehouse staff. Ability to remain compliant with the Bureau of Alcohol, Tobacco and Firearms (ATF) regarding tracking the serial numbers of all completely manufactured firearms and the locations where they are shipped.
Results
The results as measured by Remington show that the implementation of RFgen has led to:
- Warehouse staff productivity increased 10%, exceeding its original goal of 5%
- Shipping accuracy increased by as much as 8%, exceeding its original goal of 5%
- Significantly reduced costs as the staff to manage the warehouse was reduced by 15%
Moreover, with tighter inventory tracking built into the supply chain, Remington has more real-time information to make faster decisions including:
- Enhanced responsiveness to customer needs
- Tightened supply chain management
- Faster and more accurate product information
Warehouse staff productivity increased 10%!Remington Arms
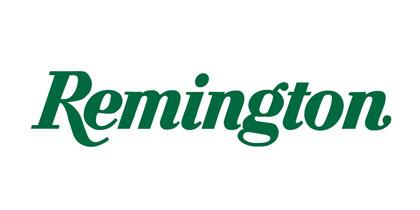
Remington continues to set the standard for the firearms industry. From the best selling firearm of all time, the Remington Model 870 pump shotgun to the world class Remington Model 700 bolt-action rifle, Remington maintains the supply chain and inventory control for more than 300 models of firearms and more than 5,000 firearms parts. However, Remington is not just firearms; the company also produces and supplies hundreds of types of ammunition and accessories.